High-grade hot work die steel with high performance and manufacturing method of high-grade hot work die steel
A hot work die steel, high-performance technology, applied in the field of steel forging and heat treatment technology, can solve the problems of general machinability, general decarburization resistance, and reduced thermal cracking resistance, so as to improve creep resistance and quenching permeability, improve temper softening resistance, and improve thermal fatigue performance
- Summary
- Abstract
- Description
- Claims
- Application Information
AI Technical Summary
Problems solved by technology
Method used
Image
Examples
Embodiment 1
[0039] The components and weight percentages of the high-grade hot work die steels with high performance provided by the embodiments and comparative examples of the present invention are shown in Table 1 and Table 2, respectively.
[0040] Table 1 The weight percentage (%) of die steel components in each embodiment
[0041]
[0042]
[0043] Table 2 The weight percentage (%) of die steel components of each comparative example
[0044]
[0045]
Embodiment 2
[0047] The method for preparing die steel provided by the present invention is as follows:
[0048] S1: Melting: According to the composition and weight percentage of the die steel, the material is selected for smelting and poured into an electrode rod;
[0049] S2: electroslag remelting: electroslag remelting refining the cast electrode rod in a protective atmosphere;
[0050] S3: High temperature homogenization treatment: high temperature homogenization treatment at a temperature of 1200°C for 6 hours;
[0051] S4: Forging treatment: the opening forging temperature is 1110℃, the final forging temperature is 850℃, and the compression ratio is 8;
[0052] S5: Ultra-fine treatment: heat to 1030℃ and keep for 3 hours, mist cooling;
[0053] S6: Spheroidizing annealing: spheroidizing annealing temperature is 860℃, holding for 15h; 740℃ holding for 12h, cooling to below 400℃, cooling rate less than 20℃ / h, air cooling out of the furnace.
Embodiment 3
[0055] The method for preparing die steel provided by the present invention is as follows:
[0056] S1: Melting: According to the composition and weight percentage of the die steel, the material is selected for smelting and poured into an electrode rod;
[0057] S2: Electroslag remelting: Electroslag remelting refining the cast electrode rod in a protective atmosphere;
[0058] S3: High-temperature homogenization treatment: a high-temperature homogenization treatment at a temperature of 1250°C for 7 hours;
[0059] S4: Forging treatment: the opening forging temperature is 1140℃, the final forging temperature is 870℃, and the compression ratio is 12;
[0060] S5: Ultra-fine processing: heat to 1050°C for 5 hours, mist cooling;
[0061] S6: Spheroidizing annealing: spheroidizing annealing temperature is 850℃, holding for 15h; 735℃ holding for 12h, cooling to 50℃, cooling rate of 15℃ / h, air cooling out of the furnace.
PUM
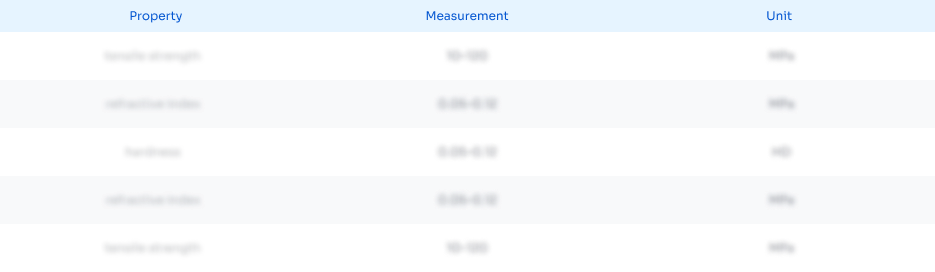
Abstract
Description
Claims
Application Information

- Generate Ideas
- Intellectual Property
- Life Sciences
- Materials
- Tech Scout
- Unparalleled Data Quality
- Higher Quality Content
- 60% Fewer Hallucinations
Browse by: Latest US Patents, China's latest patents, Technical Efficacy Thesaurus, Application Domain, Technology Topic, Popular Technical Reports.
© 2025 PatSnap. All rights reserved.Legal|Privacy policy|Modern Slavery Act Transparency Statement|Sitemap|About US| Contact US: help@patsnap.com