Environment-friendly type high-temperature denitrification catalyst and preparation method thereof
An environment-friendly, denitration catalyst technology, which is applied in the field of environmental protection catalytic materials and air pollution prevention and control, can solve the problems of complex preparation process, poor high temperature activity, narrow catalyst activity temperature window, etc., and achieve the effect of simple preparation process and reduced harm
- Summary
- Abstract
- Description
- Claims
- Application Information
AI Technical Summary
Problems solved by technology
Method used
Image
Examples
Embodiment 1
[0033] (1) Preparation of carrier
[0034] With the mass percentage of titanium dioxide / gamma alumina as 1:10%, weigh 30g of titanium dioxide and 3g of gamma alumina respectively, and mix them uniformly to obtain a catalyst carrier;
[0035] (2) Preparation of tungsten-zirconium composite ion precursor solution
[0036] Screen and weigh 0.46g of ammonium paratungstate and 1.50g of deionized water to mix, stir evenly until the solution is clear and transparent, and obtain solution A;
[0037] Screen and weigh 2.26g of zirconium chloride and add 4.71g of deionized water to mix, stir evenly until the solution is clear and transparent, and obtain solution B;
[0038] Wherein the ion molar ratio of the A and B solutions is 1:1.5, the solution B is added to the solution A, and the dropping process needs to be stirred to obtain a tungsten-zirconium saturated solution;
[0039] (3) Catalyst sludge preparation and pretreatment
Embodiment 2
[0046] (1) Preparation of cocatalyst precursor ion solution
[0047] Screen and weigh 1.51g of erbium chloride hexahydrate and 0.70g of tin tetrachloride pentahydrate, dissolve in 5g of deionized water, stir and dissolve until the solution is clear and transparent, and obtain a co-catalyst precursor solution;
[0048] (2) Preparation of carrier
[0049] Take by weighing 30g titanium dioxide and impregnate in equal volume with the co-catalyst solution prepared in step (1), after drying and pulverizing, mix it with 1.5g gamma alumina to obtain a catalyst carrier, wherein titanium dioxide / co-catalyst The mass percent of / gamma alumina is 1:3%:5%;
[0050] (3) Preparation of tungsten-zirconium composite ion precursor solution
[0051] Screen and weigh 4.14g of ammonium tungstate and 6.22g of deionized water to mix, stir evenly until the solution is clear and transparent, and obtain solution A;
[0052] Screen and weigh 5.73g of zirconium oxychloride and add 8.61g of deionized w...
Embodiment 3
[0061] (1) Preparation of cocatalyst precursor ion solution
[0062] Screen and weigh 0.33g of barium nitrate and 0.15g of erbium chloride hexahydrate, dissolve them in 3g of deionized water, place them in a constant temperature water bath at 85°C, stir and dissolve until the solution is clear and transparent, and obtain a co-catalyst precursor solution ;
[0063] (2) Preparation of carrier
[0064] Take by weighing 30g titanium dioxide and impregnate in equal volume with the co-catalyst solution prepared in the step (1), after drying and pulverizing, mix it with 9g gamma alumina to obtain a catalyst carrier, wherein titanium dioxide / co-catalyst / The mass percent of gamma alumina is 1:1%:30%;
[0065] (3) Preparation of tungsten-zirconium composite ion precursor solution
[0066] Screen and weigh 1.86g of ammonium metatungstate and 2.79g of deionized water to mix, stir evenly until the solution is clear and transparent, and obtain solution A;
[0067] Screen and weigh 2.19...
PUM
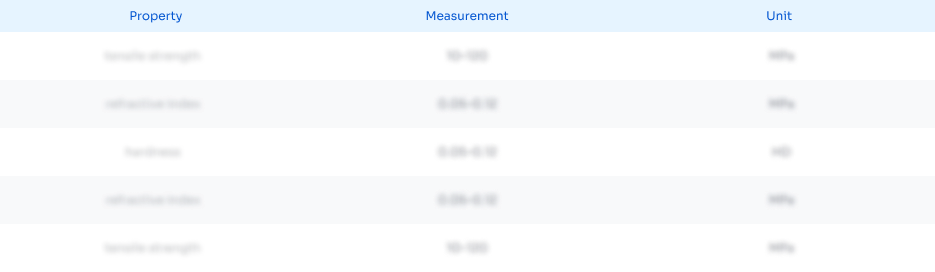
Abstract
Description
Claims
Application Information

- R&D
- Intellectual Property
- Life Sciences
- Materials
- Tech Scout
- Unparalleled Data Quality
- Higher Quality Content
- 60% Fewer Hallucinations
Browse by: Latest US Patents, China's latest patents, Technical Efficacy Thesaurus, Application Domain, Technology Topic, Popular Technical Reports.
© 2025 PatSnap. All rights reserved.Legal|Privacy policy|Modern Slavery Act Transparency Statement|Sitemap|About US| Contact US: help@patsnap.com