Preparation method of amorphous indium tin oxide thin film
A technology of indium tin oxide and thin film, which is applied in the field of preparation of amorphous indium tin oxide thin film, which can solve problems affecting processing and use, uneven film quality of indium tin oxide thin film, and difficulty in uniform dispersion of water vapor.
- Summary
- Abstract
- Description
- Claims
- Application Information
AI Technical Summary
Problems solved by technology
Method used
Image
Examples
preparation example Construction
[0019] like figure 1 The preparation method of the amorphous indium tin oxide thin film of one embodiment shown includes the following steps:
[0020] S10, providing a substrate.
[0021] The material of the substrate is glass, aluminum oxide, polyethylene terephthalate (PET) or polyimide (PI).
[0022] S20. Place the substrate obtained in S10 in the chamber of a magnetron sputtering device, under vacuum conditions, use an argon-hydrogen mixed gas with a hydrogen volume percentage of 1% to 3% as the process gas, and use indium tin oxide as the process gas For the target material, the temperature of the substrate is controlled at -50°C to 100°C, and an amorphous indium tin oxide film is deposited on the substrate by magnetron sputtering.
[0023] The vacuum degree of vacuum condition can be 1×10 -6 Pa~2×10 -4 Pa. Preferably, the degree of vacuum under vacuum conditions is 9×10 -5 Pa.
[0024] Preferably, the process gas is an argon-hydrogen mixed gas with a hydrogen cont...
Embodiment 1
[0031] Supplied with a PET substrate.
[0032] Put the PET substrate in the cavity of the magnetron sputtering equipment, and the vacuum degree is 9×10 -5 Under the vacuum condition of Pa, the process gas is argon-hydrogen mixed gas with a hydrogen volume percentage of 2.2%, and indium tin oxide with a mass content of indium oxide of 90% is used as a target material, and the temperature of the PET substrate is controlled at room temperature , Depositing amorphous indium tin oxide thin films on PET substrates by magnetron sputtering.
Embodiment 2
[0034] A glass substrate is provided.
[0035] Place the glass substrate in the cavity of the magnetron sputtering equipment at a vacuum of 1×10 -6 Under the vacuum condition of Pa, with argon-hydrogen mixed gas with a volume percentage of hydrogen of 3% as the process gas, and indium tin oxide with a mass content of indium oxide of 85% as the target material, the temperature of the glass substrate is controlled at 100 ℃, magnetron sputtering deposited amorphous indium tin oxide thin film on the glass substrate.
PUM
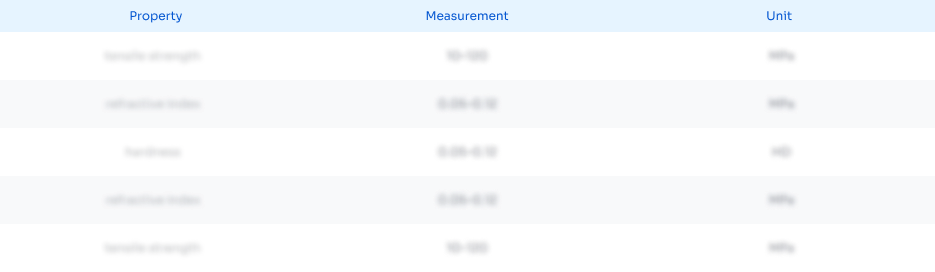
Abstract
Description
Claims
Application Information

- R&D Engineer
- R&D Manager
- IP Professional
- Industry Leading Data Capabilities
- Powerful AI technology
- Patent DNA Extraction
Browse by: Latest US Patents, China's latest patents, Technical Efficacy Thesaurus, Application Domain, Technology Topic, Popular Technical Reports.
© 2024 PatSnap. All rights reserved.Legal|Privacy policy|Modern Slavery Act Transparency Statement|Sitemap|About US| Contact US: help@patsnap.com