Solder wire material of submerged-arc welding for high grade pipeline steel
A pipeline steel, high-grade technology, applied in the direction of welding/cutting medium/material, arc welding equipment, welding medium, etc., can solve the problems of reducing toughness, difficult to meet, difficult to form passivation film, etc., to achieve good low temperature toughness, The effect of high weld strength
- Summary
- Abstract
- Description
- Claims
- Application Information
AI Technical Summary
Problems solved by technology
Method used
Image
Examples
Embodiment 1
[0025] Get 0.038% C by weight percentage, 0.040% Si, 1.800% Mn, 1.460% Ni, 0.270% Mo, 0.240% Cu, 0.025% Ti, 0.150% Ce, 95.977% Fe, use Smelting by conventional electric furnace smelting method, adding Cu, Ce, Ti-Fe, Mo-Fe during refining, controlling the tapping temperature to 1550°C, controlling the impurity S in the material to less than 0.005%, and the P to less than 0.015%, and the prepared welding wire gold phase organization see figure 1 .
[0026] The welding wire is matched with SJ101G flux to weld 15mm thick X80 grade pipeline steel. The chemical composition of the steel mainly contains 0.06% C, 1.57% Mn, 0.24% Si, 0.29% Mo, 0.14% Ni, 0.045% Cu, 0.04% Nb, 0.013% Ti, 0.0006% B, 0.01% V, 0.005% S, 0.033% P. The welding process is an asymmetrical X-shaped groove, one weld on the front and back sides, and root cleaning on the back side. The welding process parameters are welding current 580A on the first side, 650A on the second side, welding voltage 32V, and welding sp...
Embodiment 2
[0032] Get 0.030% C by weight percentage, 0.100% Si, 2.000% Mn, 1.330% Ni, 0.200% Mo, 0.300% Cu, 0.040% Ti, 0.250% Ce, 95.750% Fe, use Conventional electric furnace smelting method, adding Cu, Ce, Ti-Fe, Mo-Fe during refining, controlling the tapping temperature to 1570°C, controlling the impurity S in the material to less than 0.005%, and the P to less than 0.015%.
[0033] The welding wire is matched with SJ101G flux to weld X80 pipeline steel with a thickness of 15 mm. The chemical composition and welding process of the steel are the same as those in Example 1. The welded joints are tested according to API 5L standard, and the cold bending performance is qualified. The tensile and hardness test results are shown in Table 3, and the impact test results are shown in Table 4.
[0034]
[0035]
Embodiment 3
[0037] Get 0.053% C by weight percentage, 0.010% Si, 1.500% Mn, 1.030% Ni, 0.280% Mo, 0.200% Cu, 0.030% Ti, 0.100% Ce, 96.797% Fe, use Conventional electric furnace smelting method, adding Cu, Ce, Ti-Fe, Mo-Fe during refining, controlling the tapping temperature to 1560°C, controlling the impurity S in the material to less than 0.005%, and the P to less than 0.015%.
[0038] The welding wire is matched with SJ101G flux to weld X80 pipeline steel with a thickness of 15 mm. The chemical composition and welding process of the steel are the same as those in Example 1. The welded joints are tested according to API 5L standard, and the cold bending performance is qualified. The tensile and hardness test results are shown in Table 5, and the impact test results are shown in Table 6.
[0039]
[0040]
PUM
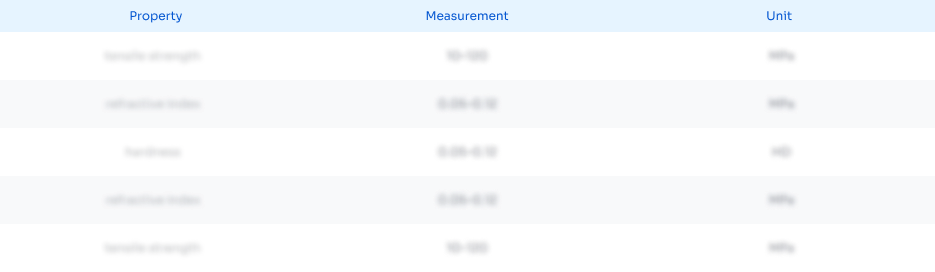
Abstract
Description
Claims
Application Information

- R&D Engineer
- R&D Manager
- IP Professional
- Industry Leading Data Capabilities
- Powerful AI technology
- Patent DNA Extraction
Browse by: Latest US Patents, China's latest patents, Technical Efficacy Thesaurus, Application Domain, Technology Topic, Popular Technical Reports.
© 2024 PatSnap. All rights reserved.Legal|Privacy policy|Modern Slavery Act Transparency Statement|Sitemap|About US| Contact US: help@patsnap.com