High nickel austenite spheroidal graphite cast-iron gas exhaust branch pipe casting technique
A technology of ductile cast iron and casting technology, which is applied in the direction of manufacturing tools, exhaust devices, casting equipment, etc., and can solve the problems of large thickness difference, high melting and pouring temperature, small exhaust pipe fittings and thin walls, etc.
- Summary
- Abstract
- Description
- Claims
- Application Information
AI Technical Summary
Problems solved by technology
Method used
Image
Examples
Embodiment 1
[0029] The casting process of the high-nickel austenitic nodular cast iron exhaust manifold shown in Figure 1 includes core making, sand mixing, molding, smelting, pouring, cleaning, heat treatment, shot blasting, blank inspection, and blank storage.
[0030] Core making, sand mixing, molding, cleaning, shot blasting, blank inspection, and blank warehousing are manufactured according to the conventional exhaust manifold manufacturing process.
[0031] Wherein the main improvement process steps are:
[0032] 1. Melting:
[0033] Melting of High Nickel Austenitic Ductile Iron
[0034] A. Furnace charge and proportion
[0035] When the content of pig iron is 50% and the content of scrap steel is 50% as the main material, the content of trace harmful elements in the charge is: Pb_≤0.002% As≤0.005% Ti≤0.045%; When the main material is 98%, the fixed carbon content of the recarburizer is ≤98%, S≥0.03%, and the particle size is between 0.15-0.3%. The scrap steel is selected at a f...
Embodiment 2
[0047] Wherein the main improvement process steps are:
[0048] 1. Melting:
[0049] Melting of High Nickel Austenitic Ductile Iron
[0050] A. Furnace charge and proportion
[0051] When the pig iron content is 75% and the steel scrap content is 25% as the main material, the content of trace harmful elements in the charge is: Pb_≤0.002% As≤0.005% Ti≤0.045%; When the main material is 95%, the fixed carbon content of the recarburizer is ≤98%, S≥0.03%, and the particle size is between 0.15-0.3%. The scrap steel is selected at a fixed point, and the composition is uniform, so there is no rust and no impurities; Ni Add in the form of electrolysis, the addition amount is 38%, Cr is added as ferrochromium containing Cr60-65%, the addition amount is 2.2%, Si is added in the form of 75% ferrosilicon, the addition amount is 5.3%;
[0052] B. Melting control
[0053] When using pig iron and scrap steel as the main material, put the pig iron and scrap into the electric furnace crucib...
PUM
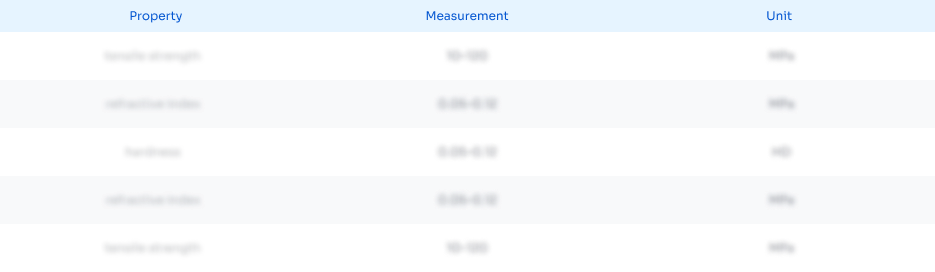
Abstract
Description
Claims
Application Information

- R&D
- Intellectual Property
- Life Sciences
- Materials
- Tech Scout
- Unparalleled Data Quality
- Higher Quality Content
- 60% Fewer Hallucinations
Browse by: Latest US Patents, China's latest patents, Technical Efficacy Thesaurus, Application Domain, Technology Topic, Popular Technical Reports.
© 2025 PatSnap. All rights reserved.Legal|Privacy policy|Modern Slavery Act Transparency Statement|Sitemap|About US| Contact US: help@patsnap.com