Method for preparing ferro-titanium by carbothermic reduction-self-propagating
A titanium-iron alloy, self-propagating technology, applied in the field of metallurgy, can solve the problem of high energy consumption, achieve the effect of improving titanium grade, reducing production cost, and remarkable effect
- Summary
- Abstract
- Description
- Claims
- Application Information
AI Technical Summary
Problems solved by technology
Method used
Image
Examples
Embodiment 1
[0030] A method for producing ferro-titanium alloy by using carbothermal reduction of ilmenite as raw material in a self-propagating manner, comprising the steps of:
[0031] 1. Preparation of ilmenite by carbothermal reduction:
[0032] With ilmenite (chemical composition and weight percentage thereof are Fe 2 o 3 : 15.1~17.5%, FeO: 25.8~27.8%, TiO 2 : 43.4~45.6%, CaO: 0.8~0.9%, SiO 2 : 4.6~5.6%, MgO: 0.9~1.1%, Al 2 o 3 : 1.0~1.3%, the balance is unavoidable impurity), the oxygen combined with the elemental iron in the coal powder and the fixed carbon in the coal powder are proportioned according to the molar ratio of 1:0.8, and 1% bentonite of ilmenite mass is added, sprayed 7% of water according to the mass of the ilmenite is used for mixing and pelletizing to obtain pellets of 8-13 mm. Dry the green pellets in an oven at 105°C for 4 hours, and then place them in a nitrogen atmosphere furnace at 1100°C for reduction for 5 hours to obtain low-carbon and high-reduction ...
Embodiment 2
[0038] This embodiment is on the basis of embodiment 1, the difference is that the oxygen combined with the iron in the ilmenite and the fixed carbon in the graphite are prepared according to the molar ratio of 1:1, and the bentonite is added to the mass of the ilmenite. 3% of the ilmenite mass, spraying 8.5% of water by the mass of the ilmenite to carry out mixing and pelletizing, and then put the pellets into an argon atmosphere furnace at 1200°C for reduction for 3 hours to obtain carbothermally reduced ilmenite, and grind Pass through a 200-mesh sieve to obtain carbothermally reduced ilmenite powder for subsequent use.
[0039] Carbothermally reduced ilmenite powder, metal aluminum, potassium chlorate, titanium dioxide, calcium oxide and calcium fluoride are mixed according to a mass ratio of 100:138:62:189:32:12.
[0040] Finally, a ferro-titanium alloy is obtained, wherein the titanium content is 49.7%.
Embodiment 3
[0042] This example is based on Example 1, the difference is that the oxygen combined with the iron in the ilmenite and the fixed carbon in the pulverized coal are mixed and pelletized according to the molar ratio of 1:1.2, wherein the bentonite is added as titanium 2% of the mass of iron ore, spraying 9% of water according to the mass of ilmenite to carry out mixing and pelletizing, and then put the pellets into an argon atmosphere furnace at 1180°C for reduction for 5 hours to obtain carbothermally reduced ferrotitanium The ore is ground until it passes through a 200-mesh sieve to obtain carbothermally reduced ilmenite powder for future use.
[0043] Carbothermally reduced ilmenite powder, metal aluminum, potassium chlorate and sodium chlorate are mixed in a mass ratio of 1:1, and titanium dioxide, calcium oxide and calcium fluoride are mixed in a mass ratio of 100:136:74:190:27:13.
PUM
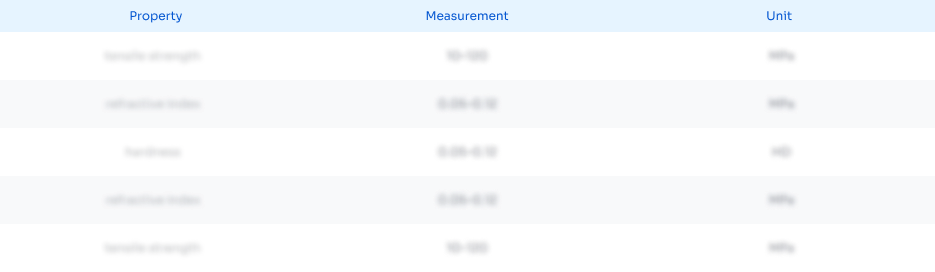
Abstract
Description
Claims
Application Information

- R&D Engineer
- R&D Manager
- IP Professional
- Industry Leading Data Capabilities
- Powerful AI technology
- Patent DNA Extraction
Browse by: Latest US Patents, China's latest patents, Technical Efficacy Thesaurus, Application Domain, Technology Topic, Popular Technical Reports.
© 2024 PatSnap. All rights reserved.Legal|Privacy policy|Modern Slavery Act Transparency Statement|Sitemap|About US| Contact US: help@patsnap.com