Industrial brush bristles and brush comprising same
A technology for brushing filaments and acid absorbers, which is applied in the direction of brushes, bristles, applications, etc., can solve the problems of not being able to use abrasive filaments and not containing abrasives, etc.
- Summary
- Abstract
- Description
- Claims
- Application Information
AI Technical Summary
Problems solved by technology
Method used
Examples
Embodiment 1
[0045] 1. Mix 4.93 kg of nylon 610 resin with 0.05 kg of polycarbodiimide (StaboxolP100) and 0.02 kg of antioxidant hindered phenol Irganox 1098.
[0046] 2. The above-mentioned mixture is passed through a twin-screw extruder, and 2.14 kilograms of emery abrasives are added from the side feeding port to carry out conventional melt spinning.
[0047] 3. The filaments coming out of the spinneret are cooled by water in the cooling tank, stretched by rollers, shaped by hot air, and finally packaged into industrial abrasive filaments.
[0048] 4. Take out a small amount of samples of the above-mentioned packaged abrasive filaments, and carry out acid treatment with pre-configured 0.1M sulfuric acid, and take out the samples after 40 days of treatment. The measured relative viscosities of the abrasive filaments before and after acid treatment were 3.27 and 3.26 respectively, and the relative viscosity change was reduced to 0.3%.
Embodiment 2
[0050] 1. Mix (4.955) kilograms of nylon 610 resin with (0.025) kilograms of sodium stearate and 0.02 kilograms of antioxidant hindered phenol Irganox 1098.
[0051] 2. The above-mentioned mixture is passed through a twin-screw extruder, and 2.14 kilograms of emery abrasives are added from the side feeding port to carry out conventional melt spinning.
[0052] 3. The filaments coming out of the spinneret are cooled by water in the cooling tank, stretched by rollers, shaped by hot air, and finally packaged into industrial abrasive filaments.
[0053] 4. Take out a small amount of samples of the above-mentioned packaged abrasive filaments, and carry out acid treatment with pre-configured 0.1M sulfuric acid, and take out the samples after 40 days of treatment. The measured relative viscosities of the abrasive filaments before and after acid treatment were 2.34 and 2.34 respectively, and the relative viscosity change was reduced to 0.
Embodiment 3
[0075] 1. Mix (4.91) kg of PBT resin, (0.05) kg of carbodiimide, (0.02) kg of hydrotalcite and (0.02) kg of antioxidant hindered phenol Irganox 1098 evenly.
[0076] 2. The above-mentioned mixture is passed through a twin-screw extruder, and 2.14 kilograms of emery abrasives are added from the side feeding port to carry out conventional melt spinning.
[0077] 3. The filaments coming out of the spinneret are cooled by water in the cooling tank, stretched by rollers, shaped by hot air, and finally packaged into industrial abrasive filaments.
[0078] 4. Take out a small amount of samples of the above-mentioned packaged abrasive filaments, and carry out acid treatment with pre-configured 0.1M sulfuric acid, and take out the samples after 40 days of treatment. The measured relative viscosities of the abrasive filaments before and after acid treatment were 2.92 and 2.90 respectively, and the relative viscosity change was reduced to 0.7%.
PUM
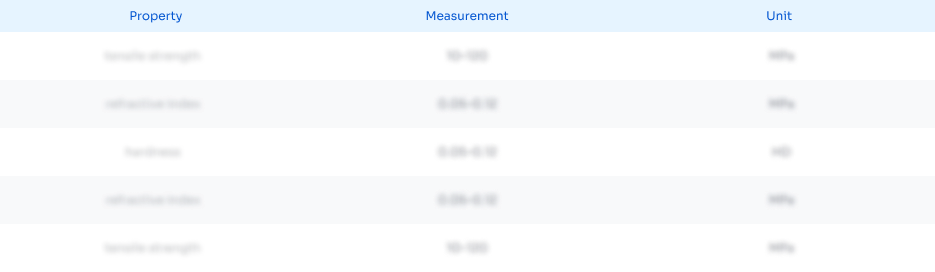
Abstract
Description
Claims
Application Information

- R&D
- Intellectual Property
- Life Sciences
- Materials
- Tech Scout
- Unparalleled Data Quality
- Higher Quality Content
- 60% Fewer Hallucinations
Browse by: Latest US Patents, China's latest patents, Technical Efficacy Thesaurus, Application Domain, Technology Topic, Popular Technical Reports.
© 2025 PatSnap. All rights reserved.Legal|Privacy policy|Modern Slavery Act Transparency Statement|Sitemap|About US| Contact US: help@patsnap.com