Method for directly smelting ferrovanadium nitride or ferrovanadium with high-temperature vanadium slag without chemical process
A ferrovanadium nitride and chemical process technology, applied in the field of vanadium metallurgy, can solve the problems of insufficient utilization of physical heat, low ferrovanadium grade, and inability to produce ferrovanadium nitride, and achieves no consumption of chemical raw materials, reduced investment, vanadium The effect of small loss
- Summary
- Abstract
- Description
- Claims
- Application Information
AI Technical Summary
Problems solved by technology
Method used
Examples
Embodiment 1
[0028] (1) Vanadium-containing molten iron contains 0.45% V; 0.23% Si; 0.25% Mn; 0.18% Ti; 0.06% Cr. At the end of vanadium extraction in a 150-ton converter, carbon powder is sprayed to the bottom of the furnace. The amount of carbon powder added is 25% of the total iron mass in the vanadium slag, and the iron oxide in the slag is reduced to obtain V in the high-temperature vanadium slag. 2 o 5 content 22.52%, TFe content 9.67%, SiO 2 、TiO 2 Content 17.95%, MnO content 4.26%, the rest is Al2O 3 , MgO, CaO, etc.
[0029] (2) Add blue charcoal particles from the top of the vanadium extracting converter after the semi-steel has been removed for reduction, and the amount of blue charcoal particles added is 25% of the mass of vanadium slag.
[0030] (3) Pour the high-temperature vanadium slag into a 20-ton electric arc furnace through an insulating slag tank. By controlling the reduction temperature to 1600°C, the vanadium in the vanadium slag is deeply reduced, and at the sam...
Embodiment 2
[0034] (1) Vanadium-containing molten iron contains 0.42% V; 0.24% Si; 0.26% Mn; 0.18% Ti; 0.06% Cr. At the end of vanadium extraction in the 150-ton converter, natural gas is sprayed to the bottom of the furnace, and the natural gas flow rate is 300m 3 / min, reduce the iron oxide in the slag, and get V in the high-temperature vanadium slag 2 o 5 content 21.76%, TFe content 9.58%, SiO 2 、TiO 2 Content 17.93%, MnO content 5.42%, the rest is Al 2 o 3 , MgO, CaO, etc.
[0035] (2) Add blue charcoal particles from the top of the vanadium extracting converter to reduce after the semi-steel is produced, and the amount of blue charcoal particles added is 20% of the mass of vanadium slag.
[0036] (3) Pour the high-temperature vanadium slag into a 20-ton intermediate frequency furnace through the heat preservation slag tank. By controlling the reduction temperature to 1550°C, the vanadium in the vanadium slag is deeply reduced. The intermediate frequency furnace is covered and s...
Embodiment 3
[0040] (1) Vanadium-containing molten iron contains 0.45% V; 0.20% Si; 0.25% Mn; 0.18% Ti; 0.06% Cr. At the end of vanadium extraction in a 150-ton converter, coke oven gas is sprayed to the bottom of the furnace. The coke oven gas feed rate is 50m3 / min, and the iron oxide in the slag is reduced to obtain V in the high-temperature vanadium slag. 2 o 5 content 21.55%, TFe content 11.74%, SiO 2 , TiO2 content 19.32%, MnO content 4.46%, the rest is Al 2 o 3 , MgO, CaO, etc.
[0041] (2) Add coke particles from the top of the vanadium extracting converter for reduction after the semi-steel has been removed, and the amount of coke particles added is 15% of the mass of the vanadium slag total iron.
[0042](3) Pour the high-temperature vanadium slag into a 20-ton intermediate-frequency induction furnace. By controlling the reduction temperature to 1550°C, the vanadium in the vanadium slag is deeply reduced. The intermediate-frequency induction furnace is covered and sealed, and ...
PUM
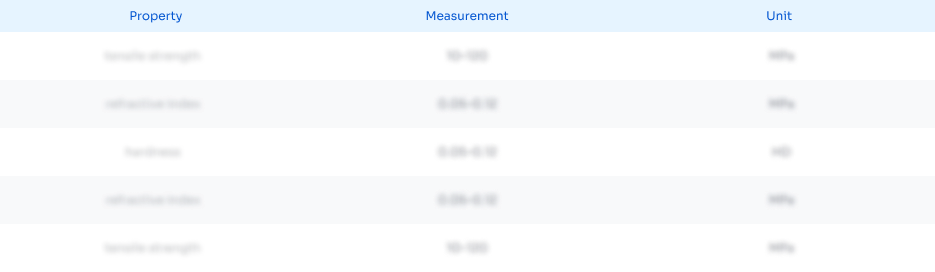
Abstract
Description
Claims
Application Information

- R&D
- Intellectual Property
- Life Sciences
- Materials
- Tech Scout
- Unparalleled Data Quality
- Higher Quality Content
- 60% Fewer Hallucinations
Browse by: Latest US Patents, China's latest patents, Technical Efficacy Thesaurus, Application Domain, Technology Topic, Popular Technical Reports.
© 2025 PatSnap. All rights reserved.Legal|Privacy policy|Modern Slavery Act Transparency Statement|Sitemap|About US| Contact US: help@patsnap.com