A kind of metamaterial and its manufacturing method
A manufacturing method and metamaterial technology, applied in the direction of manufacturing tools, instruments, optical components, etc., can solve problems such as high cost and complicated preparation process, and achieve the effects of low yield rate, convenient iteration, and low iteration cost
- Summary
- Abstract
- Description
- Claims
- Application Information
AI Technical Summary
Problems solved by technology
Method used
Image
Examples
preparation example Construction
[0026] The preparation method of the metamaterial provided by the present invention comprises the following steps:
[0027] like figure 1 Step S101 and figure 2 As shown in step S201, at least one of the wave absorbing agent powder and the metal electrode powder, and the insulating substrate powder are respectively added to the thermoplastic resin, mixed uniformly, and used as raw materials; wherein the wave absorbing agent powder includes carbon fiber One or more combinations of powder, silicon carbide fiber powder or polycrystalline iron fiber powder. Metal electrode powders include: one or more combinations of titanium, vanadium, chromium, zirconium, niobium, molybdenum, hafnium, tantalum or tungsten powders. The insulating substrate powder includes one or more combinations of polyimide, polyester, polyurethane, epoxy resin or polymethyl methacrylate powder. Thermoplastic resins include polyethylene, polypropylene, polyvinyl chloride, polystyrene, polymethyl methacrylat...
Embodiment 1
[0032] Example 1: Preparation of Resin-Based Impedance Matching Metamaterials
[0033] 1. Add carbon fiber powder, tungsten powder, and epoxy resin powder to polyethylene resin, mix them evenly, and adjust them to have similar rheological properties as raw materials. Among them, carbon fiber powder, tungsten powder, and epoxy resin powder The ratio of the sum of mass to the mass of polyethylene resin is 0.28, the mass ratio of carbon fiber powder and tungsten powder to the mass of epoxy resin powder is 1:4, and the mass ratio of carbon fiber powder to tungsten powder It is 1:3.
[0034] 2. According to the microstructure design of the metamaterial, add the above-mentioned raw materials into the mold, and use a co-extrusion process to form a rod-shaped material with a microstructure unit with a clear interface.
[0035] 3. A number of (4×4, 5×5, etc.) microstructure unit rods are densely packed into the extruder, and the arrangement is the designed periodic arrangement of the ...
Embodiment 2
[0039] Example 2: Preparation of Curved Surface Resin-Based Impedance Matching Metamaterials
[0040] 1. Add silicon carbide fiber powder, titanium powder, and polyimide powder to polymethyl methacrylate resin, mix evenly, and adjust it to have similar rheological properties as raw materials, wherein silicon carbide fiber powder, The ratio of the sum of the mass of titanium powder and polyimide powder to the mass of polymethyl methacrylate resin is 0.36, and the ratio of the sum of the mass of carbon fiber powder and tungsten powder to the mass of epoxy resin powder is 4 : 1, the mass ratio of carbon fiber powder to tungsten powder is 1:4.
[0041] 2. According to the microstructure design of the metamaterial, add the above-mentioned raw materials into the mold, and use a co-extrusion process to form a rod-shaped material with a microstructure unit with a clear interface.
[0042] 3. A number of (4×4, 5×5, etc.) microstructure unit rods are densely packed into the extruder, a...
PUM
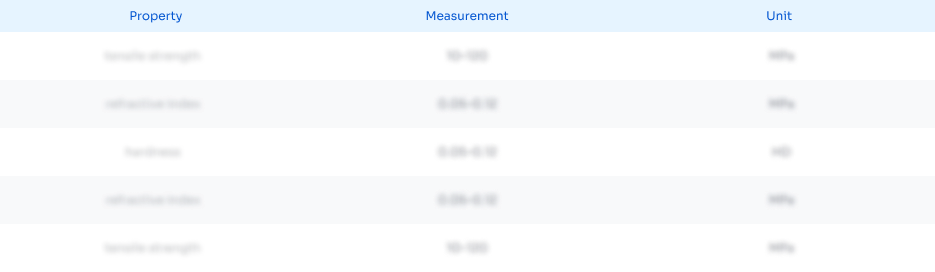
Abstract
Description
Claims
Application Information

- Generate Ideas
- Intellectual Property
- Life Sciences
- Materials
- Tech Scout
- Unparalleled Data Quality
- Higher Quality Content
- 60% Fewer Hallucinations
Browse by: Latest US Patents, China's latest patents, Technical Efficacy Thesaurus, Application Domain, Technology Topic, Popular Technical Reports.
© 2025 PatSnap. All rights reserved.Legal|Privacy policy|Modern Slavery Act Transparency Statement|Sitemap|About US| Contact US: help@patsnap.com