Preparation method of concrete forming curing agent
A curing agent and concrete technology, which is applied in the field of concrete to achieve the effects of increasing strength, reducing production costs, and protecting water resources
- Summary
- Abstract
- Description
- Claims
- Application Information
AI Technical Summary
Problems solved by technology
Method used
Image
Examples
Embodiment 1
[0045] see Figure 1-9 Shown, present embodiment is a kind of preparation method of concrete forming curing agent, comprises the following steps:
[0046] Step 1: put sepiolite, silicon dioxide and titanium dioxide into the feeding hopper 104 of the grinding device according to the weight ratio of 6:4:5, connect the driving pulley 108 and the driven pulley 109 by installing a belt, and pass The chain is installed to connect the driving sprocket 113 and the driven sprocket 114;
[0047] Step 2: start the grinding motor 110, the grinding motor 110 drives the linkage shaft 107 to rotate through the driving pulley 108 and the driven pulley 109, and drives several rolling grinding wheels 117 on the inner wall of the grinding chamber 102 through the mounting plate 116 scroll;
[0048] Step 3: Start the conveying motor 111, and the conveying motor 111 drives the threaded conveying rod 118 to rotate through the driving sprocket 113 and the driven sprocket 114, and the rotating threa...
Embodiment 2
[0055] see Figure 1-9 As shown, the grinding device in this embodiment includes a grinding mechanism 100, a separation mechanism 200, a delivery pipeline 300, and a coarse material collection box 400. One side of the grinding mechanism 100 is connected to one end of the delivery pipeline 300, so The other end of the delivery pipeline 300 is connected to the top side of the separation mechanism 200, the bottom of the delivery pipeline 300 is equipped with a coarse material collection box 400, and a coarse material discharge port is provided on one side of the coarse material collection box 400 , the first box door is installed on the coarse material discharge port;
[0056] Wherein, the grinding mechanism 100 includes a mounting frame 101, a grinding bin 102, a discharge pipe 103, a hopper 104, a delivery box 105, a bearing seat 106, a linkage shaft 107, a driving pulley 108, a driven pulley 109, Grinding motor 110, conveying motor 111, fixed mount 112, driving sprocket 113, ...
PUM
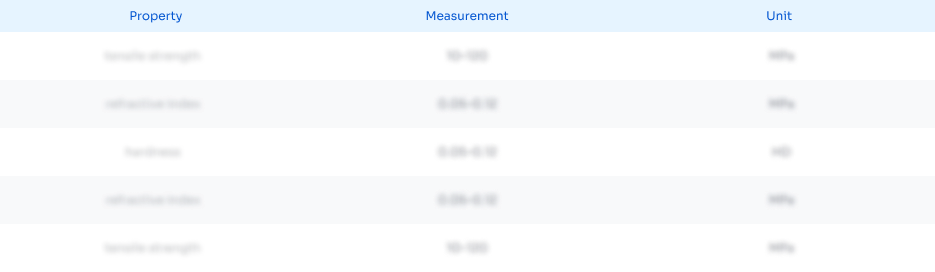
Abstract
Description
Claims
Application Information

- R&D Engineer
- R&D Manager
- IP Professional
- Industry Leading Data Capabilities
- Powerful AI technology
- Patent DNA Extraction
Browse by: Latest US Patents, China's latest patents, Technical Efficacy Thesaurus, Application Domain, Technology Topic, Popular Technical Reports.
© 2024 PatSnap. All rights reserved.Legal|Privacy policy|Modern Slavery Act Transparency Statement|Sitemap|About US| Contact US: help@patsnap.com