Austenitic stainless steel as well as preparation method thereof and application thereof
An austenitic stainless steel, mass percentage technology, applied in the field of austenitic stainless steel and its preparation, can solve the problems of the rise of irradiated DBTT, the corrosion and embrittlement of liquid lead and bismuth, and the difficulty of technical improvement, and achieves the removal of inclusions, microstructures and other problems. The effect of good stability, excellent resistance to lead and lead-bismuth liquid metal corrosion and radiation resistance
- Summary
- Abstract
- Description
- Claims
- Application Information
AI Technical Summary
Problems solved by technology
Method used
Image
Examples
preparation example Construction
[0033] The preparation method of the austenitic stainless steel of the present invention can be obtained by adopting vacuum induction melting and vacuum arc consumable remelting process to obtain consumable remelted ingot, and then adopting the method of forging to obtain the ingot billet.
[0034] Specifically, the preparation method may include the following steps:
[0035] S1. Vacuum induction melting and vacuum arc consumable remelting are performed on raw materials of austenitic stainless steel to obtain consumable remelting ingots.
[0036] Step S1 may further include the following steps:
[0037] S1.1. Select polysilicon, nickel plate, pure iron, metal molybdenum strip, metal chromium, carbon, boron-iron alloy, metal manganese and sponge titanium as raw materials. Wherein, the mass percentage of the boron element in the boron-iron alloy is 15-20%.
[0038] Weigh each raw material according to the content of each component in the austenitic stainless steel.
[0039] S...
Embodiment 1-3
[0073] Table 4. Embodiment 1-3 alloy forging deformation process parameters
[0074]
[0075]
[0076] The chemical composition (%) of the austenitic stainless steel that table 5. embodiment 1-3 obtains
[0077]
[0078]
[0079] The austenitic stainless steel of Examples 1-3 was subjected to multi-pass cold rolling deformation and intermediate annealing treatment, and finally retained 20% of the cold deformation. The tensile properties of each example at room temperature, 450°C and 550°C are shown in Table 6 . The austenitic stainless steel components of the three examples all have relatively high strength and good plasticity, meeting the performance requirements of the present invention.
[0080] Table 6. Room temperature and medium temperature tensile properties of the austenitic stainless steels of Examples 1-3
[0081]
PUM
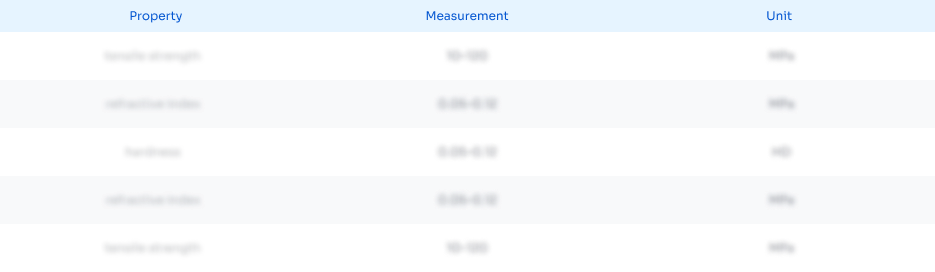
Abstract
Description
Claims
Application Information

- Generate Ideas
- Intellectual Property
- Life Sciences
- Materials
- Tech Scout
- Unparalleled Data Quality
- Higher Quality Content
- 60% Fewer Hallucinations
Browse by: Latest US Patents, China's latest patents, Technical Efficacy Thesaurus, Application Domain, Technology Topic, Popular Technical Reports.
© 2025 PatSnap. All rights reserved.Legal|Privacy policy|Modern Slavery Act Transparency Statement|Sitemap|About US| Contact US: help@patsnap.com