Nickel base alloy powder used for coating and preparing method of nickel base alloy powder used for coating
A nickel-based alloy and powder technology, applied in the field of nickel-based alloy powder for coating and its preparation, can solve problems such as poor performance of nickel-based alloy layer, and achieve the effects of reducing the melting point of the alloy, increasing wear resistance, and improving crack resistance
- Summary
- Abstract
- Description
- Claims
- Application Information
AI Technical Summary
Problems solved by technology
Method used
Examples
Embodiment 1
[0031] A nickel-based alloy powder for coating, comprising the following raw materials in parts by weight:
[0032] 1-5% magnesium, 35-45% cobalt, 7-10% chromium, 2-5% molybdenum, 2-5% boron, 3-5% silicon, 40-50% nickel, magnesium, cobalt, chromium, molybdenum, Boron, silicon and nickel are corresponding proportions of magnesium sulfate hydrate, cobalt nitrate hexahydrate, chromium nitrate nonahydrate, molybdenum nitrate pentahydrate, boron powder, silicon dioxide and nickel nitrate hexahydrate.
[0033] A preparation method of nickel-based alloy powder for coating, comprising the following steps:
[0034] Preparation of matrix alloy The process flow of matrix alloy powder preparation is: batching→centrifugation→atomization→sieving→grinding→mixing→drying→sieving;
[0035] 1) Ingredients: Take the corresponding proportion of magnesium sulfate water, cobalt nitrate hexahydrate, chromium nitrate nonahydrate, molybdenum nitrate pentahydrate, boron powder, silicon dioxide and nick...
Embodiment 2
[0045] A nickel-based alloy powder for coating, comprising the following raw materials in parts by weight:
[0046] 2-5% magnesium, 37-45% cobalt, 8-10% chromium, 3-5% molybdenum, 3-5% boron, 3-5% silicon, 40-50% nickel, magnesium, cobalt, chromium, molybdenum, Boron, silicon and nickel are corresponding proportions of magnesium sulfate hydrate, cobalt nitrate hexahydrate, chromium nitrate nonahydrate, molybdenum nitrate pentahydrate, boron powder, silicon dioxide and nickel nitrate hexahydrate.
[0047] A preparation method of nickel-based alloy powder for coating, comprising the following steps:
[0048] Preparation of matrix alloy The process flow of matrix alloy powder preparation is: batching→centrifugation→atomization→sieving→grinding→mixing→drying→sieving;
[0049]1) Ingredients: Take the corresponding proportion of magnesium sulfate water, cobalt nitrate hexahydrate, chromium nitrate nonahydrate, molybdenum nitrate pentahydrate, boron powder, silicon dioxide and nicke...
Embodiment 3
[0059] A nickel-based alloy powder for coating, comprising the following raw materials in parts by weight:
[0060] Magnesium 4-5%, cobalt 40-45%, chromium 9-10%, molybdenum 4-5%, boron 3-5%, silicon 4-5%, nickel 45-50%, magnesium, cobalt, chromium, molybdenum, Boron, silicon and nickel are corresponding proportions of magnesium sulfate hydrate, cobalt nitrate hexahydrate, chromium nitrate nonahydrate, molybdenum nitrate pentahydrate, boron powder, silicon dioxide and nickel nitrate hexahydrate.
[0061] A preparation method of nickel-based alloy powder for coating, comprising the following steps:
[0062] Preparation of matrix alloy The process flow of matrix alloy powder preparation is: batching→centrifugation→atomization→sieving→grinding→mixing→drying→sieving;
[0063] 1) Ingredients: Take the corresponding proportion of magnesium sulfate water, cobalt nitrate hexahydrate, chromium nitrate nonahydrate, molybdenum nitrate pentahydrate, boron powder, silicon dioxide and nick...
PUM
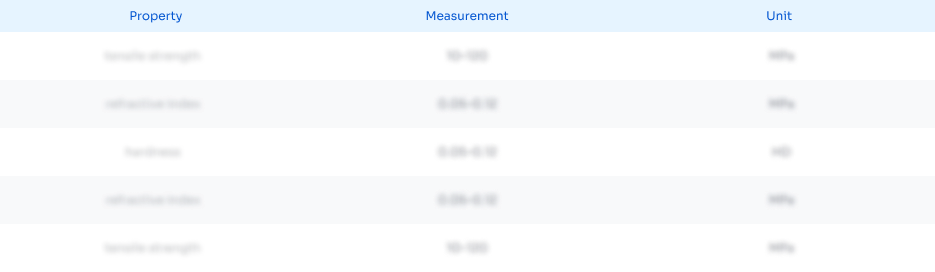
Abstract
Description
Claims
Application Information

- R&D
- Intellectual Property
- Life Sciences
- Materials
- Tech Scout
- Unparalleled Data Quality
- Higher Quality Content
- 60% Fewer Hallucinations
Browse by: Latest US Patents, China's latest patents, Technical Efficacy Thesaurus, Application Domain, Technology Topic, Popular Technical Reports.
© 2025 PatSnap. All rights reserved.Legal|Privacy policy|Modern Slavery Act Transparency Statement|Sitemap|About US| Contact US: help@patsnap.com