Cement kiln tail flue gas catalytic oxidation desulfurization method
A catalytic oxidation desulfurization, cement kiln technology, applied in chemical instruments and methods, separation methods, physical/chemical process catalysts, etc. The effect of high efficiency, good catalytic reaction effect and high system reliability
- Summary
- Abstract
- Description
- Claims
- Application Information
AI Technical Summary
Problems solved by technology
Method used
Examples
Embodiment 1
[0034] A 2500t / d cement plant in South China, due to the problem of the rock layer of the mine, temporarily no high-quality limestone is used, and the sulfur content of the high-sulfur ore used is 0.4% to 0.9%. 2 Emissions 1278mg / Nm 3 , causing the environmental protection to stop, after adopting the solution of this embodiment, the SO 2 Emission is stable at 20-90mg / m 3 , less than 100mg / m 3 , to meet the national special regional emission standards.
[0035] This embodiment scheme specifically includes the following steps:
[0036] (1) Select soluble Fe 2 (SO4) 3 ·9H 2 O crystal, MnSO 4 ·H 2 O crystals, prepared with water in a mass ratio of 5:3:600, containing Fe + and Mn + catalyst solution;
[0037] (2) The injection point is set on the flue gas pipeline 5m behind the high temperature fan of the cement kiln system, and 6 nozzles are evenly distributed in the ring. According to the injection volume of 0.5-1 ton / h, it is injected into the flue gas of the kiln ta...
Embodiment 2
[0042] A 4000t / d cement plant in East China, due to the exhaustion of high-quality limestone ore, had to use high-sulfur ore with a sulfur content of 0.7% to 1.3%. 2 Emission 1000~1600mg / Nm 3 , sometimes up to 2500mg / Nm 3 , the flue gas emission is 310,000 Nm 3 / h, after adopting the solution of this embodiment, the SO 2 Emission is stable at 10-50mg / m 3 , less than 100mg / m 3 , to meet the national special regional emission standards.
[0043] This embodiment scheme specifically includes the following steps:
[0044] (1) Select soluble CuSO 4 ·5H 2 O crystals, Zn(NO 3 ) 2 ·6H 2 O crystals, 20wt% ammonia solution, and water in a mass ratio of 2:1:200:800 to prepare a catalyst solution containing metal ions;
[0045] (2) Set the injection point on the C1 of the cement kiln system, and distribute 8 nozzles in a circular shape; the catalyst solution is 0.3-1.5 tons / h by a water pump with a pressure of 0.8MPa and an atomizing wide-angle nozzle with a model of 1 / 4. The s...
Embodiment 3
[0050] A 5000t / d cement plant in Southwest China, using high-sulfur ore with a sulfur content of 0.9% to 1.5%, in which SO in the flue gas during the stop of the vertical mill 2 Emission 1100~1900mg / Nm 3 , after adopting the scheme of this embodiment, where SO 2 Emission is stable at 50-150mg / m 3 , less than 200mg / m 3 , to meet the national emission standards.
[0051] The difference between the scheme of this example and Example 1 is: 1) Select iron ore and industrial area waste liquid (containing nitric acid and sulfuric acid) solution to directly react ferric nitrate and ferric sulfate solution, and filter, press ferric nitrate (or ferric sulfate) ), aluminum chloride, copper sulfate, polysorbate-80, and water in a mass ratio of 2:1:1:50:950 to prepare a catalyst solution containing metal ions; 2) In the preheater of the cement kiln system There are 2 injection points at the outlet humidification tower and the flue gas pipeline 8m behind the high temperature fan, respec...
PUM
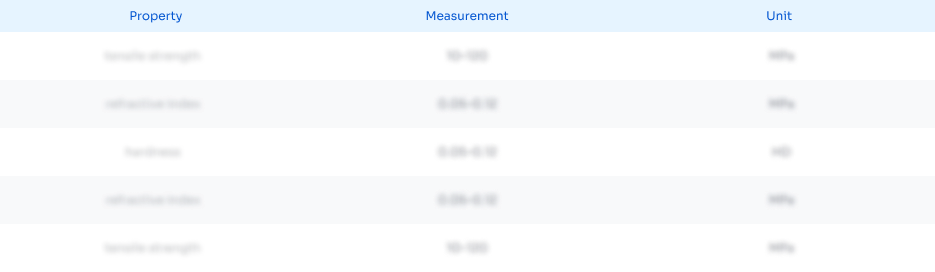
Abstract
Description
Claims
Application Information

- R&D Engineer
- R&D Manager
- IP Professional
- Industry Leading Data Capabilities
- Powerful AI technology
- Patent DNA Extraction
Browse by: Latest US Patents, China's latest patents, Technical Efficacy Thesaurus, Application Domain, Technology Topic, Popular Technical Reports.
© 2024 PatSnap. All rights reserved.Legal|Privacy policy|Modern Slavery Act Transparency Statement|Sitemap|About US| Contact US: help@patsnap.com