Cable outer layer insulation material and preparation method thereof
A technology for outer layer insulation and cable, applied in the field of cable outer layer insulation material and its preparation, can solve problems such as poor corona resistance, and achieve the effects of simple preparation method, good protection and isolation, and good service life
- Summary
- Abstract
- Description
- Claims
- Application Information
AI Technical Summary
Problems solved by technology
Method used
Examples
Embodiment 1
[0029] (1) Weigh polyethylene terephthalate 78kg, polyvinyl butyral 26kg, bisphenol hexafluoroacetone diglycidyl ether 15kg, tourmaline powder 3kg, hexamethylcyclotrisiloxane 2kg, bis- (Phenyldimethylsiloxane) methylsilanol 3kg, benzoyl peroxide butyl acetate 0.02kg and polyethylene glycol 0.8kg, add to a high-pressure homogenizer and mix evenly under 110°C and 21MPa pressure;
[0030] (2) Add 1 kg of polydeburea, 0.01 kg of copper chloride, and 0.8 kg of borosilicate to the above components, mix evenly, add to a twin-screw extruder, melt, extrude, dry, and pelletize to obtain a cable outer Layer insulation.
[0031] The temperature of each section of the twin-screw extruder is as follows: the temperature of the first zone is 195°C, the temperature of the second zone is 210°C, the temperature of the third zone is 225°C, and the temperature of the fourth zone is 230°C.
[0032] The performance test results of the prepared cable outer insulation materials are shown in Table 1. ...
Embodiment 2
[0034] (1) Weigh polyethylene terephthalate 78kg, polyvinyl butyral 26kg, bisphenol hexafluoroacetone diglycidyl ether 15kg, tourmaline powder 3kg, hexamethylcyclotrisiloxane 2kg, bis- (Phenyldimethylsiloxane) methylsilanol 3kg, benzoyl peroxide butyl acetate 0.02kg, add to a high-pressure homogenizer and mix evenly under 110°C and 21MPa pressure;
[0035] (2) Add 1 kg of polydeburea, 0.01 kg of copper chloride, and 0.8 kg of borosilicate to the above components, mix evenly, add to a twin-screw extruder, melt, extrude, dry, and pelletize to obtain a cable outer Layer insulation.
[0036] The temperature of each section of the twin-screw extruder is as follows: the temperature of the first zone is 195°C, the temperature of the second zone is 210°C, the temperature of the third zone is 225°C, and the temperature of the fourth zone is 230°C.
[0037] The performance test results of the prepared cable outer insulation materials are shown in Table 1.
Embodiment 3
[0039] (1) Weigh polyethylene terephthalate 95kg, polyvinyl butyral 33kg, bisphenol hexafluoroacetone diglycidyl ether 25kg, tourmaline powder 8kg, hexamethylcyclotrisiloxane 6kg, bis- (Phenyldimethylsiloxane)methylsilanol 5kg, benzoyl peroxide butyl acetate 0.5kg and polyethylene glycol 0.8kg, add to a high pressure homogenizer and mix evenly at 125°C and 23MPa pressure;
[0040] (2) Add 2kg of polydeburea, 0.5kg of copper chloride dihydrate, and 0.8kg of borosilicate to the above components, mix evenly, add to a twin-screw extruder, melt, extrude, dry, and pelletize to obtain Cable outer insulation material.
[0041] The temperature of each section of the twin-screw extruder is as follows: the temperature of the first zone is 200°C, the temperature of the second zone is 220°C, the temperature of the third zone is 240°C, and the temperature of the fourth zone is 240°C.
[0042] The performance test results of the prepared cable outer insulation materials are shown in Table 1...
PUM
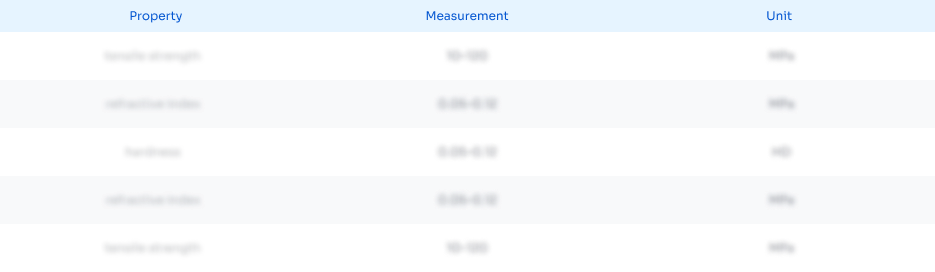
Abstract
Description
Claims
Application Information

- R&D
- Intellectual Property
- Life Sciences
- Materials
- Tech Scout
- Unparalleled Data Quality
- Higher Quality Content
- 60% Fewer Hallucinations
Browse by: Latest US Patents, China's latest patents, Technical Efficacy Thesaurus, Application Domain, Technology Topic, Popular Technical Reports.
© 2025 PatSnap. All rights reserved.Legal|Privacy policy|Modern Slavery Act Transparency Statement|Sitemap|About US| Contact US: help@patsnap.com