Method for preparing composite powder of nano tungsten carbide-coblt through direct reducition and carbonization
A composite powder and cobalt nanotechnology, which is applied in the field of direct reduction carbonization of tungsten carbide-cobalt nanocomposite powder, can solve the problems of high energy consumption, high cost, uneven mixing of WC and Co, and achieve simple and safe process control. The effect of broad utility
- Summary
- Abstract
- Description
- Claims
- Application Information
AI Technical Summary
Problems solved by technology
Method used
Image
Examples
Embodiment 1
[0040] Embodiment 1: ammonium metatungstate AMT ((NH 4 ) 6 (H 2 W 12 o 40 )·4H 2 O), hydrated cobalt nitrate Co(NO 3 ) 2 ·6H 2 The O raw material is miscible in distilled water according to the mass ratio of 2.34:1, and is made into composite oxide powder through spray pyrolysis. The composite powder and carbon powder were weighed according to the mass ratio W:C=23:6, Co:C=59:24, put into a ball mill for dry grinding for 120 hours (material: ball=1:2), and the obtained mixed powder was N 2 After carbonization at 950°C for 4 hours in a fixed bed under atmosphere, the temperature was lowered to 600°C, and H 2 Insulated for 4 hours for carbon washing, followed by N 2 It was cooled to room temperature in the atmosphere, thereby preparing WC-10Co composite powder.
Embodiment 2
[0041] Embodiment 2: ammonium paratungstate APT ((NH 4 ) 10 (H 2 W 12 o 42 )·4H 2 O), cobalt acetate hydrate Co(CH 3 COO) 2 4H 2 O, ammonium metavanadate NH 4 VO 3 The raw materials are miscible in distilled water according to the mass ratio of 132:11:1, spray-dried to make composite oxide powder, put it in a vacuum furnace at 200°C for 12 hours, and mix the composite powder and carbon powder according to the mass ratio W: C = 23: 6, Co: C = 59: 24, V: C = 51: 42 Weigh it, put it into a ball mill, and use ethanol as the wet grinding medium for wet grinding for 72 hours (material: ball: liquid = 1: 2:0.5), the powder obtained after drying was carbonized at 800°C for 6 hours in a rotary furnace under Ar atmosphere, cooled to 800°C, and CO 2 and CO mixed gas (CO accounted for 0.3vol%) insulation for 2 hours for carbon washing, followed by N 2 It was cooled to room temperature in the atmosphere, thereby preparing WC-3Co-0.5VC composite powder.
Embodiment 3
[0042] Example 3: 3CoWO 4 ·5WO 3 , cobalt chloride hydrate CoCl 2 ·6H 2 O, Chromium Chloride Hydrate CrCl 3 ·6H 2 O is miscible in distilled water at a weight ratio of 60:100:1, spray-dried to make a composite oxide powder, put it in a microwave oven and burn at 500°C for 0.5 hours, and then mix the composite powder and carbon powder according to the mass ratio W: C = 23: 6, Co: C = 59: 24, Cr: C = 59: 26 Weigh it, put it into a ball mill, and use acetone as the wet grinding medium for wet grinding for 60 hours (material: ball: liquid = 1: 20:10), the powder obtained after drying was in N 2 After carbonization at 800°C for 5 hours in a fluidized furnace under atmosphere, H 2 and CH 4 mixed gas (CH 4 accounted for 0.1vol%), kept in this atmosphere for 2 hours for carbon washing, and then cooled to room temperature in Ar atmosphere, thus producing WC-40Co-0.3Cr 3 C 2 Composite powder.
PUM
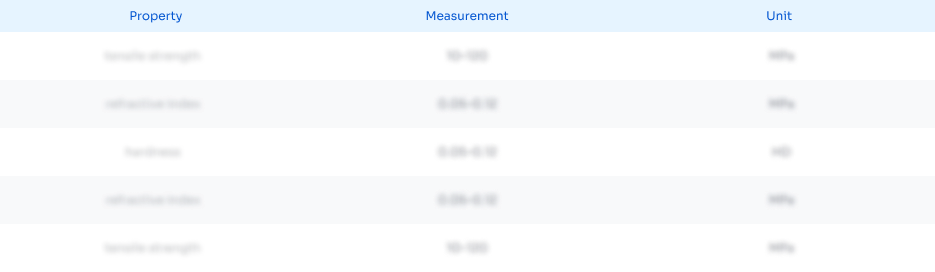
Abstract
Description
Claims
Application Information

- R&D
- Intellectual Property
- Life Sciences
- Materials
- Tech Scout
- Unparalleled Data Quality
- Higher Quality Content
- 60% Fewer Hallucinations
Browse by: Latest US Patents, China's latest patents, Technical Efficacy Thesaurus, Application Domain, Technology Topic, Popular Technical Reports.
© 2025 PatSnap. All rights reserved.Legal|Privacy policy|Modern Slavery Act Transparency Statement|Sitemap|About US| Contact US: help@patsnap.com