A kind of anti-carbon aldol condensation catalyst and its preparation method and the method of using the catalyst to prepare methyl methacrylate
A condensation catalyst, carbon deposition aldol technology, applied in chemical instruments and methods, preparation of organic compounds, catalysts for physical/chemical processes, etc. The effect of easy carbon deposition and poor stability, reduced carbon deposition rate, and reduced regeneration frequency
- Summary
- Abstract
- Description
- Claims
- Application Information
AI Technical Summary
Problems solved by technology
Method used
Examples
Embodiment 1
[0061] Weigh 3.064g of Cs 2 CO 3 , 0.041g of Pt(NO 3 ) 2 and 0.016g of Nd(NO 3 ) 3 ·6H 2 Dissolve O in 30.0ml deionized water to make an impregnation solution; weigh 50.0g SiO 2 Carrier, immersed in the above solution at room temperature, after 0.5 hours of immersion, 50 ° C vacuum rotary evaporation for 1 hour, the vacuum degree is 10 4 Pa, to prepare the catalyst precursor.
[0062] Place the catalyst precursor in a quartz tube reactor, and heat it to 200°C at a rate of 5°C / min in 95% nitrogen and 5% water vapor by volume percentage; adjust the atmosphere to 95% nitrogen and 5% carbon monoxide, the catalyst was heated to 450°C at a rate of 2°C / min; the atmosphere was adjusted to 100% nitrogen, and kept at a temperature of 450°C for 5 hours; the temperature was lowered to room temperature at a rate of 10°C / min to complete the activation of the catalyst preparation.
Embodiment 2
[0064] Weigh 10.999g of CsNO 3 , 0.844g of C 4 h 6 o 4 Pd and 0.439g PrCl 3 Dissolve in a mixed solution of 20.0ml deionized water and 10ml acetone to configure as an impregnation solution; weigh 50.0g SiO 2 The carrier was immersed in the above solution at room temperature, and after immersion for 2 hours, it was evaporated to dryness in vacuum at 60°C for 2 hours, and the vacuum degree was 10 2 Pa, to prepare the catalyst precursor.
[0065] Place the catalyst precursor in a quartz tube reactor, and heat it to 250°C at a rate of 10°C / min in 95% nitrogen and 5% water vapor by volume percentage; adjust the atmosphere to 90% nitrogen and 10% carbon monoxide, the catalyst was heated to 500°C at a rate of 5°C / min; the atmosphere was adjusted to 100% nitrogen, and kept at a temperature of 500°C for 8 hours; the temperature was lowered to room temperature at a rate of 15°C / min to complete the activation of the catalyst preparation.
Embodiment 3
[0067] Weigh 7.221g of CH 3 COOCs, 0.311g of IrCl 3 and 0.380g of Nd(NO 3 ) 3 ·6H 2 Dissolve O in 30.0ml deionized water to make an impregnation solution; weigh 50.0g SiO 2 The carrier is immersed in the above solution at room temperature. After soaking for 0.1 hour, it is evacuated to dryness in vacuum at 40°C for 0.5 hour, and the vacuum degree is 10 5 Pa, to prepare the catalyst precursor.
[0068] The catalyst precursor is placed in a quartz tube reactor, heated to 100°C at a rate of 1°C / min in 100% nitrogen by volume percentage; the atmosphere is adjusted to 99% nitrogen and 1% hydrogen, and the catalyst is Heating at a rate of 1 °C / min to 400 °C; adjusting the atmosphere to 100% nitrogen, and maintaining it at a temperature of 400 °C for 2 hours; cooling to room temperature at a rate of 5 °C / min to complete the preparation of the activated catalyst.
PUM
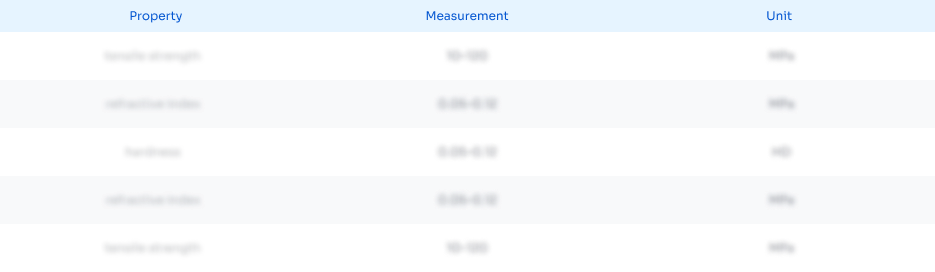
Abstract
Description
Claims
Application Information

- R&D Engineer
- R&D Manager
- IP Professional
- Industry Leading Data Capabilities
- Powerful AI technology
- Patent DNA Extraction
Browse by: Latest US Patents, China's latest patents, Technical Efficacy Thesaurus, Application Domain, Technology Topic, Popular Technical Reports.
© 2024 PatSnap. All rights reserved.Legal|Privacy policy|Modern Slavery Act Transparency Statement|Sitemap|About US| Contact US: help@patsnap.com