Method for associated producing ammonium molybdate and manganese sulfate by roasting molybdenite and pyrolusite
A technology of pyrolusite and molybdenite, applied to manganese sulfate, chemical instruments and methods, molybdenum compounds, etc., can solve the problems that have not been solved well, high energy consumption in the production process, and difficult to popularize and apply, etc., to achieve metal synthesis High recovery rate, low environmental pollution and simple equipment
- Summary
- Abstract
- Description
- Claims
- Application Information
AI Technical Summary
Problems solved by technology
Method used
Examples
Embodiment 1
[0029] Stir and mix 5 parts of molybdenite concentrate (containing Mo 47.4%) and 8 parts of pyrolusite (containing Mn 50.4%) (n MnO2 / n MoS2 =3.0), put the ore powder into the quartz tube and place it in a tube-type resistance furnace to heat up and roast. One end of the quartz tube is connected to a blower, and the air volume is controlled to be 25ml / min. The temperature is controlled at 500°C by a temperature controller, and roasted for 180min . Sulfur element analysis, Mo phase analysis, etc. were carried out on the roasted product. The results showed that the sulfur fixation rate was 94.8%, the Mo oxidation rate was 100%, and the main component of the sand was manganese molybdate (MnMoO 4 ).
[0030] The obtained manganese-containing Mo sand was leached by 100g / L sulfuric acid solution at room temperature (25°C), the solid ratio of the leaching liquid was 10, and the acid hydrolysis time was 90min, and the Mo(MoO 2 SO 4 ), Mn(MnSO 4) red solution and acid insoluble s...
Embodiment 2
[0033] Stir and mix 5 parts of molybdenite concentrate (containing Mo 47.4%) and 16 parts of pyrolusite (containing Mn 50.4%) (n MnO2 / n MoS2 =6.0), put the ore powder into the quartz tube and place it in a tubular resistance furnace for heating and roasting. One end of the quartz tube is connected to a blower, and the air volume is controlled to be 25ml / min. The temperature is controlled at 600°C by a temperature controller, and roasted for 90 minutes . Sulfur element analysis, Mo phase analysis, etc. were carried out on the roasted product, and the results showed that the sulfur fixation rate was 98.8%, the Mo oxidation rate was 100%, and the main component of the sand was manganese molybdate (MnMoO 4 ) and manganese sulfate.
[0034] The obtained manganese-containing Mo sand was leached by 300g / L sulfuric acid solution, the leaching was controlled at 65°C, the solid ratio of the leaching solution was 5, and the acid hydrolysis time was 300min, and the Mo(MoO 2 SO 4 ), ...
Embodiment 3
[0037] Stir and mix 15 parts of molybdenite concentrate (containing Mo 47.4%) and 8 parts of pyrolusite (containing Mn 50.4%) (n MnO2 / n MoS2 =2.0), put the ore powder into the quartz tube and place it in a tube-type resistance furnace to heat up and roast. One end of the quartz tube is connected to a blower, and the air volume is controlled to be 45ml / min. The temperature is controlled at 550°C by a temperature controller, and roasted for 120min . Sulfur element analysis, Mo phase analysis, etc. were carried out on the roasted product, and the results showed that the sulfur fixation rate was 91.8%, the Mo oxidation rate was 100%, and the main component of the sand was manganese molybdate (MnMoO 4 ).
[0038] The obtained manganese-containing Mo sand is leached by 30% nitric acid solution, the leaching is room temperature (25° C.), the leaching liquid-solid ratio is 15, and the leaching time is 30 min, and the red solution and acid-insoluble slag containing Mo and Mn are ob...
PUM
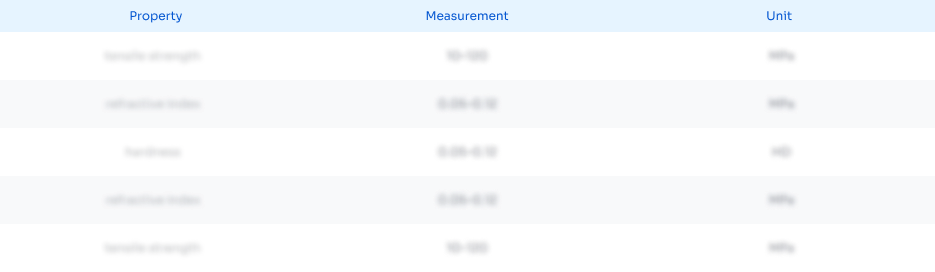
Abstract
Description
Claims
Application Information

- R&D
- Intellectual Property
- Life Sciences
- Materials
- Tech Scout
- Unparalleled Data Quality
- Higher Quality Content
- 60% Fewer Hallucinations
Browse by: Latest US Patents, China's latest patents, Technical Efficacy Thesaurus, Application Domain, Technology Topic, Popular Technical Reports.
© 2025 PatSnap. All rights reserved.Legal|Privacy policy|Modern Slavery Act Transparency Statement|Sitemap|About US| Contact US: help@patsnap.com