Pretreatment process of vacuum ruthenium plating technology
A kind of pretreatment and technical technology, applied in the direction of vacuum evaporation plating, metal material coating process, sputtering plating, etc., can solve the problems of high pollution, poor adhesion effect, etc., to reduce oxygen content, connect The effect is uniform and strong, and the effect of increasing firmness
- Summary
- Abstract
- Description
- Claims
- Application Information
AI Technical Summary
Problems solved by technology
Method used
Image
Examples
Embodiment 1
[0028] A pretreatment process of vacuum ruthenium plating technology, according to the following steps:
[0029] Step 1, put the molybdenum sheet into the electrolytic cell for electrolytic degreasing reaction, and then rinse it with pure water;
[0030] The electrolytic solution in the electrolytic cell adopts mixed lye, and described mixed lye is mixed by sodium hydroxide solution and sodium carbonate solution, and the concentration of sodium hydroxide in described mixed lye is 10g / L, and the concentration of sodium carbonate is 20g / L. L; the temperature of the electrolytic degreasing is 70°C, the time is 2min, and the current density of the electrolytic degreasing is 50mA / cm 2 ;
[0031] Step 2, adding the rinsed molybdenum sheet into the mixed acid solution for surface film removal treatment, and rinsing with pure water after treatment;
[0032] The mixed acid solution adopts a mixture of hydrochloric acid, sulfuric acid and water, and the mass ratio of hydrochloric acid...
Embodiment 2
[0038] A pretreatment process of vacuum ruthenium plating technology, according to the following steps:
[0039] Step 1, put the molybdenum sheet into the electrolytic cell for electrolytic degreasing reaction, and then rinse it with pure water;
[0040] The electrolytic solution in the electrolytic cell adopts mixed lye, and described mixed lye is mixed by sodium hydroxide solution and sodium carbonate solution, and the concentration of sodium hydroxide in described mixed lye is 20g / L, and the concentration of sodium carbonate is 30g / L. L; the temperature of the electrolytic degreasing is 70°C, the time is 2min, and the current density of the electrolytic degreasing is 50mA / cm 2 ;
[0041] Step 2, adding the rinsed molybdenum sheet into the mixed acid solution for surface film removal treatment, and rinsing with pure water after treatment;
[0042] The mixed acid solution adopts a mixture of hydrochloric acid, sulfuric acid and water, and the mass ratio of hydrochloric acid...
Embodiment 3
[0048] A pretreatment process of vacuum ruthenium plating technology, according to the following steps:
[0049] Step 1, put the molybdenum sheet into the electrolytic cell for electrolytic degreasing reaction, and then rinse it with pure water;
[0050] The electrolytic solution in the electrolytic cell adopts mixed lye, and described mixed lye is mixed by sodium hydroxide solution and sodium carbonate solution, and the concentration of sodium hydroxide in described mixed lye is 20g / L, and the concentration of sodium carbonate is 30g / L. L; the temperature of the electrolytic degreasing is 70°C, the time is 2min, and the current density of the electrolytic degreasing is 50mA / cm 2 ;
[0051] Step 2, adding the rinsed molybdenum sheet into the mixed acid solution for surface film removal treatment, and rinsing with pure water after treatment;
[0052] The mixed acid solution adopts a mixture of hydrochloric acid, sulfuric acid and water, and the mass ratio of hydrochloric acid, ...
PUM
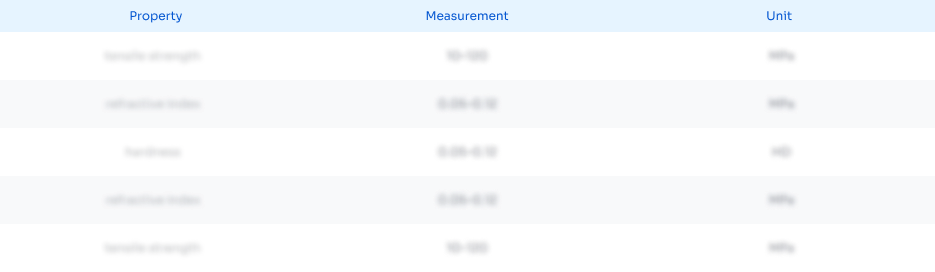
Abstract
Description
Claims
Application Information

- R&D
- Intellectual Property
- Life Sciences
- Materials
- Tech Scout
- Unparalleled Data Quality
- Higher Quality Content
- 60% Fewer Hallucinations
Browse by: Latest US Patents, China's latest patents, Technical Efficacy Thesaurus, Application Domain, Technology Topic, Popular Technical Reports.
© 2025 PatSnap. All rights reserved.Legal|Privacy policy|Modern Slavery Act Transparency Statement|Sitemap|About US| Contact US: help@patsnap.com