Pyrocatechin and hydroquinone production process
A technology for hydroquinone and catechol, applied in the field of catechol and hydroquinone production technology, can solve the problems of huge phenol separation work, high energy consumption and high cost, and achieves easy industrial automation and large scale. The effect of large-scale production, easy control of process conditions and low production cost
- Summary
- Abstract
- Description
- Claims
- Application Information
AI Technical Summary
Problems solved by technology
Method used
Image
Examples
Embodiment 1
[0044] Preparation of o-nitrophenol: Add 150 parts of Zhebai sodium hydroxide to the autoclave, add 250 parts of o-nitrochlorobenzene with a concentration of 80g / L sodium hydroxide aqueous solution, heat to 140-150°C, and the pressure is about 0.45MPa , keep warm for 2 hours, then raise the temperature to material 155-160°C, pressure about 0.54, keep warm for 3 hours. Cool down to about 120°C, press the material into a reaction kettle lined with acid-resistant ceramic tiles and equipped with titanium cooling coils and titanium stirring, neutralize with 30% hydrochloric acid until the pH is 1-2, cool down to 30°C, and filter with suction to obtain 210 parts of o-nitrophenol tidal products, the content is about 92%, and the yield is 90-95%. The parts of the raw materials are all parts by weight.
[0045] Preparation of o-aminophenol: 300 parts of o-nitrophenol, 1000 parts of 95% ethanol, 9 parts of activated nickel catalyst, sealed reaction kettle, heated to about 80 ° C, under...
Embodiment 2
[0048] With embodiment 1, difference is:
[0049]Preparation of catechol: 100 parts of o-aminophenol, 92 parts of 98% sulfuric acid, and 808 parts of water are placed in a zirconium reactor, heated to 235°C, controlled at 235-240°C for 3 hours, cooled to 50°C, filtered , the filtrate was extracted with butyl acetate, the butyl acetate was recovered, and the residue was distilled under reduced pressure at 25 mmHg to obtain 88 parts of pure catechol with a content of 99.7% and a yield of 85-90%. The parts of the raw materials are all parts by weight.
Embodiment 3
[0051] With embodiment 1, difference is:
[0052] Preparation of catechol: 108 parts of o-aminophenol, 230 parts of ammonium bisulfate, and 1700 parts of water are placed in a zirconium reactor, heated to 240°C, controlled at 240-242°C for 4 hours, and cooled to 40-50°C , filtered, the filtrate was extracted with n-butyl ether, n-butyl ether was recovered, and the residue was distilled under reduced pressure at 25 mmHg to obtain pure catechol with a content of 99.8 / 5 and a yield of 99.1%. The parts of the raw materials are all parts by weight.
PUM
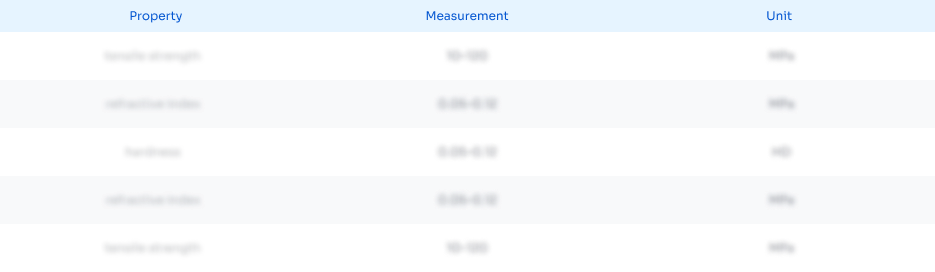
Abstract
Description
Claims
Application Information

- R&D
- Intellectual Property
- Life Sciences
- Materials
- Tech Scout
- Unparalleled Data Quality
- Higher Quality Content
- 60% Fewer Hallucinations
Browse by: Latest US Patents, China's latest patents, Technical Efficacy Thesaurus, Application Domain, Technology Topic, Popular Technical Reports.
© 2025 PatSnap. All rights reserved.Legal|Privacy policy|Modern Slavery Act Transparency Statement|Sitemap|About US| Contact US: help@patsnap.com