Method for modifying epoxy resin through phosphorus/nitrogen/silicon synergistic flame retardance
An epoxy resin and synergistic flame-retardant technology, applied in the field of flame-retardant materials, can solve the problems of reducing the mechanical properties and poor compatibility of flame-retardant products, and achieve the effects of improving heat release rate, easy control, and improving dispersion
- Summary
- Abstract
- Description
- Claims
- Application Information
AI Technical Summary
Problems solved by technology
Method used
Image
Examples
Embodiment 1
[0031] Melamine polyphosphate MPP and siloxane halogen-free cyclotriphosphazene APESP were baked in a vacuum oven at 80°C for 6 hours; 4.38g of APESP was dissolved in 150ml of absolute ethanol. Mix; add 39.42g of dried MPP to the APESP solution, place the three-neck flask in an oil bath, and stir for 30 minutes while raising the temperature to 80°C; then use a rotary evaporator to evaporate the ethanol at 60°C, The obtained remaining solid was put into a vacuum oven and baked at 80°C for 8 hours. When the mass became constant, it was taken out and ground into powder, and stored in a desiccator to obtain an APESP modified melamine polyphosphate flame retardant; Weigh 292g of dried bisphenol A epoxy resin prepolymer E-44 epoxy resin in a three-necked flask, and place it in an oil bath at 140°C for preheating; 20g of modified melamine polyphosphate flame retardant Add the curing agent into the three-necked flask, stir at 140°C for 30 minutes, and stir thoroughly with a mechanical...
Embodiment 2
[0033] Melamine polyphosphate MPP and siloxane halogen-free cyclotriphosphazene APESP were baked in a vacuum oven at 80°C for 6 hours; 4.38g of APESP was dissolved in 150ml of absolute ethanol, and placed in a three-necked flask at room temperature Mix well; add 17.52g of dried MPP to the APESP solution, place the three-necked flask in an oil bath, and stir for 30 minutes while raising the temperature to 80°C; then use a rotary evaporator to evaporate the ethanol to dryness at 60°C , put the remaining solid obtained in a vacuum oven at 80°C and bake for 8 hours. When the mass becomes constant, take it out and grind it into powder, and store it in a desiccator to obtain APESP modified melamine polyphosphate flame retardant ; Weigh 292g of dried bisphenol A epoxy resin prepolymer E-44 epoxy resin in a three-necked flask and place it in an oil bath at 140°C for preheating; 20g of modified melamine polyphosphate resistance Put the fuel into the three-necked flask, stir at 140°C fo...
Embodiment 3
[0035] Melamine polyphosphate MPP and siloxane halogen-free cyclotriphosphazene APESP were baked in a vacuum oven at 80°C for 6 hours; 4.38g of APESP was dissolved in 150ml of absolute ethanol, and placed in a three-necked flask at room temperature Mix well; add 17.52g of dried MPP to the APESP solution, place the three-necked flask in an oil bath, and stir for 30 minutes while raising the temperature to 60°C; then use a rotary evaporator to evaporate the ethanol to dryness at 60°C , put the remaining solid obtained in a vacuum oven at 80°C and bake for 8 hours. When the mass becomes constant, take it out and grind it into powder, and store it in a desiccator to obtain APESP modified melamine polyphosphate flame retardant ; Weigh 292g of dried bisphenol A epoxy resin prepolymer E-44 epoxy resin in a three-necked flask and place it in an oil bath at 100°C for preheating; 20g of modified melamine polyphosphate resistance Put the fuel into the three-necked flask, stir for 30 minu...
PUM
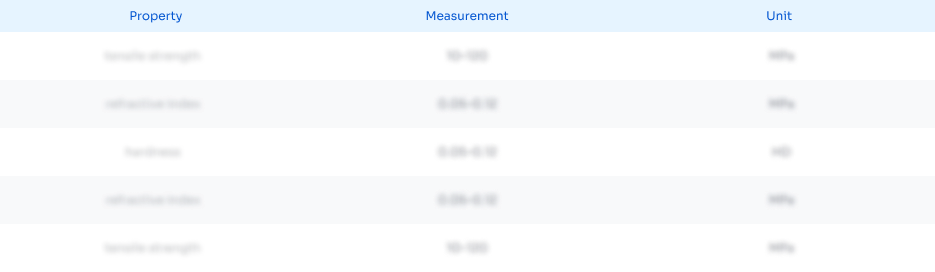
Abstract
Description
Claims
Application Information

- Generate Ideas
- Intellectual Property
- Life Sciences
- Materials
- Tech Scout
- Unparalleled Data Quality
- Higher Quality Content
- 60% Fewer Hallucinations
Browse by: Latest US Patents, China's latest patents, Technical Efficacy Thesaurus, Application Domain, Technology Topic, Popular Technical Reports.
© 2025 PatSnap. All rights reserved.Legal|Privacy policy|Modern Slavery Act Transparency Statement|Sitemap|About US| Contact US: help@patsnap.com