Preparation method of high-toughness UV varnish
A glossy varnish, high toughness technology, applied in coatings and other directions, can solve the problems of poor mechanical properties, insufficient impact resistance and toughness of coating materials, achieve uniform sol network structure, improve mechanical properties and bonding strength, Reducing the effect of insufficient uniformity of stress
- Summary
- Abstract
- Description
- Claims
- Application Information
AI Technical Summary
Problems solved by technology
Method used
Image
Examples
Embodiment 1
[0033]In terms of parts by weight, weigh 45 parts of tetramethoxysilane, 15 parts of methanol and 6 parts of deionized water respectively and place them in a Erlenmeyer flask, stir and mix and add 1 mol / L hydrochloric acid of 1 / 100 of the quality of deionized water, After insulated reaction at 78°C for 20 hours, the mixed liquid was collected and treated by rotary evaporation. After the rotary evaporation reached 1 / 5 of the original volume, the rotary evaporated liquid was collected and the mass ratio was 1:2:10. Add a fraction of 8% ammonia water to N, N-dimethylformamide, stir and mix and place at room temperature for gelation treatment, collect the gel liquid and place it in a drying kettle, dry it under pressure at 8MPa and collect dry air condensation Glue particles;
[0034] According to the mass ratio of 1:5, the dry airgel particles and nano-titanium dioxide particles were stirred and mixed and ground through a 2000 mesh sieve, the sieved particles were collected and p...
Embodiment 2
[0038] In terms of parts by weight, weigh 47 parts of tetramethoxysilane, 17 parts of methanol and 7 parts of deionized water respectively and place them in a Erlenmeyer flask, stir and mix and add 1 mol / L hydrochloric acid of 1 / 100 of the quality of deionized water, After insulated reaction at 84°C for 22 hours, the mixed liquid was collected and treated by rotary evaporation. After the rotary evaporation reached 1 / 5 of the original volume, the rotary evaporated liquid was collected and the mass ratio was 1:2:10. Add a fraction of 8% ammonia water to N,N-dimethylformamide, stir and mix and place at room temperature for gelation treatment, collect the gel liquid and place it in a drying kettle, dry it under pressure at 9MPa and collect dry air condensation Glue particles;
[0039] According to the mass ratio of 1:5, the dry airgel particles and nano-titanium dioxide particles were stirred and mixed and ground through a 2000 mesh sieve, the sieved particles were collected and p...
Embodiment 3
[0043] In terms of parts by weight, weigh 50 parts of tetramethoxysilane, 20 parts of methanol and 8 parts of deionized water respectively and place them in a Erlenmeyer flask, stir and mix and add 1 mol / L hydrochloric acid of 1 / 100 of the quality of deionized water, After insulated reaction at 95°C for 24 hours, the mixed liquid was collected and treated by rotary evaporation. After the rotary evaporation reached 1 / 5 of the original volume, the rotary evaporated liquid was collected and the mass ratio was 1:2:10. Add a fraction of 8% ammonia water to N,N-dimethylformamide, stir and mix and place at room temperature for gelation treatment, collect the gel liquid and place it in a drying kettle, dry it under pressure at 10MPa and collect dry air condensation Glue particles;
[0044] According to the mass ratio of 1:5, the dry airgel particles and nano-titanium dioxide particles were stirred and mixed and ground through a 2000 mesh sieve, the sieved particles were collected and ...
PUM
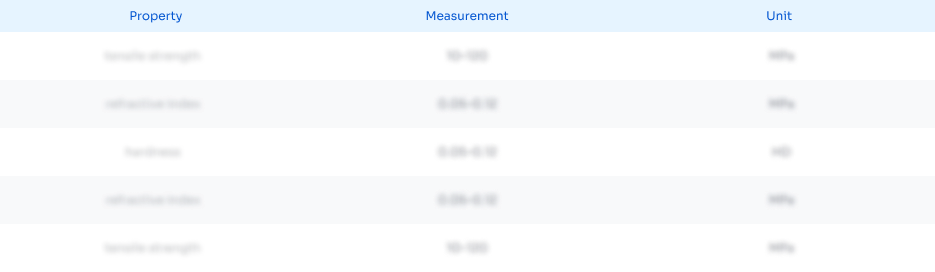
Abstract
Description
Claims
Application Information

- Generate Ideas
- Intellectual Property
- Life Sciences
- Materials
- Tech Scout
- Unparalleled Data Quality
- Higher Quality Content
- 60% Fewer Hallucinations
Browse by: Latest US Patents, China's latest patents, Technical Efficacy Thesaurus, Application Domain, Technology Topic, Popular Technical Reports.
© 2025 PatSnap. All rights reserved.Legal|Privacy policy|Modern Slavery Act Transparency Statement|Sitemap|About US| Contact US: help@patsnap.com