High-temperature proton membrane catalyst, and preparation method and application thereof
A proton membrane and catalyst technology, applied in the direction of catalyst activation/preparation, chemical instruments and methods, physical/chemical process catalysts, etc., to reduce sintering problems, improve life, and improve activity
- Summary
- Abstract
- Description
- Claims
- Application Information
AI Technical Summary
Problems solved by technology
Method used
Image
Examples
Embodiment 1
[0027] The preparation of a high-temperature proton membrane catalyst precursor comprises the following steps:
[0028] 1) Weigh 3.487g of samarium oxide and 3.442g of cerium oxide, mix the samarium oxide and cerium oxide evenly, and then grind for 2 hours to obtain uniformly mixed samarium oxide and cerium oxide powder;
[0029] 2) The powder obtained in step 1) was calcined at 500°C for 12 hours in an argon atmosphere, and then naturally cooled to room temperature. After the calcined product was ball-milled again, it was shaken and sieved. Calcined again at 1200°C for 10 hours to form a solid solution and obtain a dense ceramic film;
[0030]3) Weigh 0.28g RuCl 3 Dissolve in 5.0mL deionized water to prepare impregnating liquid, apply the impregnating liquid evenly on one side wall surface of the ceramic membrane obtained in step 2) to make it reach saturation of water absorption, after impregnating at room temperature for 12 hours, place in an oven at 110°C Dry for 12h. T...
Embodiment 2
[0032] The preparation of a high-temperature proton membrane catalyst precursor comprises the following steps:
[0033] 1) Weigh 3.258g of lanthanum oxide and 2.092g of germanium oxide, mix the lanthanum oxide and germanium oxide evenly, and then grind for 3 hours to obtain uniformly mixed lanthanum oxide and germanium oxide powders;
[0034] 2) The powder obtained in step 1) was calcined at 600°C for 16 hours in an argon atmosphere, and then cooled to room temperature naturally. Calcined again at 1500°C for 15 hours to form a solid solution and obtain a dense ceramic film;
[0035] 3) Weigh 0.22g RuCl 3 Dissolve in 5.0mL deionized water to prepare impregnating liquid A, and apply impregnating liquid A evenly on one side wall surface of the ceramic membrane obtained in step 2) to make it reach water absorption saturation, and place it in an oven after immersing at room temperature for 12 hours Dry at 110°C for 12h. The above impregnation steps are repeated until the impregn...
Embodiment 3
[0038] The preparation of a high-temperature proton membrane catalyst precursor comprises the following steps:
[0039] 1) Weigh 3.365g of neodymium oxide and 3.442g of cerium oxide, mix the neodymium oxide and cerium oxide evenly, and then grind for 2 hours to obtain uniformly mixed neodymium oxide and cerium oxide powder;
[0040] 2) The powder obtained in step 1) was calcined at 800°C for 8 hours in an argon atmosphere, and then naturally cooled to room temperature. After the calcined product was ball-milled again, it was vibrated and screened. Calcined again at 1400°C for 10 hours to form a solid solution and obtain a dense ceramic film;
[0041] 3) Weigh 0.28g RuCl 3 ·3H 2 O was dissolved in 5.0mL deionized water to prepare an impregnating solution, and the impregnating solution was uniformly drip-coated on one side wall of the ceramic membrane obtained in step 2) to make it reach saturated water absorption. After immersing at room temperature for 12 hours, place it in ...
PUM
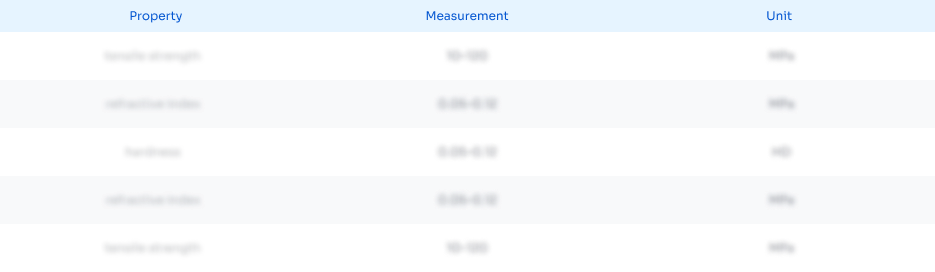
Abstract
Description
Claims
Application Information

- Generate Ideas
- Intellectual Property
- Life Sciences
- Materials
- Tech Scout
- Unparalleled Data Quality
- Higher Quality Content
- 60% Fewer Hallucinations
Browse by: Latest US Patents, China's latest patents, Technical Efficacy Thesaurus, Application Domain, Technology Topic, Popular Technical Reports.
© 2025 PatSnap. All rights reserved.Legal|Privacy policy|Modern Slavery Act Transparency Statement|Sitemap|About US| Contact US: help@patsnap.com