A preparation method of flame-retardant and toughened PBT for motor inserts
A technology of inserting and toughening, which is applied in the field of preparation of flame-retardant and toughened PBT, can solve the problems of PBT toughness influence, damage to PBT molecular connection performance, etc., and achieve the effect of improving adaptability, capacity and flame retardancy
- Summary
- Abstract
- Description
- Claims
- Application Information
AI Technical Summary
Problems solved by technology
Method used
Examples
Embodiment 1
[0035] S1. After mixing silicon carbide powder and graphene powder at a weight ratio of 53:1, pour it into a mold, and perform dry pressing at 180MPa to obtain a silicon carbide green body.
[0036] S2. Put the above-mentioned silicon carbide green body into a vacuum pressureless sintering furnace, raise the temperature to 2100°C, then cool down to 1950°C for sintering and heat preservation for 9 hours, take it out and grind it after cooling to obtain silicon carbide-graphene powder.
[0037] S3. SiC-graphene powder, sintering aid B 4 C. Flame retardant zinc borate, defoamer n-octanol and dispersant cetylpyridinium bromide are mixed according to the weight ratio of 30:0.6:4:0.4:1.3 to form a mixture; the mixture is 0.4kg according to the mass volume ratio / L was added to deionized water, and ball milled for 18 hours to form a slurry.
[0038] S4. Send the slurry into a pressurized sintering furnace, adjust the sintering pressure to 40MPa, and sinter at 360°C for 2 hours at hi...
Embodiment 2
[0042] S1. After mixing silicon carbide powder and graphene powder at a weight ratio of 53:1, pour it into a mold, and perform dry pressing at 180MPa to obtain a silicon carbide green body.
[0043] S2. Put the above-mentioned silicon carbide green body into a vacuum pressureless sintering furnace, raise the temperature to 2100°C, then cool down to 1900°C for sintering and heat preservation for 8 hours, take it out and grind it after cooling to obtain silicon carbide-graphene powder.
[0044] S3. SiC-graphene powder, sintering aid B 4 C. Flame retardant zinc borate, defoamer n-octanol and dispersant cetylpyridinium bromide are mixed according to the weight ratio of 30:0.5:3:0.3:1.3 to form a mixture; the mixture is 0.3kg according to the mass volume ratio / L was added to deionized water, and ball milled for 15 hours to form a slurry.
[0045] S4. Send the slurry into a pressurized sintering furnace, adjust the sintering pressure to 40MPa, and sinter at a high temperature of 3...
Embodiment 3
[0049] S1. After mixing silicon carbide powder and graphene powder at a weight ratio of 53:1, pour it into a mold, and perform dry pressing at 180MPa to obtain a silicon carbide green body.
[0050] S2. Put the above-mentioned silicon carbide green body into a vacuum pressureless sintering furnace, raise the temperature to 2100°C, then cool down to 2000°C for sintering and heat preservation for 10 hours, take it out and grind it after cooling to obtain silicon carbide-graphene powder.
[0051] S3. SiC-graphene powder, sintering aid B 4 C. Flame retardant zinc borate, defoamer n-octanol and dispersant cetylpyridinium bromide are mixed according to the weight ratio of 30:0.7:5:0.5:1.3 to form a mixture; the mixture is 0.5kg according to the mass volume ratio / L was added to deionized water, and ball milled for 20 hours to form a slurry.
[0052] S4. Send the slurry into a pressurized sintering furnace, adjust the sintering pressure to 40MPa, and sinter at a high temperature of ...
PUM
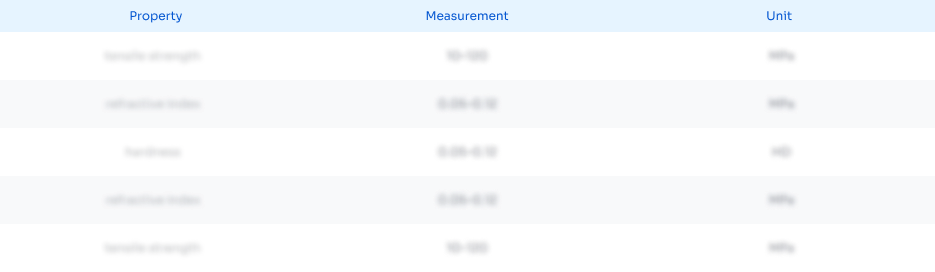
Abstract
Description
Claims
Application Information

- R&D Engineer
- R&D Manager
- IP Professional
- Industry Leading Data Capabilities
- Powerful AI technology
- Patent DNA Extraction
Browse by: Latest US Patents, China's latest patents, Technical Efficacy Thesaurus, Application Domain, Technology Topic, Popular Technical Reports.
© 2024 PatSnap. All rights reserved.Legal|Privacy policy|Modern Slavery Act Transparency Statement|Sitemap|About US| Contact US: help@patsnap.com