Device and method for preparing 2,6-dimethylnaphthalene
A technology of dimethylnaphthalene and temperature control device, which is applied in chemical instruments and methods, catalyst activation/preparation, isomerization hydrocarbon production, etc., can solve the problems of high cost, low purity, and low yield of 2,6-DMN problem, to achieve the effect of easy industrial application, simple operation and simple device structure
- Summary
- Abstract
- Description
- Claims
- Application Information
AI Technical Summary
Problems solved by technology
Method used
Image
Examples
preparation example Construction
[0033] The second aspect of the present invention proposes a method for preparing 2,6-dimethylnaphthalene, which uses the above-mentioned device for preparing 2,6-dimethylnaphthalene. Preferably, the preparation method comprises the following steps:
[0034] In the isomerization reaction step, the mixed solution of medium washing oil and organic solvent is introduced into the isomerization reactor 200 through the feed pipe 100 to carry out the isomerization reaction, and the temperature of the isomerization reactor 200 is controlled to be 320° C. to 400° C. ℃;
[0035]In the rectification step, the mixed liquid after the isomerization reaction is introduced into the rectification tower for rectification treatment, the temperature of the rectification tank 340 of the rectification tower is controlled to be 280°C-290°C, and the temperature control of the first temperature control device 310 The temperature is 270°C-280°C, the temperature control temperature of the second temper...
Embodiment 1
[0051] The weight ratio is sodium aluminate: sodium silicate: zinc hydroxide: palladium chloride = 1:1.5:2:0.5 Weigh 500g of sodium aluminate, sodium silicate, zinc hydroxide and palladium chloride in total, dissolve in 5L The mass concentration is 10% cetyltrimethylammonium bromide aqueous solution, stirring at 60°C for 45 minutes, adding sulfuric acid to adjust the pH to 8-10, and standing for 30 minutes to prepare the catalyst precursor.
[0052] The catalyst precursor was placed in an autoclave and reacted at 150°C for 5.0 hours. The obtained solid was washed and dried with deionized water, and then calcined at 600°C for 8.0 hours. The calcined solid was crushed into powder and uniformly viscous On the catalyst carrier 210 pottery sheet coated with silica sol, after standing at room temperature for a period of time, calcining at 350° C. for 1.5 h to prepare the catalyst-loaded pottery sheet. The pottery pieces are placed in the isomerization reactor 200 in a single and dou...
Embodiment 2
[0057] Sodium aluminate by weight: sodium silicate: zinc hydroxide: palladium chloride = 1:1.2:1.6:0.4 Weigh 500g of sodium aluminate, sodium silicate, zinc hydroxide, and palladium chloride in total, dissolve in 5L The mass concentration is 10% cetyltrimethylammonium bromide aqueous solution, stirred at 60° C. for 30 minutes, added sulfuric acid to adjust the pH to 8-10, and stood still for 20 minutes to prepare the catalyst precursor.
[0058] The catalyst precursor was placed in an autoclave and reacted at 120°C for 2.0 hours. The obtained solid was washed and dried with deionized water, and then calcined at 500°C for 5.0 hours. The calcined solid was crushed into powder and uniformly viscous On the catalyst carrier 210 pottery sheet coated with silica sol, after standing at room temperature for a period of time, calcining at 300° C. for 1.0 h to prepare the catalyst-loaded pottery sheet. The pottery pieces are placed in the isomerization reactor 200 in a single and double ...
PUM
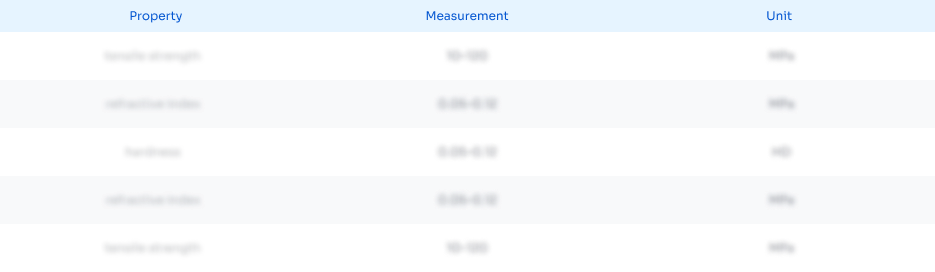
Abstract
Description
Claims
Application Information

- R&D Engineer
- R&D Manager
- IP Professional
- Industry Leading Data Capabilities
- Powerful AI technology
- Patent DNA Extraction
Browse by: Latest US Patents, China's latest patents, Technical Efficacy Thesaurus, Application Domain, Technology Topic, Popular Technical Reports.
© 2024 PatSnap. All rights reserved.Legal|Privacy policy|Modern Slavery Act Transparency Statement|Sitemap|About US| Contact US: help@patsnap.com