Method for improving stability of inverse emulsion system
An inverse emulsion and stability technology, applied in the field of emulsion polymerization, can solve the problems of many components, charge distribution, difficult operability, etc., and achieve the effects of increasing interaction, application promotion, and improving stability
- Summary
- Abstract
- Description
- Claims
- Application Information
AI Technical Summary
Problems solved by technology
Method used
Image
Examples
Embodiment 1
[0036] 300g of liquid paraffin and 45g of a mixed emulsifier system (composed of 37.8g of Span 80 and 7.2g of Tween 80) with an HLB value of 6.0 were mixed uniformly to obtain an oil phase. Mix 300g of deionized water, 57.8g of acrylamide, 42.2g of methacryloxyethyl trimethylammonium chloride, 0.5g of polyacryloxyethyl dimethylbenzyl ammonium chloride with a molecular weight of 50,000. Get the water phase. Put the oil phase in a 1L three-neck jacketed reactor, stir at 1500 rpm, and add the water phase dropwise while stirring. The time is controlled within 30 minutes. Then add 0.15g VA044 initiator and continue to stir for 15 minutes. A W / O pre-emulsion is obtained. Reduce the stirring rate to 300 revolutions per minute, keep the temperature up to 50°C, and react for 8 hours to obtain a stable W / O emulsion polymer. Put 25mL of the W / O emulsion after the reaction in a 25mL graduated glass test tube with a stopper, and place it at room temperature for one month. Observe that the...
Embodiment 2
[0040] 100g of liquid paraffin, 100g of raffinate oil, 100g of cyclohexane, 45g of a mixed emulsifier system (composed of 35.8g of Span 60 and 9.2g of OP-10) with an HLB value of 6.5 are uniformly mixed to obtain an oil phase. Combine 300g of deionized water, 50g of acrylamide, 25g of methacryloxyethyltrimethylammonium chloride, 25g of acryloxyethyltrimethylammonium chloride, 0.25g of polymethacrylamide with a molecular weight of 50,000 Oxyethyl dimethyl benzyl ammonium chloride and 0.25 g of polyacryloxyethyl dimethyl benzyl ammonium chloride with a molecular weight of 50,000 are mixed uniformly to obtain an aqueous phase. Place the oil phase in a 1L three-neck jacketed reactor, stir at 3000 rpm at high speed, add the water phase dropwise while stirring, the time is controlled within 30 minutes, and then add 5.5g potassium persulfate and 2.5g sodium nitrite. After stirring for 15 minutes, the W / O pre-emulsion is obtained. Reduce the stirring rate to 300 revolutions per minute...
Embodiment 3
[0042] 67.5g hexane, 67.5g heptane, 16.7g mixed emulsifier system (composed of 12.57g Span 85, 2.065g Tween 80 and 2.065g OP-10) with an HLB value of 5.0 were mixed uniformly to obtain an oil phase. 270g deionized water, 24g methacrylamide, 3g methacryloxyethyl dimethylbenzyl ammonium chloride, 3g acryloxyethyl dimethylbenzyl ammonium chloride, 0.015g cation degree is 90 % And a molecular weight of 200,000 methacryloxyethyl trimethylammonium chloride-octadecyl methacrylate copolymer is mixed uniformly to obtain an aqueous phase. Put the oil phase in a 1L three-neck jacketed reactor, stir at 1500 rpm at high speed, add the water phase dropwise while stirring, the time is controlled within 30 minutes, and then add 0.315g ammonium persulfate and 0.135g sodium bisulfite The composition of the redox initiator is continuously stirred for 15 minutes to obtain the W / O pre-emulsion. Reduce the stirring rate to 300 revolutions per minute, keep the temperature up to 30°C, and react for 8...
PUM
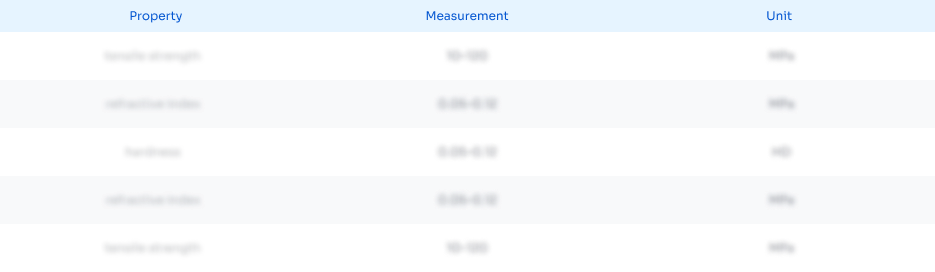
Abstract
Description
Claims
Application Information

- Generate Ideas
- Intellectual Property
- Life Sciences
- Materials
- Tech Scout
- Unparalleled Data Quality
- Higher Quality Content
- 60% Fewer Hallucinations
Browse by: Latest US Patents, China's latest patents, Technical Efficacy Thesaurus, Application Domain, Technology Topic, Popular Technical Reports.
© 2025 PatSnap. All rights reserved.Legal|Privacy policy|Modern Slavery Act Transparency Statement|Sitemap|About US| Contact US: help@patsnap.com