A method for preparing kaolin roasting activated rotary kiln
A technology of roasting activation and rotary kiln, which is applied in the field of environmental protection and comprehensive utilization of resource recycling, which can solve problems such as pollution, failure of powder materials, failure of furnace tubes and baffles, etc., to reduce environmental pollution, reduce production costs, and avoid emissions Effect
- Summary
- Abstract
- Description
- Claims
- Application Information
AI Technical Summary
Problems solved by technology
Method used
Image
Examples
Embodiment Construction
[0029] The present invention will be further described below in conjunction with the accompanying drawings and specific embodiments.
[0030] like figure 1 , figure 2 , image 3 , Figure 4 , Figure 5 , Image 6 , Figure 7 Shown, a kind of method for preparing kaolin roasting activated rotary kiln is characterized in that:
[0031] Step 1. The idler assembly 3 includes a roller set 21 and a base 22. The roasting and activating rotary cylinder 18 is inlaid with two groups of roller table assemblies 17 in the front and rear. The positioning is erected on the idler assembly 3, and the ring gear 16 is inlaid in the roasting and activating rotating cylinder. On the cylinder body 18 , the roasting activation rotary cylinder body 18 is driven to rotate around its central axis under the drive of the driving gear assembly 2 , which includes a driving gear 13 and a transmission system 12 .
[0032] Step 2, the roasting and activating rotary kiln cylinder assembly 4 includes a ...
PUM
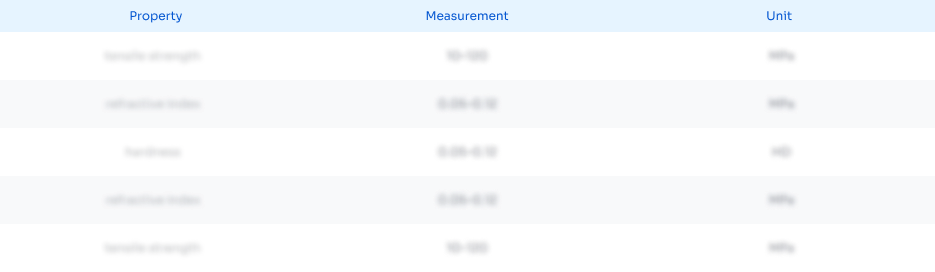
Abstract
Description
Claims
Application Information

- R&D
- Intellectual Property
- Life Sciences
- Materials
- Tech Scout
- Unparalleled Data Quality
- Higher Quality Content
- 60% Fewer Hallucinations
Browse by: Latest US Patents, China's latest patents, Technical Efficacy Thesaurus, Application Domain, Technology Topic, Popular Technical Reports.
© 2025 PatSnap. All rights reserved.Legal|Privacy policy|Modern Slavery Act Transparency Statement|Sitemap|About US| Contact US: help@patsnap.com