Grinding and leaching pretreatment process of refractory gold ore
A technology for pretreatment and gold ore, which is applied in the field of grinding and leaching pretreatment process of refractory gold ore, can solve the problems of complicated furnace gas dust collection and purification device, incomplete decomposition of sulfide, affecting gold recovery rate, etc. Sub-wrapping, significant economic and social benefits, and the effect of accelerated leaching
- Summary
- Abstract
- Description
- Claims
- Application Information
AI Technical Summary
Problems solved by technology
Method used
Image
Examples
Embodiment 1
[0053] In this embodiment, a refractory gold mine in Fujian is selected. Most of the gold is wrapped in sulfide, and its composition is 45.6g / t of gold, 15.8% of iron, and 26.4% of sulfur. The specific operation steps and process parameters adopted in this example are as follows: 100 grams of this refractory gold ore is crushed, ball milled, and the particle size is less than 0.074mm, accounting for 95%. Oxygen roasting, the roasting temperature is controlled at 1000°C, and the roasting time is 0.25 hours. The soot produced by roasting is cooled to obtain sulfur, and the grinding media zirconia balls are mixed and dry-milled at a mass ratio of 0.5:1 to the roasted slag, and the grinding time is 150 minutes. After grinding, take out the calcined slag, add acid iron solution containing 200g / L sulfuric acid and 10g / L ferric sulfate to adjust the slurry, the mass ratio of roasted slag and acid iron solution is 1:50. After mixing and sizing, place it in a reaction kettle, control ...
Embodiment 2
[0058] In this example, a refractory gold mine in Gansu is selected. The gold is wrapped in sulfide in the form of fine particles, and its composition is 52.4g / t of gold, 21.5% of iron, 23.6% of sulfur, 1.2% of copper, 7.8% of arsenic, antimony 2.3%. The specific operation steps and process parameters adopted in this example are as follows: 100 grams of this refractory gold ore is crushed, ball milled, and the particle size is less than 0.074 mm, accounting for 65%, and placed in a vacuum furnace for roasting, and the roasting temperature is controlled at 600 ° C. The calcination time is 4 hours, and the reaction residual pressure is 200Pa. Sulfur, arsenic, antimony, arsenic sulfide and antimony sulfide can be obtained by cooling the soot generated by roasting. Add silicon carbide balls with a mass ratio of 50:1 to the calcined slag, then add ferric acid solution containing 200g / L hydrochloric acid and 500g / L ferric chloride to adjust the slurry, the mass ratio of calcined sl...
Embodiment 3
[0063] In this embodiment, a refractory gold mine in Anhui is selected. Gold is wrapped in sulfide, and its main components are gold 65.9g / t, iron 19.1%, sulfur 20.2%, and carbon 1.7%. The specific operating steps and process parameters adopted in this example are as follows: get 100 grams of this refractory gold ore to be crushed, ball milled, and the particle size is less than 0.074mm, accounting for 50%, and placed in a heating furnace to feed a mixture of hydrogen and natural gas (both volume ratio 1:1) for calcination, the calcination temperature is controlled at 750°C, and the calcination time is 2 hours. The soot generated by roasting is cooled to obtain products such as hydrogen sulfide. Add ore particle grinding media with a mass ratio of 20:1 to the roasted slag, and then add acid iron solution containing 100g / L nitric acid and 200g / L ferric chloride to adjust the slurry, the mass ratio of roasted slag and acid iron solution The ratio is 1:10, and the slurry is adju...
PUM
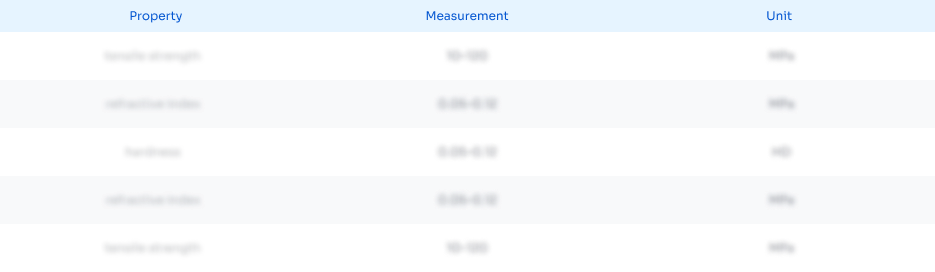
Abstract
Description
Claims
Application Information

- R&D
- Intellectual Property
- Life Sciences
- Materials
- Tech Scout
- Unparalleled Data Quality
- Higher Quality Content
- 60% Fewer Hallucinations
Browse by: Latest US Patents, China's latest patents, Technical Efficacy Thesaurus, Application Domain, Technology Topic, Popular Technical Reports.
© 2025 PatSnap. All rights reserved.Legal|Privacy policy|Modern Slavery Act Transparency Statement|Sitemap|About US| Contact US: help@patsnap.com