Surface pretreatment method for improving abrasion resistance of automobile brake pad
A technology for surface pretreatment and automobile brakes, applied in heat treatment furnaces, heat treatment equipment, furnaces, etc., can solve the problems of low mechanical properties of brake pads, increase the preparation process, affect the use effect, etc., and achieve good safety and chemical stability Strong resistance and prolonging the service life
- Summary
- Abstract
- Description
- Claims
- Application Information
AI Technical Summary
Problems solved by technology
Method used
Examples
Embodiment 1
[0024] The surface pretreatment method that present embodiment improves the wear resistance of automobile brake pads comprises the following steps:
[0025] S1. Heat-treat the brake pad blank obtained by molding, put the brake pad blank into an electric furnace to heat, the heating temperature is 450°C, and the heating time is 9h, cool the brake pad blank after heat treatment, and firstly heat it on a drilling machine Drilling and chamfering, and then moving to the grinding machine to remove flash and burrs, and get pre-treated brake pads;
[0026] S2. The brake pads pretreated in step S1 are subjected to frosting treatment and cleaning treatment. After cleaning, the brake pads are placed in an electric furnace, and the temperature is raised to 750°C once, and the holding time is 65min. After 41 minutes, cool down to room temperature at a rate of 40°C / min, then raise the temperature to 550°C three times, keep warm for 20 minutes, and air-cool to room temperature with the furna...
Embodiment 2
[0032] The surface pretreatment method that present embodiment improves the wear resistance of automobile brake pads comprises the following steps:
[0033] S1. Heat-treat the brake pad blank obtained by molding, put the brake pad blank into an electric furnace to heat, the heating temperature is 490°C, and the heating time is 10h, cool the brake pad blank after heat treatment, and firstly heat it on a drilling machine Drilling and chamfering, and then moving to the grinding machine to remove flash and burrs, and get pre-treated brake pads;
[0034] S2. The brake pads pretreated in step S1 are subjected to frosting treatment and cleaning treatment. After the cleaning treatment, the brake pads are placed in an electric furnace, and the temperature is raised to 850° C. for 70 minutes, and then the temperature is raised to 1010° C. for the second time. After 45 minutes, cool down to room temperature at a rate of 40°C / min, then raise the temperature to 570°C three times, keep warm...
Embodiment 3
[0040] The surface pretreatment method that present embodiment improves the wear resistance of automobile brake pads comprises the following steps:
[0041] S1. Heat-treat the brake pad blank obtained by molding, put the brake pad blank into an electric furnace to heat, the heating temperature is 470°C, and the heating time is 9.5h. Cool the brake pad blank after heat treatment, and first place it on a drilling machine. Carry out drilling and chamfering treatment, and then move to the grinding machine to remove flash and burrs, and obtain pre-treated brake pads;
[0042] S2. The brake pads pretreated in step S1 are subjected to frosting treatment and cleaning treatment. After the cleaning treatment, the brake pads are placed in an electric furnace, and the temperature is raised to 800° C. for 68 minutes, and then the temperature is raised to 995° C. for the second time. After 43 minutes, cool down to room temperature at a rate of 40°C / min, then raise the temperature to 560°C t...
PUM
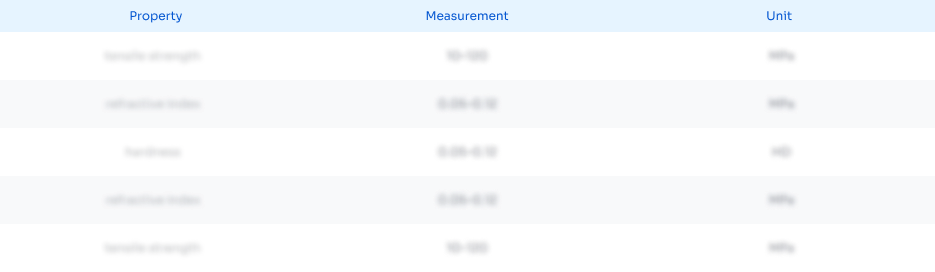
Abstract
Description
Claims
Application Information

- R&D
- Intellectual Property
- Life Sciences
- Materials
- Tech Scout
- Unparalleled Data Quality
- Higher Quality Content
- 60% Fewer Hallucinations
Browse by: Latest US Patents, China's latest patents, Technical Efficacy Thesaurus, Application Domain, Technology Topic, Popular Technical Reports.
© 2025 PatSnap. All rights reserved.Legal|Privacy policy|Modern Slavery Act Transparency Statement|Sitemap|About US| Contact US: help@patsnap.com