Fast-fired tea dust matt reaction glaze and preparation method thereof
A light reaction and tea powder technology, which is applied in the field of fast-fired tea powder non-light reaction glaze and its preparation, can solve the problems of increasing process difficulty, difficulty in controlling the amount of introduction, and large crystals, so as to reduce labor costs and facilitate large-scale production , Improve the effect of density
- Summary
- Abstract
- Description
- Claims
- Application Information
AI Technical Summary
Problems solved by technology
Method used
Image
Examples
Embodiment 1
[0028] Preparation of modified nano-zinc oxide:
[0029] Step S1, dissolving yttrium oxide in nitric acid to prepare 0.7mol / L yttrium nitrate solution, dissolving zinc nitrate hexahydrate in deionized water to prepare 0.75mol / L zinc nitrate solution, and mixing the two solutions in a volume ratio of 1:1 , to obtain a salt solution;
[0030] Step S2, add 2mol / L ammonia water to the salt solution while stirring, continue to stir for 2h and then stand for 3h, separate the precipitate and wash it with deionized water and absolute ethanol for 3 times, and then place it in an oven to dry to obtain a precursor body, wherein the mass ratio of salt solution and ammonia water is 1:10;
[0031] In step S3, the precursor is placed in a muffle furnace for primary calcination, and then ethanol is added for ball milling, followed by secondary calcination to obtain modified nano-zinc oxide. The temperature was 1100°C, and the temperature was kept for 4h.
Embodiment 2
[0033] Preparation of modified nano-zinc oxide:
[0034] Step S1, dissolving yttrium oxide in nitric acid to prepare 0.71mol / L yttrium nitrate solution, dissolving zinc nitrate hexahydrate in deionized water to prepare 0.76mol / L zinc nitrate solution, and mixing the two solutions in a volume ratio of 1:1 , to obtain a salt solution;
[0035] Step S2, add 2mol / L ammonia water to the salt solution while stirring, continue to stir for 2h and then stand for 3h, separate the precipitate and wash it with deionized water and absolute ethanol for 3 times, and then place it in an oven to dry to obtain a precursor body, wherein the mass ratio of salt solution and ammonia water is 1:10;
[0036] In step S3, the precursor is placed in a muffle furnace for primary calcination, and then ethanol is added for ball milling, followed by secondary calcination to obtain modified nano-zinc oxide. The temperature was 1100°C, and the temperature was kept for 4h.
Embodiment 3
[0038] Preparation of modified nano-zinc oxide:
[0039] Step S1, dissolving yttrium oxide in nitric acid to prepare 0.73mol / L yttrium nitrate solution, dissolving zinc nitrate hexahydrate in deionized water to prepare 0.78mol / L zinc nitrate solution, and mixing the two solutions in a volume ratio of 1:1 , to obtain a salt solution;
[0040] Step S2, add 2mol / L ammonia water to the salt solution while stirring, continue to stir for 2h and then stand for 4h, separate the precipitate and wash it with deionized water and absolute ethanol for 4 times, and then place it in an oven to dry to obtain a precursor body, wherein the mass ratio of salt solution and ammonia water is 1:10;
[0041] In step S3, the precursor is placed in a muffle furnace for primary calcination, and then ethanol is added for ball milling, followed by secondary calcination to obtain modified nano-zinc oxide. The temperature was 1100°C, and the temperature was kept for 4h.
PUM
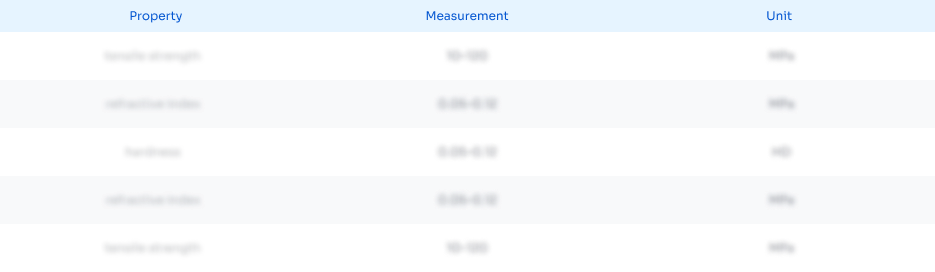
Abstract
Description
Claims
Application Information

- R&D Engineer
- R&D Manager
- IP Professional
- Industry Leading Data Capabilities
- Powerful AI technology
- Patent DNA Extraction
Browse by: Latest US Patents, China's latest patents, Technical Efficacy Thesaurus, Application Domain, Technology Topic, Popular Technical Reports.
© 2024 PatSnap. All rights reserved.Legal|Privacy policy|Modern Slavery Act Transparency Statement|Sitemap|About US| Contact US: help@patsnap.com