Method for recycling waste hydrogenation catalyst
A technology of spent hydrogenation catalysts and spent catalysts, applied in the direction of catalyst carriers, chemical instruments and methods, physical/chemical process catalysts, etc., can solve problems such as environmental hazards and waste of resources, and reduce environmental hazards, reduce pollution, reduce pollution effect
- Summary
- Abstract
- Description
- Claims
- Application Information
AI Technical Summary
Problems solved by technology
Method used
Image
Examples
Embodiment 1
[0031] Under the action of ultrasonic waves, feed chlorine gas and air into the container containing the above-mentioned treated spent catalyst powder, the volume ratio of chlorine gas to air is 5:1, and the frequency of ultrasonic waves is 100kHz to react. The solid product obtained from the reaction was transferred into a container filled with nitrogen, and heated to 700°C to separate the gas-solid phase, and condense and recover the metal from the gas phase, with a metal recovery rate of 81%. The solid residue after separation was washed with distilled water, and dried at 100° C. for 12 hours after washing. Add 3wt% scallop powder and 2wt% nitric acid to the dried material, knead it, shape it, and dry it at 120°C for 2 hours. The dried carrier was calcined at 700° C. for 3 hours in a nitrogen atmosphere to obtain an alumina-carbon composite carrier A.
Embodiment 2
[0033] Under the action of ultrasonic waves, feed chlorine gas and air into the container containing the above-mentioned treated spent catalyst powder, the volume ratio of chlorine gas to air is 4:1, and the frequency of ultrasonic waves is 80kHz to react. The solid product obtained from the reaction was transferred into a container filled with nitrogen, and heated to 750°C to separate the gas-solid phase, and condense and recover the metal from the gas phase, with a metal recovery rate of 83%. The solid residue after separation was washed with distilled water, and dried at 100° C. for 12 hours after washing. The dried material is mixed with pseudo-boehmite at a mixing ratio of 2:1, 3wt% safflower powder and 2wt% nitric acid are added, kneaded and shaped, and dried at 120°C for 2 hours. The dried carrier was calcined at 700° C. for 3 hours in a nitrogen atmosphere to obtain an alumina-carbon composite carrier B.
Embodiment 3
[0035]Under the action of ultrasonic waves, feed chlorine gas and air into the container containing the above-mentioned treated spent catalyst powder, the volume ratio of chlorine gas to air is 5:1, and the frequency of ultrasonic waves is 100kHz to react. The solid product obtained from the reaction was moved into a container filled with nitrogen, and heated to 700°C to separate the gas-solid phase, and condense and recover the metal from the gas phase, with a metal recovery rate of 86%. The solid residue after separation was washed with distilled water, and dried at 100° C. for 12 hours after washing. The dried material is mixed with pseudo-boehmite in a mixing ratio of 3:1, 3wt% safflower powder and 2wt% acetic acid are added, kneaded and shaped, and dried at 120°C for 2 hours. The dried carrier was calcined at 700° C. for 3 hours in a nitrogen atmosphere to obtain an alumina-carbon composite carrier C.
PUM
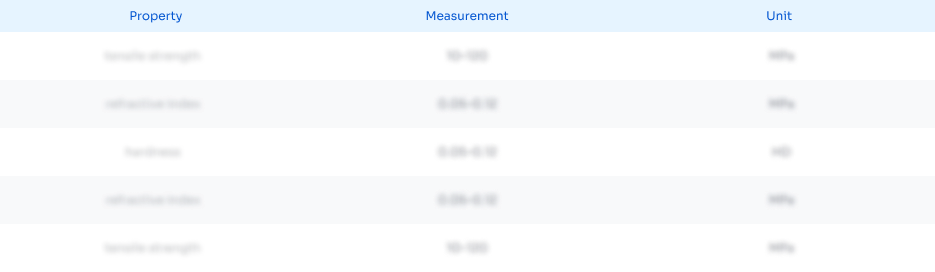
Abstract
Description
Claims
Application Information

- R&D
- Intellectual Property
- Life Sciences
- Materials
- Tech Scout
- Unparalleled Data Quality
- Higher Quality Content
- 60% Fewer Hallucinations
Browse by: Latest US Patents, China's latest patents, Technical Efficacy Thesaurus, Application Domain, Technology Topic, Popular Technical Reports.
© 2025 PatSnap. All rights reserved.Legal|Privacy policy|Modern Slavery Act Transparency Statement|Sitemap|About US| Contact US: help@patsnap.com