Component design and preparation method for zinc-aluminum alloy pipe
A kind of zinc-aluminum alloy, alloy technology
- Summary
- Abstract
- Description
- Claims
- Application Information
AI Technical Summary
Problems solved by technology
Method used
Image
Examples
Embodiment 1
[0026] A zinc-aluminum alloy pipe composition design and preparation method figure 1 Component B of the Zn-Al binary phase diagram, which contains the following components by weight: 68.6% zinc, 31% aluminum, 0.03% copper, 0.02% magnesium, 0.03% tin, 0.01% silver, 0.1% titanium, 0.01% Boron, 0.05% cerium, 0.15% praseodymium;
[0027] Its preparation process includes the following steps:
[0028] (1) According to the ratio of raw materials designed above, the raw materials are smelted in a smelting furnace, and cast in a hot work mold to obtain a multi-component zinc-aluminum alloy ingot; the preparation process of the alloy rod, the relative error of the ingredients No more than 0.3%, the casting mold material is selected from hot work die steel or graphite, and special attention is paid to degassing and impurity removal to ensure that the melt is clean, and the alloy rod is obtained by cooling;
[0029] (2) Homogenizing heat treatment of the alloy ingot obtained in step (1)...
Embodiment 2
[0034] The composition of the zinc-aluminum alloy pipe, the preparation processes (1), (2), (3) and (4) are as in Example 1;
[0035] 5) Perform precision heat treatment on the extruded zinc-aluminum alloy pipe obtained in step (4), and the process is specifically as follows: placing the obtained extruded zinc-aluminum alloy pipe in a heat treatment furnace, and stress relief annealing at 250° C. for 9 hours; obtaining High plasticity, low hardness zinc-aluminum alloy tube Zn-31Al-RE-250; sampled and prepared into mechanical specimens, and its elongation and Vickers hardness were measured.
Embodiment 3
[0037] A zinc-aluminum alloy pipe composition design and preparation method, according to the attached figure 1 The composition ratio of C in the Zn-Al binary phase diagram, which contains the following components by weight: 56.6% zinc, 43% aluminum, 0.03% copper, 0.02% magnesium, 0.03% tin, 0.01% silver, 0.1% titanium, 0.01% boron, 0.05% cerium, 0.15% praseodymium;
[0038] Its preparation process includes the following steps:
[0039] (1) According to the above ratio of raw materials, the raw materials are placed in the casting equipment for casting to obtain multi-component zinc-aluminum alloy ingots; in the preparation process of the alloy rods, the relative error of the ingredients does not exceed 0.3%, and the casting mold material is selected from hot work die steel. Or graphite, pay special attention to degassing and impurity removal to ensure that the melt is clean, and the alloy rod is obtained by cooling;
[0040] (2) Homogenizing heat treatment of the alloy ingot o...
PUM
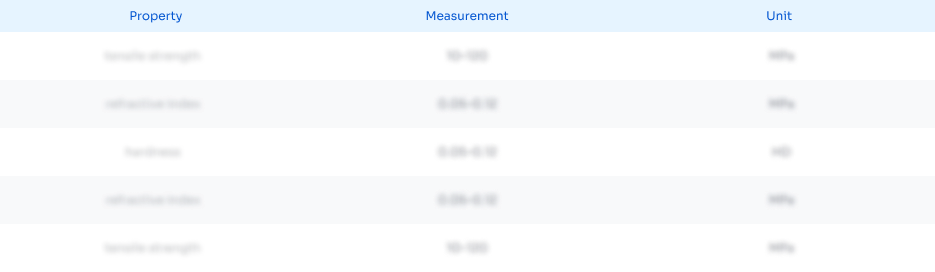
Abstract
Description
Claims
Application Information

- R&D
- Intellectual Property
- Life Sciences
- Materials
- Tech Scout
- Unparalleled Data Quality
- Higher Quality Content
- 60% Fewer Hallucinations
Browse by: Latest US Patents, China's latest patents, Technical Efficacy Thesaurus, Application Domain, Technology Topic, Popular Technical Reports.
© 2025 PatSnap. All rights reserved.Legal|Privacy policy|Modern Slavery Act Transparency Statement|Sitemap|About US| Contact US: help@patsnap.com