High-titanium-carbide steel bond hard alloy mold material
A steel-bonded hard alloy and mold material technology, which is applied in the field of mold material preparation for powder metallurgy products, can solve problems such as high brittleness, high porosity, and low strength, and achieve improved hardenability, improved grain boundary bonding force, The effect of improving the bonding strength
- Summary
- Abstract
- Description
- Claims
- Application Information
AI Technical Summary
Problems solved by technology
Method used
Image
Examples
Embodiment 1
[0020] 55.0% by weight of titanium carbide, 45% of the iron-based binder phase according to the requirements of the ingredients, the composition of the iron-based binder phase is C: 0.55%, Cr: 3.5%, Mn: 0.9%, Mo: 3.0%, Ni : 3.4%, Cu: 0.80%, the balance of Fe, where Fe consists of 80% reduced iron powder and 20% carbonyl iron powder. The bearing steel ball is used as the grinding body, the ball-to-material ratio is 4:1, the material is unloaded after wet grinding for 36 hours, vacuum-dried, then pressed into shape with a cold isostatic press, vacuum sintered at 1420°C for 1 hour, and finally kept at 1050°C for 1 hour Air cooling after 1 hour to obtain the required TiC steel-bonded hard alloy material. Its metallographic diagram see figure 1 , the properties are shown in Table 1.
Embodiment 2
[0022] 55.0% by weight of titanium carbide, 45% of the iron-based binder phase according to the requirements of the ingredients, the composition of the iron-based binder phase is C: 0.55%, Cr: 3.5%, Mn: 0.9%, Mo: 3.0%, Ni : 3.4%, Cu: 0.80%, alloy additives: 0.63%, the balance of Fe, wherein the alloy additives are composed of 0.01% B, 0.25% V and 0.27% rare earth, the rare earth is composed of La, Ce, Nd, E and Y, Fe It is composed of 80% reduced iron powder and 20% carbonyl iron powder. The bearing steel ball is used as the grinding body, the ball-to-material ratio is 4:1, the material is unloaded after wet grinding for 36 hours, vacuum-dried, then pressed into shape with a cold isostatic press, vacuum sintered at 1420°C for 1 hour, and finally kept at 1050°C for 1 hour Air cooling after 1 hour to obtain the required TiC steel-bonded hard alloy material. Its metallographic diagram see figure 2 , the properties are shown in Table 1.
Embodiment 3
[0024] 65.0% by weight of titanium carbide, 35% of the iron-based binder phase ingredients according to the requirements, the composition of the iron-based binder phase is C: 0.4%, Cr: 1.5%, Mn: 0.9%, Mo: 3.6%, Ni : 5.4%, Cu: 0.8%, alloy additives: 0.68%, the balance of Fe, wherein the alloy additives are composed of 0.01% B, 0.25% V and 0.42% rare earths, the rare earths La, Ce and Nd are composed, and Fe is composed of 80% reduced iron powder and 20% carbonyl iron powder. Bearing steel balls are used as the grinding body, the ball-to-material ratio is 4:1, the material is unloaded after wet grinding for 45 hours, vacuum-dried, then pressed into shape with a cold isostatic press, vacuum sintered at 1420°C for 1 hour, and finally kept at 1070°C for 1 hour Air cooling after 1 hour to obtain the required TiC steel-bonded hard alloy material. Its performance is shown in Table 1.
[0025] Table 1. The physical properties of the TiC steel-bonded cemented carbide prepared by the e...
PUM
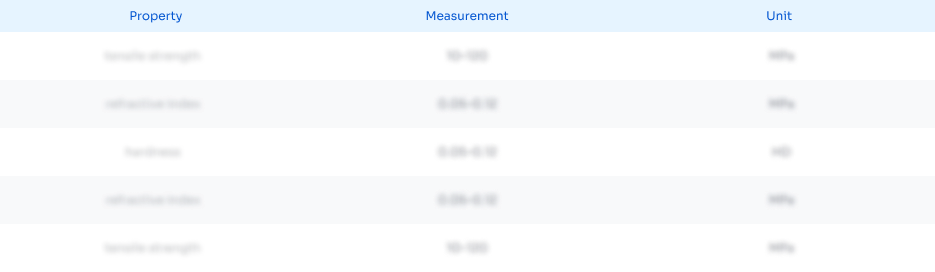
Abstract
Description
Claims
Application Information

- R&D
- Intellectual Property
- Life Sciences
- Materials
- Tech Scout
- Unparalleled Data Quality
- Higher Quality Content
- 60% Fewer Hallucinations
Browse by: Latest US Patents, China's latest patents, Technical Efficacy Thesaurus, Application Domain, Technology Topic, Popular Technical Reports.
© 2025 PatSnap. All rights reserved.Legal|Privacy policy|Modern Slavery Act Transparency Statement|Sitemap|About US| Contact US: help@patsnap.com