Method for synthesizing allylamine using transfer line reactor
A pipeline reactor and allylamine technology, which is applied in the preparation of amino-substituted functional groups, organic chemistry, etc., can solve the problems of high raw material costs, serious pollution emissions, etc., and achieve good safety effects
- Summary
- Abstract
- Description
- Claims
- Application Information
AI Technical Summary
Problems solved by technology
Method used
Image
Examples
Embodiment 1
[0027] Embodiment 1: A kind of method utilizing pipeline reactor to prepare allylamines, reaction process is as follows:
[0028]Take allyl chloride 1000g (13.1mol), catalyst 25g, solvent methanol 2000g, liquid ammonia 4454g (262mol). The reactor adopts a pipeline reactor, and the feed adopts a metering pump. Keep the temperature of the reactor jacket at 90°C, adjust the flow rate, divide the above raw materials into two groups and pour them into the pipeline reactor at the same time, the system pressure is 1.2Mpa, and the reaction residence time is 12 minutes. Sampling and analysis showed that the conversion rate of raw material allyl chloride was 99.9%. Rectify the synthetic liquid, extract 433g of allylamine from the fraction at 52-55°C, extract 241.4g of diallylamine from the fraction at 107-111°C, and obtain 23.9g of triallylamine as a by-product, accounting for 3.4% of the product %.
Embodiment 2
[0029] Embodiment 2: a kind of method utilizing pipeline reactor to prepare allylamines, reaction process is as follows:
[0030] Take 1000g (13.1mol) of allyl chloride, 33g of catalyst, 200g of solvent ethanol, and 3340.5g (196.5mol) of liquid ammonia. The reactor adopts a pipeline reactor, and the feed adopts a metering pump. Keep the reactor jacket temperature at 80°C, adjust the flow rate, divide the above raw materials into two groups and pour them into the pipeline reactor at the same time, the system pressure is 1.0Mpa, and the reaction residence time is 9 minutes. Sampling and analysis showed that the conversion rate of raw material allyl chloride was 99.85%. The synthetic liquid was rectified, and 395.8g of allylamine was obtained by extracting the fraction at 52-55°C, 260.5g of diallylamine was obtained at the fraction of 107-111°C, and 35.9g of triallylamine as a by-product, accounting for 4% of the product 5.1%.
Embodiment 3
[0031] Embodiment 3: a kind of method utilizing pipeline reactor to prepare allylamines, reaction process is as follows:
[0032] Take allyl chloride 1000g (13.1mol), catalyst 45g, solvent 2000g, liquid ammonia 2227g (131mol). The reactor adopts a pipeline reactor, and the feed adopts a metering pump. Keep the temperature of the reactor jacket at 75°C, adjust the flow rate, divide the above raw materials into two groups and pour them into the pipeline reactor at the same time, the system pressure is 0.95Mpa, and the reaction residence time is 10 minutes. Sampling and analysis showed that the conversion rate of raw material allyl chloride was 99.79%. The synthetic liquid was rectified, and 365.8g of allylamine was obtained by mining the fraction at 52-55°C, 273.2g of diallylamine was obtained at the fraction of 107-111°C, and 47.8g of triallylamine as a by-product, accounting for 10% of the product 6.9%.
PUM
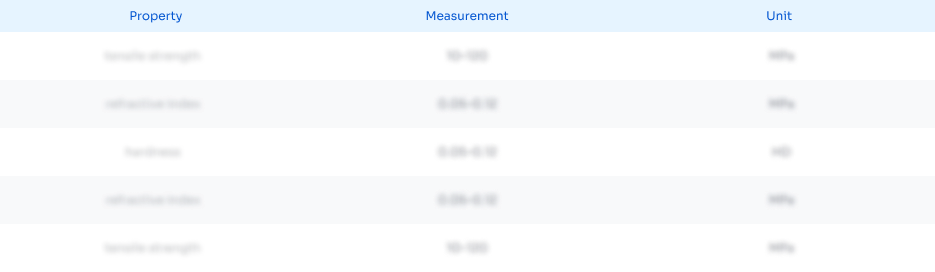
Abstract
Description
Claims
Application Information

- R&D
- Intellectual Property
- Life Sciences
- Materials
- Tech Scout
- Unparalleled Data Quality
- Higher Quality Content
- 60% Fewer Hallucinations
Browse by: Latest US Patents, China's latest patents, Technical Efficacy Thesaurus, Application Domain, Technology Topic, Popular Technical Reports.
© 2025 PatSnap. All rights reserved.Legal|Privacy policy|Modern Slavery Act Transparency Statement|Sitemap|About US| Contact US: help@patsnap.com