A kind of preparation method of denitrification catalyst
A technology of denitrification catalyst and sodium hydroxide, which is applied in the field of environmental catalysis, can solve the problems of high production costs, achieve the effects of increased added value, simple preparation process, and reduced production costs
- Summary
- Abstract
- Description
- Claims
- Application Information
AI Technical Summary
Problems solved by technology
Method used
Examples
Embodiment 1
[0020] A preparation method of SCR denitration catalyst is realized through the following steps:
[0021] (1) Pretreatment of tungsten slag: crush the raw material of tungsten slag, screen out tungsten slag of 80~100 mesh and put it in a sodium hydroxide solution with a mass concentration of 20wt%. It is 15mL / g, treated in a water bath at 60°C for 10h under the condition of ultrasonic assistance, and then filtered, and the filtered cake was washed with deionized water until neutral, and then dried at 110°C for 12h;
[0022] (2) Modification of tungsten slag: Weigh 40g of sucrose and dissolve it in 200mL deionized water, stir at room temperature for 30min to dissolve completely, then add 200g of tungsten slag obtained in step (1) to it and continue stirring for 30min to obtain Mixture A, transfer the mixture A to a hydrothermal reactor and treat it at 200°C for 6 hours, then filter it, wash it with absolute ethanol three times, dry it at 110°C for 12 hours, and then roast it un...
Embodiment 2
[0025] A preparation method of SCR denitration catalyst is realized through the following steps:
[0026] (1) Pretreatment of tungsten slag: crush tungsten slag, screen out tungsten slag of 80~100 mesh and place it in a sodium hydroxide solution with a mass concentration of 20wt%, wherein the volume-mass ratio of sodium hydroxide solution to tungsten slag is 20mL / g, treated in a water bath at 60°C for 15h under the condition of ultrasonic assistance, and then filtered, and the filter cake obtained by filtration was washed to neutral, and then dried at 110°C for 12h;
[0027] (2) Modification of tungsten slag: Weigh 20g of sucrose, dissolve it in 200mL deionized water, stir at room temperature for 25min to dissolve completely, then add 100g of tungsten slag obtained in step (1) and continue stirring for 30min. To obtain mixture A, transfer the mixture A to a hydrothermal reactor and treat it at 220°C for 4h, then filter it, wash it twice with absolute ethanol, dry it at 110°C f...
Embodiment 3
[0030]A preparation method of SCR denitration catalyst is realized through the following steps:
[0031] (1) Pretreatment of tungsten slag: crush tungsten slag, screen out tungsten slag of 80~100 mesh and place it in a sodium hydroxide solution with a mass concentration of 20wt%, wherein the volume-to-mass ratio of sodium hydroxide solution to tungsten slag is 17mL / g, treated in a water bath at 60°C for 12h under the condition of ultrasonic assistance, and then filtered, and the filter cake obtained by filtration was washed to neutral, and then dried at 110°C for 12h;
[0032] (2) Modification of tungsten slag: Weigh 20g of sucrose and dissolve it in 200mL deionized water, stir at room temperature for 20min to dissolve completely, then add 100g of tungsten slag obtained in step (1) to it and continue stirring for 30min. Obtain mixture A; transfer the mixture A to a hydrothermal reaction kettle and treat it at 210°C for 5h, then filter and wash with ethanol for 4 times, dry it ...
PUM
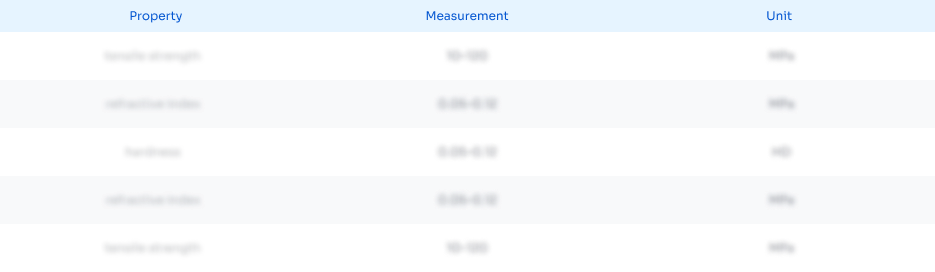
Abstract
Description
Claims
Application Information

- R&D
- Intellectual Property
- Life Sciences
- Materials
- Tech Scout
- Unparalleled Data Quality
- Higher Quality Content
- 60% Fewer Hallucinations
Browse by: Latest US Patents, China's latest patents, Technical Efficacy Thesaurus, Application Domain, Technology Topic, Popular Technical Reports.
© 2025 PatSnap. All rights reserved.Legal|Privacy policy|Modern Slavery Act Transparency Statement|Sitemap|About US| Contact US: help@patsnap.com