Roasting-ammonia leaching processing method for brown iron type laterite nickel ore
A technology of laterite nickel ore and processing method, which is applied in the fields of limonite-type laterite nickel ore roasting-ammonia leaching for nickel-cobalt extraction and comprehensive recovery of iron, can solve the problems of waste of iron resources, increased process steps, low equipment output rate and the like , to achieve the effect of full gas-solid contact, easy heat and mass transfer, and fast reaction speed
- Summary
- Abstract
- Description
- Claims
- Application Information
AI Technical Summary
Problems solved by technology
Method used
Image
Examples
Embodiment 1
[0045] The limonite-type lateritic nickel ore with a moisture content of 35% is naturally air-dried to 28%, then enters the dryer to reduce its moisture content to 6%, and then enters the mill for grinding and further drying, and the discharged ore powder The particle size is <75μm, and the moisture content of the ore powder is 1%. At this time, the contents of nickel, cobalt and iron in the ore powder are 1.06%, 0.17%, and 38.05%, respectively.
[0046] The ore powder is sent to the preheating device before the flash magnetization roasting furnace, and in the preheating device, multi-stage heat exchange is carried out with the roasting tail gas discharged from the cyclone separator; the temperature of the reducing gas entering the flash magnetization roasting furnace is higher than the roasting temperature, Provides the heat needed to maintain the firing temperature. The fully preheated ore powder enters the flash magnetization roasting furnace and undergoes suspension fluidi...
Embodiment 2
[0050] The limonite-type lateritic nickel ore was dried and ball milled in the same manner as in Example 1. The contents of nickel, cobalt and iron in the ore powder were respectively 0.98%, 0.11%, and 45.34%.
[0051] The ore powder is sent to the preheating device before the flash magnetization roasting furnace, and in the preheating device, multi-stage heat exchange is carried out with the roasting tail gas discharged from the cyclone separator; the temperature of the reducing gas entering the flash magnetization roasting furnace is higher than the roasting temperature, Provides the heat needed to maintain the firing temperature. The fully preheated ore powder enters the flash magnetization roasting furnace and undergoes suspension fluidized roasting at 600°C with the reducing gas containing 2% CO from the hot blast stove, so that the nickel and cobalt in the ore powder are reduced to metal, limonite is reduced to magnetic iron. The residence time of ore powder in the flas...
Embodiment 3
[0055] The same ore powder as in Example 1 is sent into the preheating device before the flash magnetization roasting furnace, and in the preheating device, carries out multistage heat exchange with the roasting tail gas discharged from the cyclone separator; enters the reduction of the flash magnetization roasting furnace The gas temperature is higher than the firing temperature, providing the heat needed to maintain the firing temperature. The fully preheated ore powder enters the flash magnetization roasting furnace and undergoes suspension fluidized roasting at 900°C with the reducing gas containing 7% CO from the hot blast furnace to reduce the nickel oxide and cobalt in the ore powder It is metallic nickel and cobalt, and limonite is reduced to magnetic iron. The residence time of ore powder in the flash magnetization roaster is 30s.
[0056] After the reaction is completed, the roasted ore enters the cyclone separator with the airflow for gas-solid separation, and the ...
PUM
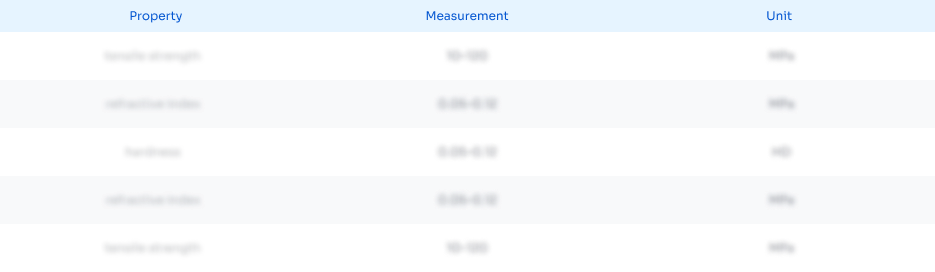
Abstract
Description
Claims
Application Information

- R&D
- Intellectual Property
- Life Sciences
- Materials
- Tech Scout
- Unparalleled Data Quality
- Higher Quality Content
- 60% Fewer Hallucinations
Browse by: Latest US Patents, China's latest patents, Technical Efficacy Thesaurus, Application Domain, Technology Topic, Popular Technical Reports.
© 2025 PatSnap. All rights reserved.Legal|Privacy policy|Modern Slavery Act Transparency Statement|Sitemap|About US| Contact US: help@patsnap.com