Sliver stannic oxide electrical contact material and preparation method thereof
A technology of electrical contact materials, silver tin oxide, applied in the direction of contacts, circuits, electric switches, etc., can solve the problems of difficulty in adapting to electrical performance and cost requirements, poor material structure uniformity, low material cost performance, etc., and meet the requirements of oxidation equipment The effect of not high, improving tissue uniformity, and low production cost
- Summary
- Abstract
- Description
- Claims
- Application Information
AI Technical Summary
Problems solved by technology
Method used
Image
Examples
Embodiment 1
[0034] A. Preparation of alloy
[0035] 0.48 kg of tin, 0.1 kg of zinc, 0.1 kg of copper, and 9.32 kg of silver were melted in a vacuum induction melting furnace and cast into alloy round ingots;
[0036] B. Broken
[0037] Using 720°C to 760°C, the alloy round ingot obtained in step A is extruded into a φ5mm alloy wire, and drawn to φ2mm, and then crushed into an alloy wire segment with a length of 10mm to 50mm, cleaned and dried;
[0038] C. Internal oxidation
[0039] The oxidation temperature in the alloy wire segment obtained in step B is 820°C, the oxidation pressure is 0.5MPa, and the oxidation time is 35h;
[0040] D. Extrusion
[0041] The oxidized material in step C is processed and then pressed and extruded into a wire or plate or strip.
[0042] The specific composition weight percentages of the silver tin oxide electrical contact material prepared in this example are as follows:
[0043]Tin oxide 6%, the total amount of additive oxides 2.45%, impurities 0.05%...
Embodiment 2
[0045] A. Preparation of alloy
[0046] 0.8 kg of tin, 0.02 kg of zinc, 0.03 kg of bismuth, 0.03 kg of copper, 0.02 kg of nickel, and 9.1 kg of silver are melted in a vacuum induction melting furnace and cast into alloy ingots;
[0047] B. Broken
[0048] Using 720°C to 760°C, the alloy round ingot obtained in step A is extruded into a φ6mm alloy wire, and drawn to φ1.3mm, then crushed into an alloy wire segment with a length of 10mm to 50mm, cleaned and dried;
[0049] C. Internal oxidation
[0050] The oxidation temperature in the alloy wire segment obtained in step B is 760°C, the oxidation pressure is 0.2MPa, and the oxidation time is 40h;
[0051] D. Extrusion
[0052] Same as Example 1.
[0053] The specific composition weight percentages of the silver tin oxide electrical contact material prepared in this example are as follows:
[0054] Tin oxide 9.9%, additive oxide total 1.51%, impurities 0.1%, silver 88.49%; Bismuth oxide content is 0.65%, copper oxide content ...
Embodiment 3
[0056] A. Preparation of alloy
[0057] 0.8 kg of tin, 0.03 kg of bismuth, 0.06 kg of copper, 0.03 kg of nickel, and 9.08 kg of silver were melted in a vacuum induction melting furnace and cast into alloy ingots;
[0058] B. Broken
[0059] Using 720°C to 760°C, the alloy round ingot obtained in step A is extruded into a φ6.3mm alloy wire, and drawn to φ1.5mm, and then crushed into an alloy wire segment with a length of 10mm to 50mm, cleaned and dried;
[0060] C. Internal oxidation
[0061] The oxidation temperature in the alloy wire segment obtained in step B is 680°C, the oxidation pressure is 0.7MPa, and the oxidation time is 30h;
[0062] D. Extrusion
[0063] Same as Example 1.
[0064] The specific composition weight percentages of the silver tin oxide electrical contact material prepared in this example are as follows:
[0065] Tin oxide is 9.9%, the total amount of additive oxides is 1.75%, impurities are 0.1%, and silver is 88.25%. Among them, the content of bis...
PUM
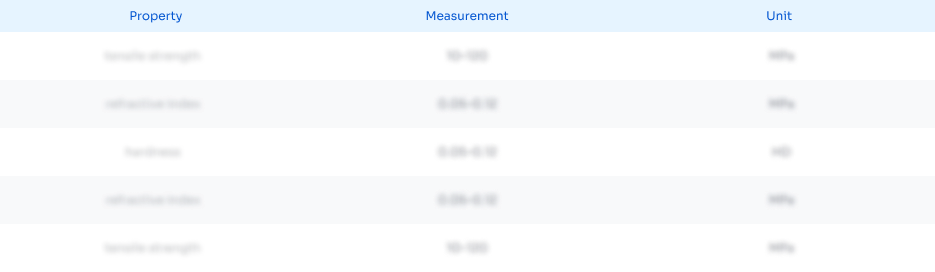
Abstract
Description
Claims
Application Information

- R&D Engineer
- R&D Manager
- IP Professional
- Industry Leading Data Capabilities
- Powerful AI technology
- Patent DNA Extraction
Browse by: Latest US Patents, China's latest patents, Technical Efficacy Thesaurus, Application Domain, Technology Topic, Popular Technical Reports.
© 2024 PatSnap. All rights reserved.Legal|Privacy policy|Modern Slavery Act Transparency Statement|Sitemap|About US| Contact US: help@patsnap.com