Low pressure combustion process of synthesizing alpha-phase silicon nitride powder
A technology of phase silicon nitride powder and low pressure combustion is applied in the field of low pressure combustion synthesis of high alpha phase silicon nitride powder, which can solve the problems of inability to meet the requirements of fine structure ceramics, high impurities such as iron in products, and increased probability of accidents. To achieve the effect of easy subsequent treatment, high content of α phase, and promotion of nitrogen permeation
- Summary
- Abstract
- Description
- Claims
- Application Information
AI Technical Summary
Problems solved by technology
Method used
Examples
Embodiment 1
[0022] The Si with an average particle size of 250 mesh was pickled with diluted HCl and dried under a protective atmosphere. Metal Si is 50.0% by weight, amorphous Si is 5.0%, Si 3 N 4 28.9%, NH 4 F is 12.3%, NH 4 Cl is 3.8%, the raw material powder is ball-milled on a rolling ball mill for 24 hours to make it fully mixed, the mixed raw material is dried at 65°C, placed in a porous graphite container, put into a combustion synthesis reaction device, and pumped After vacuuming, nitrogen gas with a pressure of 0.9 MPa is blown from the bottom of the powder, and the nitrogen gas flow rate is 8 l / min to induce the combustion of the raw material powder. The igniter is pure titanium powder or a mixture of titanium powder and carbon black, and the molar ratio is 1: 1. After the combustion reaction lasts for 15 minutes, cool to room temperature, finely grind and classify to obtain a silicon nitride powder with an α-phase silicon nitride content of 87wt% and a residual Si content o...
Embodiment 2
[0024] The silicon powder with a particle size of 350 mesh was ultrasonically treated at a power of 300 watts for 3 hours. Si is 40.5% by weight, amorphous Si is 29.5%, Si 3 N 4 21.5%, NH 4 F is 5.0%, (NH 4 ) 2 CO 3 3.5%, the raw material powder was ball milled on a rolling ball mill for 20 hours to make it fully mixed, and the mixed raw material was dried at 60°C, placed in a porous graphite container, placed in a combustion synthesis reaction device, and vacuumized Finally, nitrogen gas with a pressure of 0.7MPa is blown from the bottom of the powder, and the nitrogen gas flow rate is 4l / min, and the ignition agent is ignited to induce the combustion of the raw material powder. The ignition agent is pure titanium powder or a mixture of titanium powder and carbon black, and the molar ratio The ratio is 1:1; after the combustion reaction lasts for 10 minutes, cool to room temperature, finely grind and classify to obtain a silicon nitride powder with an α-phase silicon nit...
Embodiment 3
[0026] Silicon powder with a particle size of 450 mesh was ball milled at room temperature and at a speed of 100 r / m for 4 hours at high speed. Si is 25.5% by weight, Si(NH) 2 11.5%, Si 3 N 4 51.5%, NH 4 F is 7.6%, NH 4Cl is 3.9%, the raw material powder is ball-milled on a rolling ball mill for 15 hours to make it fully mixed, the mixed raw material is dried at 60°C, placed in a porous graphite container, put into a combustion synthesis reaction device, and pumped After vacuuming, nitrogen gas with a pressure of 0.7MPa is blown from the bottom of the powder, and the nitrogen gas flow rate is 2l / min. The igniter is ignited to induce the combustion of the raw material powder. The igniter is pure titanium powder or a mixture of titanium powder and carbon black. The ratio is 1:1; after the combustion reaction lasts for 20 minutes, cool to room temperature, finely grind and classify to obtain silicon nitride powder with α-phase silicon nitride content of 89wt% and residual Si ...
PUM
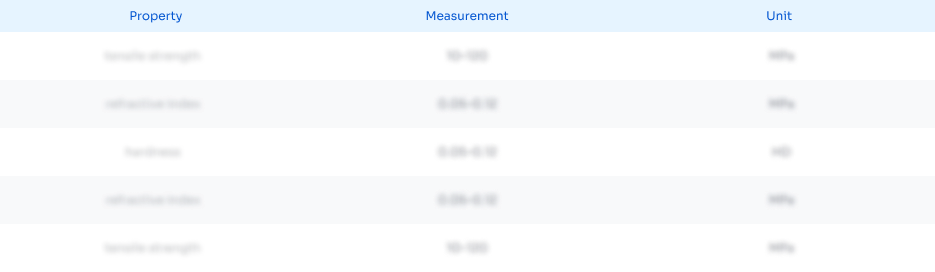
Abstract
Description
Claims
Application Information

- R&D
- Intellectual Property
- Life Sciences
- Materials
- Tech Scout
- Unparalleled Data Quality
- Higher Quality Content
- 60% Fewer Hallucinations
Browse by: Latest US Patents, China's latest patents, Technical Efficacy Thesaurus, Application Domain, Technology Topic, Popular Technical Reports.
© 2025 PatSnap. All rights reserved.Legal|Privacy policy|Modern Slavery Act Transparency Statement|Sitemap|About US| Contact US: help@patsnap.com