Preparation method and application of zinc sheet with surface coating
A surface coating and zinc flake technology, which is applied in electrode manufacturing, electrode heat treatment, active material electrodes, etc., can solve the problem of unfavorable long-term cycle performance and coulombic efficiency of zinc-ion batteries, damage the cycle performance of zinc-ion batteries, and cannot effectively resist zinc flakes Corrosion and other problems, achieve good desolvation effect, rich reserves, and improve electrochemical performance
- Summary
- Abstract
- Description
- Claims
- Application Information
AI Technical Summary
Problems solved by technology
Method used
Image
Examples
Embodiment 1
[0034] The preparation of zinc flakes with surface coating in this embodiment includes the following steps:
[0035] (1) Measure 3mL of deionized water into a 5mL glass vial with a measuring cylinder, slowly add 225mg of diatomite powder under stirring conditions, and continue stirring for 1h at a speed of 500r / mim to obtain a uniform dispersion;
[0036] (2) The dispersion liquid obtained in step 1) is evenly coated on the surface of the zinc flakes, and the thickness is controlled to be 5 μm;
[0037] (3) The zinc flakes in step (2) were quickly transferred to a vacuum drying oven at 30° C. for 30 min, and then cooled to obtain a zinc flake with a surface coating, denoted as LAP@Zn.
[0038] The dispersion liquid obtained in step 1) of this embodiment is as figure 1 As shown, the clear, homogeneous optical photographs show that the lithodiatomite is completely dispersed in deionized water.
Embodiment 2
[0040] The preparation of zinc flakes with surface coating in this embodiment includes the following steps:
[0041] (1) Measure 2 mL of deionized water into a 3 mL glass vial with a measuring cylinder (add 2 mg of methylene blue powder at the same time), slowly add 80 mg of diatomite powder under stirring conditions, and continue to stir at a speed of 300 r / mim for 0.5 h to obtain a uniform dispersion. ;
[0042] (2) The dispersion liquid obtained in step 1) is evenly coated on the surface of the zinc flakes, and the thickness is controlled to be 8 μm;
[0043] (3) The zinc flakes coated with the dispersion in step (2) were quickly transferred to a vacuum drying oven at 60° C. for 30 min, taken out and cooled to obtain zinc flakes with a surface coating, denoted as LAP@Zn.
[0044] In order to test the anti-corrosion performance of the surface coating, a small amount of methylene blue dye added in step 1) is only used for color marking. The comparative example is that the me...
Embodiment 3
[0046] The preparation of zinc flakes with surface coating in this embodiment includes the following steps:
[0047] (1) Measure 2 mL of deionized water into a 3 mL glass vial with a measuring cylinder, slowly add 100 mg of diatomite powder under stirring conditions, and continue stirring at a speed of 400 r / mim for 1.5 h to obtain a dispersion;
[0048] (2) The dispersion liquid obtained in step 1) is evenly coated on the surface of the zinc flakes, and the thickness is controlled to be 10 μm;
[0049](3) The zinc flakes coated with the dispersion in step (2) were quickly transferred to a vacuum drying oven at 120° C. for 30 min, taken out and cooled to obtain zinc flakes with a surface coating, denoted as LAP@Zn.
[0050] The zinc flakes with surface coating prepared in this example are characterized by scanning electron microscope, and the scanning electron microscope images of the cross section and surface are as follows: image 3 It can be seen that the obtained surface ...
PUM
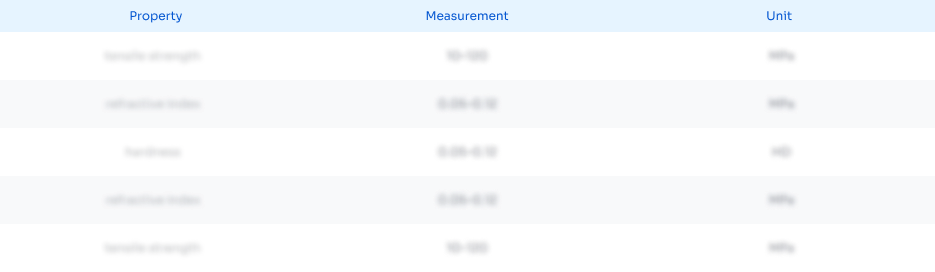
Abstract
Description
Claims
Application Information

- R&D
- Intellectual Property
- Life Sciences
- Materials
- Tech Scout
- Unparalleled Data Quality
- Higher Quality Content
- 60% Fewer Hallucinations
Browse by: Latest US Patents, China's latest patents, Technical Efficacy Thesaurus, Application Domain, Technology Topic, Popular Technical Reports.
© 2025 PatSnap. All rights reserved.Legal|Privacy policy|Modern Slavery Act Transparency Statement|Sitemap|About US| Contact US: help@patsnap.com