Preparation method of multilayer reticular zirconium oxide fiber reinforced resin-based material
A technology of zirconia fiber and reinforced resin base is applied in the field of preparation of multi-layer reticulated zirconia fiber reinforced resin base material, which can solve the problems such as failure to realize large-scale popularization and application, low production cost, uncontrollable material structure and the like , to achieve the effect of improving the chemical stability of the interface, large friction coefficient, wide industrial production and application in machinery
- Summary
- Abstract
- Description
- Claims
- Application Information
AI Technical Summary
Problems solved by technology
Method used
Image
Examples
Embodiment 1
[0033] Step 1: Mix 30% silica ceramic powder and 70% PAA mixed solution according to mass percentage to obtain ceramic powder A with certain viscosity;
[0034] Wherein, the PAA mixed solution is composed of 40% PAA, 50% deionized water, 5% sodium carbonate and 5% sodium tripolyphosphate;
[0035] Step 2: Soak the zirconia fiber cloth in an acetone mixed solution and ultrasonically treat it for 10 minutes, then dry it at 50°C to obtain a surface-modified fiber solid B;
[0036] Among them, the zirconia fiber cloth adopts a mixture of zirconia and silica in a diversified network system.
[0037] The acetone mixed solution is composed of 40% acetone, 50% deionized water and 10% sodium carbonate.
[0038] Step 3: Take fiber solid B and carry out solid phase reaction at 200°C for 20 minutes, wash with ethanol solution for 3 to 6 times, and then dry at 50°C to obtain net-like solid C;
[0039] Step 4: Take the reticular solid C and put it in the hydroxylation solution, add the ph...
Embodiment 2
[0050] Step 1: Mix 50% calcium oxide ceramic powder with 50% PAA mixed solution according to mass percentage to obtain ceramic powder A with certain viscosity;
[0051] Wherein, the PAA mixed solution is composed of 60% PAA, 30% deionized water, 5% sodium carbonate and 5% sodium tripolyphosphate;
[0052] Step 2: Soak the zirconia fiber cloth in an acetone mixed solution and ultrasonically treat it for 30 minutes, then dry it at 30°C to obtain a surface-modified fiber solid B;
[0053] Among them, the zirconia fiber cloth adopts a mixture of zirconia and potassium oxide in a diversified network system;
[0054] The acetone mixed solution is composed of 60% acetone, 30% deionized water and 10% sodium carbonate.
[0055] Step 3: Take the fiber solid B and carry out a solid phase reaction at 400°C for 15 minutes, wash it with ethanol solution for 3 to 6 times, and then dry it at 70°C to obtain a net-like solid C;
[0056] Step 4: Take the reticular solid C and put it in the hyd...
Embodiment 3
[0062] Step 1: Mix 40% iron oxide and calcium titanate mixed ceramic powder with 60% PAA mixed solution according to mass percentage to obtain ceramic powder A with certain viscosity;
[0063] Wherein, the PAA mixed solution is composed of 45% PAA, 40% deionized water, 7% sodium carbonate and 8% sodium tripolyphosphate;
[0064] Step 2: Soak the zirconia fiber cloth in an acetone mixed solution and ultrasonically treat it for 15 minutes, then dry it at 560°C to obtain a surface-modified fiber solid B;
[0065] Among them, the zirconia fiber cloth adopts a mixture of zirconia and potassium oxide in a diversified network system;
[0066] The acetone mixed solution is composed of 35% acetone, 35% deionized water and 30% sodium carbonate.
[0067] Step 3: take fiber solid B and carry out solid-phase reaction at 300°C for 18 minutes, wash with ethanol solution for 3 to 6 times, and then dry at 60°C to obtain net-like solid C;
[0068] Step 4: Take the reticular solid C and put it...
PUM
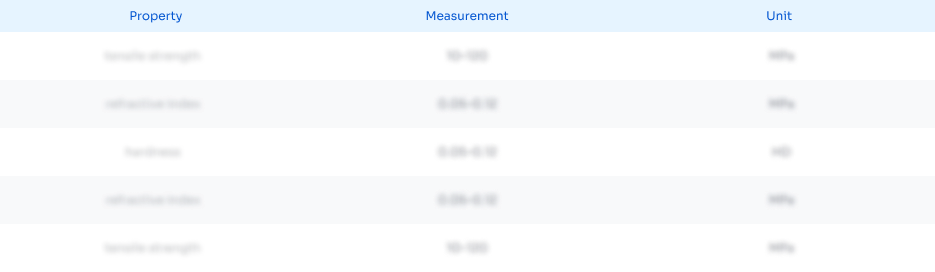
Abstract
Description
Claims
Application Information

- R&D
- Intellectual Property
- Life Sciences
- Materials
- Tech Scout
- Unparalleled Data Quality
- Higher Quality Content
- 60% Fewer Hallucinations
Browse by: Latest US Patents, China's latest patents, Technical Efficacy Thesaurus, Application Domain, Technology Topic, Popular Technical Reports.
© 2025 PatSnap. All rights reserved.Legal|Privacy policy|Modern Slavery Act Transparency Statement|Sitemap|About US| Contact US: help@patsnap.com