A copper-based powder metallurgy pantograph sliding plate material for monorail vehicles and its preparation method
A pantograph sliding plate and powder metallurgy technology, which is applied in the field of copper-based powder metallurgy pantograph sliding plate materials for monorail vehicles, can solve the problems of large wear amount, unfavorable environmental protection and high friction coefficient
- Summary
- Abstract
- Description
- Claims
- Application Information
AI Technical Summary
Problems solved by technology
Method used
Image
Examples
Embodiment 1
[0029] Put the powders of niobium oxide, zirconia, silicon carbide, and graphene into a three-dimensional mixer, mix them at 50°C for 3 hours, bake the powders at a pressure of 10Pa for 10 hours, cool down to 30°C, mix the powders with their mass 5 ~8 times of absolute ethanol was mixed, soaked for 50min under 500W ultrasonic vibration, and then the resulting mixture was dried at 3Pa, 20°C for 3h, and polyvinyl butyral, barium bicarbonate, Mix the starch evenly, press it with a granulator at 6 MPa to form granules with a particle size of 2mm, put the granules at 1200°C and sinter the air with an oxygen volume content of 23% for 15 hours, cool down the sintered ceramic granules, and use a ball mill to process them into Ultrafine powder, to obtain the conductive ceramics;
[0030] Reduct the copper powder in an ammonia decomposition atmosphere for 2.5 hours and then cool it to room temperature; dry the graphite, tin powder, nickel powder, chromium powder, molybdenum disulfide, a...
Embodiment 2
[0032]Put the powders of niobium oxide, zirconia, silicon carbide and graphene into a three-dimensional mixer, mix at 70°C for 5 hours, bake the powder at a pressure of 15Pa for 20 hours, cool down to 35°C, mix the powder with its mass of 8 times of absolute ethanol, soaked for 70min under 700W ultrasonic vibration, then dried the resulting mixture at 8Pa, 25°C for 5h, added polyvinyl butyral, barium bicarbonate, and starch to the dried product and mixed Evenly, use a granulator to press under 6MPa to form particles with a particle size of 3mm, place the particles at 1300°C and sinter in air with an oxygen volume content of 25% for 20 hours, cool down the sintered ceramic particles, and use a ball mill to process them into ultra-fine particles. powder, to obtain the conductive ceramics;
[0033] Reduct the copper powder in an ammonia decomposition atmosphere for 2.5 hours and then cool it to room temperature; dry the graphite, tin powder, nickel powder, chromium powder, molybd...
Embodiment 3
[0035] Put the powders of niobium oxide, zirconia, silicon carbide and graphene into a three-dimensional mixer, mix at 67°C for 4 hours, bake the powder at a pressure of 13Pa for 17 hours, cool down to 33°C, mix the powder with its mass of 8 times of absolute ethanol, soaked for 70min under 500W ultrasonic vibration, then dried the resulting mixture at 3Pa, 25°C for 3h, and added polyvinyl butyral, barium bicarbonate, and starch to the dried product to mix Evenly, use a granulator to press under 6MPa to form particles with a particle size of 3mm, place the particles at 1200°C, and sinter in air with an oxygen volume content of 25% for 15 hours, cool down the sintered ceramic particles, and use a ball mill to process them into ultrafine particles. powder, to obtain the conductive ceramics;
[0036] Copper powder is reduced in an ammonia decomposition atmosphere for 3 hours and then cooled to room temperature; graphite, tin powder, nickel powder, chromium powder, molybdenum disu...
PUM
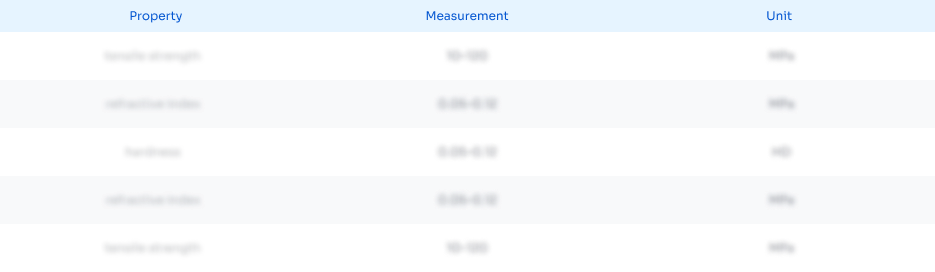
Abstract
Description
Claims
Application Information

- R&D
- Intellectual Property
- Life Sciences
- Materials
- Tech Scout
- Unparalleled Data Quality
- Higher Quality Content
- 60% Fewer Hallucinations
Browse by: Latest US Patents, China's latest patents, Technical Efficacy Thesaurus, Application Domain, Technology Topic, Popular Technical Reports.
© 2025 PatSnap. All rights reserved.Legal|Privacy policy|Modern Slavery Act Transparency Statement|Sitemap|About US| Contact US: help@patsnap.com