In Situ Synthesis of Olefin Hydration Molecular Sieve Catalysts with MFI Structure
An in-situ synthesis and olefin hydration technology, which is applied in molecular sieve catalysts, molecular sieves and base exchange compounds, chemical instruments and methods, etc., can solve the problem of in-situ synthesis of olefin hydration catalyst preparation methods report few reports, catalyst activity and stability decline, catalyst problems such as the loss of sulfonic acid groups, to achieve the effect of suitable grain size, reduced catalyst cost, high catalytic activity and selectivity
- Summary
- Abstract
- Description
- Claims
- Application Information
AI Technical Summary
Problems solved by technology
Method used
Image
Examples
Embodiment 1
[0053] Component content: in parts by weight, get 400 parts of silica sol, 500 parts of deionized water, 20 parts of tetrapropylammonium hydroxide and Al 2 o 3 The number of moles is SiO in silica sol 2 1 / 50 of the molar number of aluminum nitrate, the inorganic alkali solution is sodium hydroxide solution.
[0054] (1) Add 500 parts of deionized water to 400 parts of silica sol for dilution and stir evenly, then add 20 parts of tetrapropylammonium hydroxide dropwise to obtain the first solution;
[0055] (2) In the first solution, aluminum nitrate is added dropwise, and an aqueous solution containing 10 parts of phosphoric acid and 0.3 part of palladium chloride is added simultaneously, and the mixture is evenly stirred to obtain the second solution;
[0056] (3) adding an appropriate amount of sodium hydroxide solution to the second solution to adjust the pH value to 13.0 to obtain a third solution;
[0057] (4) Add the third solution into the autoclave, stir continuously...
Embodiment 2
[0061] Component content: in parts by weight, get 312.5 parts of ethyl orthosilicate, 200 parts of deionized water, 5 parts of tetrabutylammonium hydroxide and Al 2 o 3 The number of moles is SiO in silica sol 2 1 / 25 of the molar amount of aluminum chloride, hydrochloric acid is selected as the inorganic acid solution.
[0062] (1) Add 200 parts of deionized water to 312.5 parts of ethyl orthosilicate to dilute and stir evenly, then add 5 parts of tetrabutylammonium hydroxide dropwise to obtain the first solution;
[0063] (2) Add aluminum chloride dropwise to the first solution, and simultaneously add an aqueous solution containing 40 parts of copper nitrate and 1 part of germanium nitrate, and stir evenly to obtain the second solution;
[0064] (3) adding an appropriate amount of hydrochloric acid to the second solution to adjust the pH value to 10.0 to obtain a third solution;
[0065] (4) Add the third solution into the autoclave, stir continuously at 60°C and crystalli...
Embodiment 3
[0069] Component content: in parts by weight, get 312.5 parts of ethyl orthosilicate, 400 parts of deionized water, 15 parts of tetraethylammonium hydroxide and Al 2 o 3 The number of moles is SiO in silica sol 2 The aluminum nitrate of 1 / 80 of the molar number, and the inorganic alkali solution is potassium hydroxide solution.
[0070] (1) Add 400 parts of deionized water to 312.5 parts of ethyl orthosilicate to dilute and stir evenly, then add 15 parts of tetraethylammonium hydroxide dropwise to obtain the first solution;
[0071] (2) Add aluminum nitrate dropwise to the first solution, and simultaneously add an aqueous solution containing 5 parts of lanthanum nitrate, and stir evenly to obtain the second solution;
[0072] (3) adding an appropriate amount of sodium bicarbonate solution to the second solution to adjust the pH value to 10.0 to obtain a third solution;
[0073] (4) Add the third solution into the autoclave, stir continuously at 150° C. and crystallize for 1...
PUM
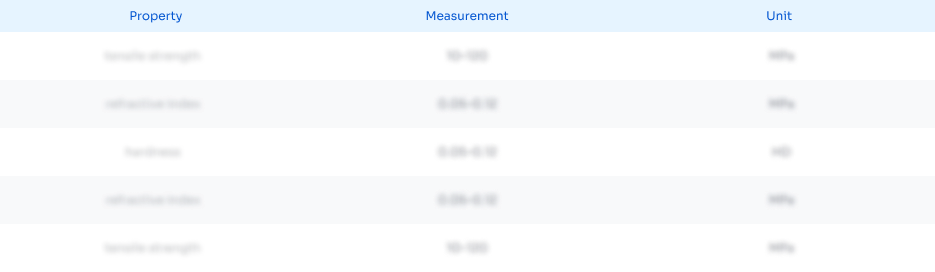
Abstract
Description
Claims
Application Information

- Generate Ideas
- Intellectual Property
- Life Sciences
- Materials
- Tech Scout
- Unparalleled Data Quality
- Higher Quality Content
- 60% Fewer Hallucinations
Browse by: Latest US Patents, China's latest patents, Technical Efficacy Thesaurus, Application Domain, Technology Topic, Popular Technical Reports.
© 2025 PatSnap. All rights reserved.Legal|Privacy policy|Modern Slavery Act Transparency Statement|Sitemap|About US| Contact US: help@patsnap.com