A kind of preparation method of environment-friendly denitrification catalyst
A technology of denitrification catalyst and pyrite slag, which is applied in the direction of catalyst activation/preparation, chemical instruments and methods, physical/chemical process catalysts, etc., can solve the problems of high production cost and hinder application, and achieve the purpose of increasing surface area and weakening mutual effect, easily amplified
- Summary
- Abstract
- Description
- Claims
- Application Information
AI Technical Summary
Problems solved by technology
Method used
Examples
Embodiment 1
[0022] 1) Pyrite slag pretreatment: crush the pyrite slag raw material, screen out 60-80 mesh pyrite slag, dissolve it in dilute nitric acid solution with a mass concentration of 2%, and filter it after stirring at room temperature for 6 hours. Filter and wash the filtered (ie undissolved) pyrite slag until neutral, then dry it at 105°C for 12 hours;
[0023] 2) Pyrite slag modification: Weigh 100g of sucrose and dissolve it in 200mL of deionized water and stir at room temperature to dissolve it completely to obtain a sucrose solution; then add 100g of the pyrite slag obtained in step 1) to the sucrose solution And continue stirring for 10 minutes to obtain mixture A; transfer mixture A to a hydrothermal reactor, and treat it at 220 ° C for 2 hours to obtain mixture B; filter the filter cake obtained by filtering mixture B and wash it with ethanol for 4 times, then After drying for 6 hours under the condition of ℃, roasting under the nitrogen atmosphere of 500 ℃ for 4 hours to...
Embodiment 2
[0026] 1) Pyrite slag pretreatment: crush the pyrite slag raw material, screen out 60-80 mesh pyrite slag, dissolve it in dilute nitric acid solution with a mass concentration of 5%, and filter it after stirring at room temperature for 4 hours. Filter and wash the filtered (ie undissolved) pyrite slag until neutral, then dry it at 105°C for 12 hours;
[0027] 2) Pyrite slag modification: Weigh 100g of sucrose and dissolve it in 200mL deionized water and stir at room temperature to dissolve it completely to obtain a sucrose solution; then add 100g of the pyrite slag obtained in step 1) to the sucrose solution And continue stirring for 15 minutes to obtain mixture A; transfer mixture A to a hydrothermal reactor, and treat it at 180 ° C for 4 hours to obtain mixture B; filter the filter cake obtained by filtering mixture B and wash it with ethanol for 4 times, After drying for 6 hours under the condition of ℃, roasting under the nitrogen atmosphere of 500 ℃ for 4 hours to obtain ...
Embodiment 3
[0030] 1) Pyrite slag pretreatment: crush the pyrite slag raw material, screen out 60-80 mesh pyrite slag, dissolve it in dilute nitric acid solution with a mass concentration of 3%, and filter it after stirring at room temperature for 6 hours. Filter and wash the filtered (ie undissolved) pyrite slag until neutral, then dry it at 105°C for 12 hours;
[0031] 2) Pyrite slag modification: Weigh 100g of sucrose and dissolve it in 200mL of deionized water and stir at room temperature to dissolve it completely to obtain a sucrose solution; then add 100g of the pyrite slag obtained in step 1) to the sucrose solution And continue stirring for 15 minutes to obtain mixture A; transfer mixture A to a hydrothermal reactor, and treat it at 200 ° C for 3 hours to obtain mixture B; filter the filter cake obtained by filtering mixture B and wash it with ethanol for 4 times, After drying for 6 hours under the condition of ℃, roasting under the nitrogen atmosphere of 500 ℃ for 4 hours to obta...
PUM
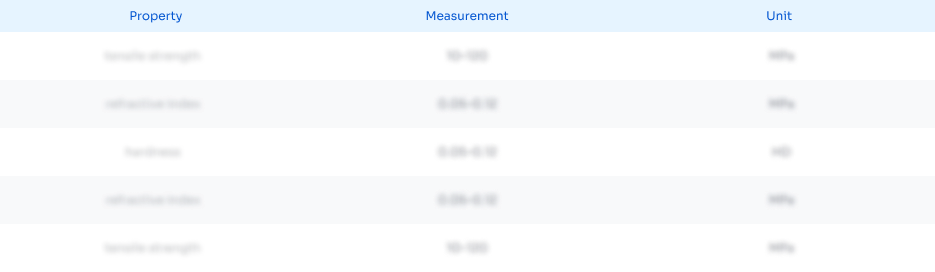
Abstract
Description
Claims
Application Information

- Generate Ideas
- Intellectual Property
- Life Sciences
- Materials
- Tech Scout
- Unparalleled Data Quality
- Higher Quality Content
- 60% Fewer Hallucinations
Browse by: Latest US Patents, China's latest patents, Technical Efficacy Thesaurus, Application Domain, Technology Topic, Popular Technical Reports.
© 2025 PatSnap. All rights reserved.Legal|Privacy policy|Modern Slavery Act Transparency Statement|Sitemap|About US| Contact US: help@patsnap.com