Core-shell catalyst as well as preparation method and application thereof
A core-shell catalyst and catalyst technology, applied in catalyst activation/preparation, catalyst, catalytic reaction, etc., can solve the problems of reducing catalytic activity, methanol selectivity, life limit, etc.
- Summary
- Abstract
- Description
- Claims
- Application Information
AI Technical Summary
Problems solved by technology
Method used
Image
Examples
Embodiment 1
[0092] Using 5g copper nitrate trihydrate and 6.2g zinc nitrate hexahydrate as raw materials (Cu / Zn=1:1, molar ratio), 6.5gH 3 BTC is an organic ligand, 80ml dimethylformamide (DMF), 80ml ethanol (EtOH) and 80ml deionized water are used as solvents, the above mixture is transferred to a polytetrafluoroethylene reactor, and CuZnO / HKUST- 1 catalyst precursor. Wherein, the temperature is 110° C., and the time is 12 hours. The solvothermal catalyst was filtered, washed and dried at 400 °C in N 2 Roasting in the atmosphere (80ml / min) for 3h and passing through 5wt%H 2 (The mixed gas is composed of hydrogen and nitrogen) reduction at 220 ° C for 10 h, passivation at room temperature overnight, the organic framework of the catalyst precursor is changed into a core-shell structure coated with Cu / ZnO, and the core-shell catalyst CuZnO / HKUST-1. The catalyst (3.0g) will be further subjected to CO / CO in a liquid-phase slurry-bed reactor and a gas-solid-phase fixed-bed reactor. 2 / H ...
Embodiment 2
[0094] Using 4.1g copper acetate monohydrate and 4.6g zinc acetate dihydrate as raw materials (Cu / Zn=1:1, molar ratio), 6.5gH 3 BTC is the organic ligand, 80ml DMF, 80ml EtOH and 80ml deionized water are used as the solvent, the above mixture is transferred to a polytetrafluoroethylene reactor, and the ZnO / HKUST-1 catalyst precursor is prepared by solvothermal method. Wherein, the temperature is 110° C., and the time is 12 hours. The solvothermal catalyst was filtered, washed and dried at 400 °C in N 2 Roasting in the atmosphere (80ml / min) for 3h and passing through 5wt%H 2 (The mixed gas is composed of hydrogen and nitrogen) reduction at 220 ° C for 10 h, passivation at room temperature overnight, the organic framework of the catalyst precursor is changed into a core-shell structure coated with Cu / ZnO, and the core-shell catalyst CuZnO / HKUST-1-AC. The catalyst (3.0g) will be further subjected to CO / CO in a liquid-phase slurry-bed reactor and a gas-solid-phase fixed-bed re...
Embodiment 3
[0096] Using 6.2g zinc nitrate hexahydrate as raw material, 5.2g H 2 BDC was the organic ligand, 80ml DMF was the solvent, and the MOF-5 catalyst precursor was prepared by solvothermal method. Wherein, the temperature is 110° C., and the time is 12 hours. The above mixture was transferred to a polytetrafluoroethylene reactor, and the MOF-5 catalyst precursor was prepared by a solvothermal method. After the solvothermal catalyst was filtered, washed and dried, 5g of copper nitrate trihydrate (Cu / Zn=1:1, molar ratio) was used as raw material, dissolved in 50ml of deionized water, and the catalyst precursor was prepared by ultrasonic-assisted excessive impregnation method Bulk Cu / MOF-5. at 400°C in N 2 Roasting in the atmosphere (80ml / min) for 3h and passing through 5wt%H 2 (The mixed gas is composed of hydrogen and nitrogen) Reduction at 220 °C for 10 h, passivation at room temperature overnight, the organic framework of the catalyst precursor becomes a core-shell structure ...
PUM
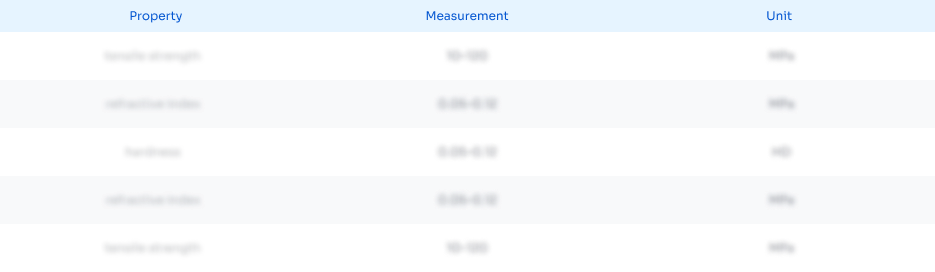
Abstract
Description
Claims
Application Information

- R&D
- Intellectual Property
- Life Sciences
- Materials
- Tech Scout
- Unparalleled Data Quality
- Higher Quality Content
- 60% Fewer Hallucinations
Browse by: Latest US Patents, China's latest patents, Technical Efficacy Thesaurus, Application Domain, Technology Topic, Popular Technical Reports.
© 2025 PatSnap. All rights reserved.Legal|Privacy policy|Modern Slavery Act Transparency Statement|Sitemap|About US| Contact US: help@patsnap.com