Technique for preparing two-component epoxy vinyl ester resin paint
A technology of epoxy vinyl ester and resin coatings, applied in the direction of epoxy resin coatings, coatings, etc., can solve problems such as increased shrinkage, difficulty in control, and potential safety hazards, so as to reduce product shrinkage and improve adhesion Strength, enhanced wear resistance effect
- Summary
- Abstract
- Description
- Claims
- Application Information
AI Technical Summary
Problems solved by technology
Method used
Image
Examples
Embodiment 1
[0025] Preparation of base material liquid: 100 parts by weight of vinyl ester resin, 15 parts of reactive diluent styrene, and 2 parts of accelerator cobalt naphthenate styrene solution, put into the batching tank in sequence, stir evenly under normal temperature and normal pressure, and set aside for use.
[0026] Preparation of titanium dioxide paste: put in ultra-fine titanium dioxide 6, toner iron oxide red 8, additives: defoamer polysiloxane solution 0.2, dispersant low molecular weight unsaturated carboxylic acid polymer 0.44, leveling agent amino resin 4. Plasticizer dibutyl phthalate 2, anti-settling agent modified urea solution 2, and the base material liquid 85, feed while stirring during the feeding process, or after feeding a raw material, wait to be basically stirred After mixing evenly, put in the second raw material. After feeding, use a high-speed disperser to disperse at low speed (1200±200 rpm) for 10-15 minutes, and then use high-speed gear (2200±200 rpm) to...
Embodiment 2
[0031] Preparation of base material liquid: 106 parts by weight of vinyl ester resin, 16 parts of reactive diluent styrene, and 2.6 parts of accelerator cobalt naphthenate styrene solution, put into the batching tank in sequence, stir evenly under normal temperature and normal pressure and set aside for use.
[0032] Preparation of titanium dioxide slurry: put in ultra-fine titanium dioxide 9, toner fast yellow 5, additives: defoamer polysiloxane solution 0.3, dispersant low molecular weight unsaturated carboxylic acid polymer 0.5, leveling agent amino resin 5.6, plasticizer dibutyl phthalate 3, anti-sedimentation agent polyethylene wax slurry 3 and the base material liquid 90, stirring, dispersing and grinding in the feeding process are the same as in Example 1;
[0033] Preparation of filler slurry: Pour Yunwu powder 10, precipitated barium sulfate 39 and the rest of the base material liquid into the batching tank, and the following dispersion and grinding are the same as in ...
Embodiment 3
[0037] Preparation of base material liquid: vinyl ester resin 120 (weight parts), reactive diluent methyl methacrylate 18, accelerator cobalt naphthenate styrene solution 5, drop into batching tank successively, after normal temperature, normal pressure stir evenly, wait for use.
[0038] Preparation of titanium dioxide slurry: 8 superfine titanium dioxide, 6 toner phthalocyanine green, additives: defoamer polysiloxane solution 0.4, dispersant low molecular weight unsaturated carboxylic acid polymer 0.7, leveling agent amino resin 8, plasticizer dibutyl phthalate 4, anti-settling agent modified urea solution 4 and the base material liquid 100, stirring, dispersing and grinding during the feeding process are the same as in Example 1;
[0039] Preparation of filler slurry: Pour Yunwu powder 6, precipitated barium sulfate 20 and the rest of the base material liquid into the batching tank, and the following dispersion and grinding are the same as in Example 1;
[0040] Pour the t...
PUM
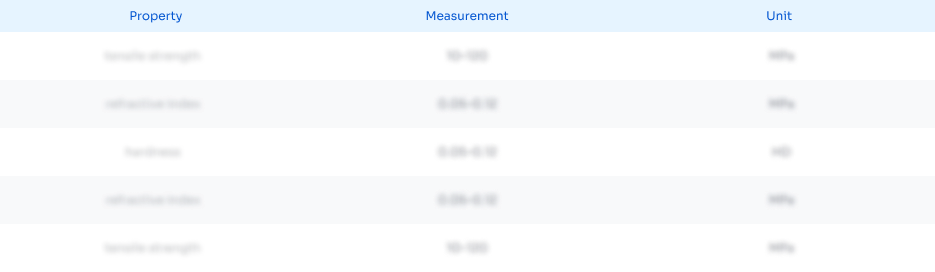
Abstract
Description
Claims
Application Information

- R&D
- Intellectual Property
- Life Sciences
- Materials
- Tech Scout
- Unparalleled Data Quality
- Higher Quality Content
- 60% Fewer Hallucinations
Browse by: Latest US Patents, China's latest patents, Technical Efficacy Thesaurus, Application Domain, Technology Topic, Popular Technical Reports.
© 2025 PatSnap. All rights reserved.Legal|Privacy policy|Modern Slavery Act Transparency Statement|Sitemap|About US| Contact US: help@patsnap.com