Chromium-free passivating pretreatment method for mirror aluminum board
A chrome-free passivation, mirror aluminum plate technology, applied in the direction of metal material coating process, etc., to achieve the effect of low cost, stable process and good adhesion
- Summary
- Abstract
- Description
- Claims
- Application Information
AI Technical Summary
Problems solved by technology
Method used
Examples
Embodiment 1
[0024] (1) Preparation of degreasing solution: Weigh 30g of potassium hydroxide, 12g of potassium silicate, 7g of potassium tetraborate, 10g of fatty alcohol alkoxy ether, and 5g of composite corrosion inhibitor, and dissolve them in 1L of tap water. Heat to about 40°C and keep stirring. After the dissolution is complete, adjust the pH value to 10-12 with acetic acid, and use it after standing still at room temperature for 24 hours;
[0025] (2) Preparation of surface adjustment solution: Weigh 30g of phosphoric acid and 3g of hydrofluoric acid, dissolve in 1L of tap water, stir to mix evenly, adjust the pH value to 1.5-3 with ammonia water, and the temperature is 22°C;
[0026] (3) Preparation of chromium-free passivation solution: weigh 4g hexafluorozirconic acid, 1g hexafluorotitanic acid, 13g magnesium nitrate, 0.5g hydrofluoric acid, 0.4g sodium sulfate, 2g 3-aminopropyltriethoxysilane , 0.08g of lanthanum chloride, dissolved in 1L of deionized water, stirred to dissolve ...
Embodiment 2
[0038] (1) Preparation of degreasing solution: Weigh 24g of potassium hydroxide, 10g of potassium silicate, 8g of potassium tetraborate, 15g of fatty alcohol alkoxy ether, and 6.5g of composite corrosion inhibitor, dissolve them in 1L of tap water, and dissolve them in 1L of tap water. It needs to be heated to about 40°C and kept stirring. After the dissolution is complete, adjust the pH value to 10-12 with acetic acid, and use it after standing still at room temperature for 24 hours;
[0039] (2) Preparation of surface adjustment solution: Weigh 24g of phosphoric acid and 1.3g of hydrofluoric acid, dissolve in 1L of tap water, stir to mix evenly, adjust the pH value to 1.5-3 with ammonia water, and the temperature is 20°C;
[0040] (3) Preparation of chromium-free passivation solution: weigh 5g hexafluorozirconic acid, 0.8g hexafluorotitanic acid, 10g magnesium nitrate, 0.6g hydrofluoric acid, 0.3g sodium sulfate, 2.5g 3-aminopropyl triethoxy silane, 0.09g lanthanum chloride, d...
Embodiment 3
[0052] (1) Preparation of degreasing solution: Weigh 15g of potassium hydroxide, 8g of potassium silicate, 11g of potassium tetraborate, 12g of fatty alcohol alkoxy ether, and 7g of composite corrosion inhibitor, and dissolve them in 1L of tap water. Heat to about 40°C and keep stirring. After the dissolution is complete, adjust the pH value to 10-12 with acetic acid, and use it after standing still at room temperature for 24 hours.
[0053] (2) Preparation of surface adjustment solution: weigh 19g of phosphoric acid and 1g of hydrofluoric acid, dissolve in 1L of tap water, stir to mix evenly, adjust the pH value to 1.5-3 with ammonia water, and the temperature is 31°C;
[0054] (3) Preparation of chromium-free passivation solution: weigh 6g hexafluorozirconic acid, 0.6g hexafluorotitanic acid, 15g magnesium nitrate, 0.7g hydrofluoric acid, 0.4g sodium sulfate, 1.7g 3-aminopropyl triethoxy Dissolve silane and 0.1g lanthanum chloride in 1L deionized water, stir to dissolve all ...
PUM
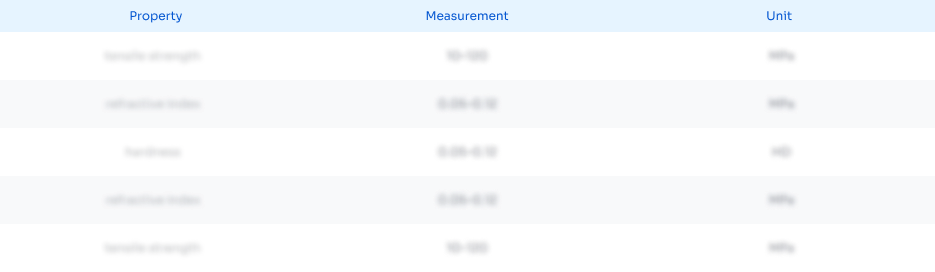
Abstract
Description
Claims
Application Information

- R&D
- Intellectual Property
- Life Sciences
- Materials
- Tech Scout
- Unparalleled Data Quality
- Higher Quality Content
- 60% Fewer Hallucinations
Browse by: Latest US Patents, China's latest patents, Technical Efficacy Thesaurus, Application Domain, Technology Topic, Popular Technical Reports.
© 2025 PatSnap. All rights reserved.Legal|Privacy policy|Modern Slavery Act Transparency Statement|Sitemap|About US| Contact US: help@patsnap.com