Preparation method of micro member for MEMS
A technology of micro-electronic machinery and micro-components, applied in micro-structure technology, micro-structure device, manufacturing micro-structure device, etc., can solve the problem of high equipment investment, achieve high dimensional accuracy, loose process conditions, and wide application.
- Summary
- Abstract
- Description
- Claims
- Application Information
AI Technical Summary
Problems solved by technology
Method used
Examples
Embodiment 1
[0009] Embodiment 1. The making of micro-cross:
[0010] 1) Fabrication of microelectronic mechanical photoresist patterns:
[0011] Under the background vacuum degree of 7.0E-3, working air pressure of 5Pa, sputtering power of 110W, target distance of 14 cm, and time of 26 minutes, a metal substrate was sputtered on a silicon substrate by magnetron sputtering ( Substrate material can be selected iron, nickel etc.), present embodiment selects iron substrate for use, and substrate thickness is between 30-100nm; Then clean with deionized water, get rid of the negative photoresist of certain thickness; The patterned chromium plate is used as a mask, and ultraviolet light with a wavelength of 400nm is used as the exposure light source, and the exposure time is 45s. This embodiment adopts wet development, and the developing solution is the RFX-2277 negative film developing solution produced by Suzhou Ruihong Electronic Chemicals Co., Ltd., a Sino-Japanese joint venture. ethyl est...
Embodiment 2
[0024] Embodiment 2. The making of microgear nickel member:
[0025] 1) Fabrication of microelectronic mechanical photoresist patterns:
[0026] Under the conditions of background vacuum degree of 6.0E-3, working pressure of 10Pa, sputtering power of 200W, target distance of 20cm, and time of 50 minutes, a layer of metal nickel substrate was sputtered on the silicon substrate by magnetron sputtering method. , the thickness of the substrate is between 30-100nm; then wash it with deionized water; use a negative photoresist, use a chromium plate with a micro-gear pattern as a mask, and use ultraviolet light with a wavelength of 400nm as the exposure light source, and the exposure time is 90s . This embodiment adopts wet development, and the developing solution is the RFX-2277 negative film developing solution produced by Suzhou Ruihong Electronic Chemicals Co., Ltd., a Sino-Japanese joint venture. ethyl ester, and then washed with deionized water to obtain a negative photoresis...
Embodiment 3
[0039] Embodiment 3. The making of micro-gear-shaped metal member:
[0040] 1) Fabrication of microelectronic mechanical photoresist patterns:
[0041] Under the conditions of background vacuum ≥ 5.0E-3, working pressure 0.1Pa, sputtering power 20W, target distance 5 cm, time 5 minutes, sputter a layer of metal substrate on silicon substrate by magnetron sputtering method (substrate material can be selected iron, nickel etc. for use), present embodiment selects iron substrate for use, and substrate thickness is between 30-100nm; Then clean with deionized water, with negative photoresist; The chromium plate is used as a mask, and ultraviolet light with a wavelength of 400nm is used as the exposure light source, and the exposure time is 60s. In this embodiment, wet development is adopted. After development, fixation is carried out in a fixing solution, and then washed with deionized water to obtain a negative photoresist pattern on the substrate.
[0042] 1) Fabrication of mic...
PUM
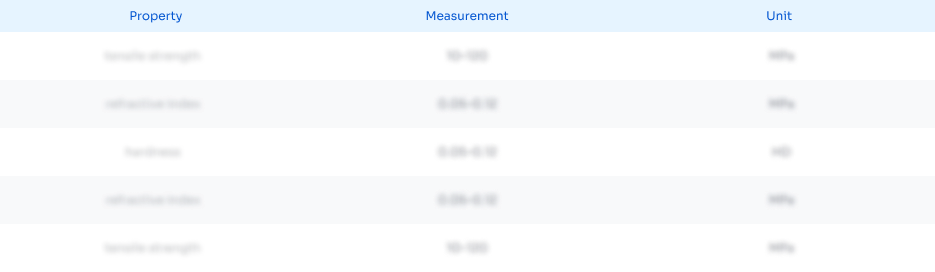
Abstract
Description
Claims
Application Information

- Generate Ideas
- Intellectual Property
- Life Sciences
- Materials
- Tech Scout
- Unparalleled Data Quality
- Higher Quality Content
- 60% Fewer Hallucinations
Browse by: Latest US Patents, China's latest patents, Technical Efficacy Thesaurus, Application Domain, Technology Topic, Popular Technical Reports.
© 2025 PatSnap. All rights reserved.Legal|Privacy policy|Modern Slavery Act Transparency Statement|Sitemap|About US| Contact US: help@patsnap.com