Anti-corrosive coating for surface layer of electrical equipment and preparation method ofanti-corrosive coating
A technology for power equipment and anti-corrosion coatings, applied in anti-corrosion coatings, epoxy resin coatings, polyurea/polyurethane coatings, etc., can solve the problems of accelerating anti-corrosion coating oxidation, anti-corrosion coating aging, chapping and falling off, etc., to achieve easy filling and processing, and improve durability Abrasion resistance and anti-aging performance, good adhesion effect
- Summary
- Abstract
- Description
- Claims
- Application Information
AI Technical Summary
Problems solved by technology
Method used
Examples
Embodiment 1
[0026] An anti-corrosion coating for the surface layer of electric equipment, comprising the following raw materials in parts by weight:
[0027] 25 parts of epoxy resin, 15 parts of polyurethane resin, 30 parts of polyacrylic resin, 5 parts of polydimethylsiloxane, 4 parts of dibutyl phthalate, 6 parts of mica, 3 parts of red clay, 5 parts of bentonite, talc 4 parts of powder, 4 parts of graphene, 3 parts of zinc powder, 3 parts of zinc oxide, 3 parts of aluminum oxide, 4 parts of glass fiber, 3 parts of nano-titanium dioxide, 3 parts of nano-silicon carbide, 2 parts of microcrystalline paraffin, butyl stearate 2 parts of ester, 10 parts of acetone, 2 parts of sodium dodecylsulfonate, 1.5 parts of silane coupling agent, 1.2 parts of defoamer, 1.8 parts of antioxidant, 2.1 parts of heat stabilizer and 1.5 parts of ultraviolet absorber.
[0028] The silane coupling agent is vinyltriethoxysilane.
[0029] The defoamer is polyoxyethylene polyoxypropylene pentaerythritol ether. ...
Embodiment 2
[0039] An anti-corrosion coating for the surface layer of electric equipment, comprising the following raw materials in parts by weight:
[0040] 35 parts of epoxy resin, 25 parts of polyurethane resin, 40 parts of polyacrylic resin, 10 parts of polydimethylsiloxane, 8 parts of dibutyl phthalate, 10 parts of mica, 6 parts of red clay, 10 parts of bentonite, talc 8 parts of powder, 8 parts of graphene, 6 parts of zinc powder, 6 parts of zinc oxide, 6 parts of aluminum oxide, 8 parts of glass fiber, 6 parts of nano-titanium dioxide, 6 parts of nano-silicon carbide, 4 parts of microcrystalline paraffin, butyl stearate 4 parts of ester, 15 parts of acetone, 4 parts of sodium dodecylsulfonate, 3.6 parts of silane coupling agent, 2.8 parts of defoamer, 3.8 parts of antioxidant, 4.2 parts of heat stabilizer and 3.2 parts of ultraviolet absorber.
[0041] The silane coupling agent is 3-glycidyloxypropyltrimethoxysilane.
[0042] The defoamer is composed of polyoxyethylene polyoxyprop...
Embodiment 3
[0052] An anti-corrosion coating for the surface layer of electric equipment, comprising the following raw materials in parts by weight:
[0053] 32 parts of epoxy resin, 20 parts of polyurethane resin, 36 parts of polyacrylic resin, 8 parts of polydimethylsiloxane, 6.5 parts of dibutyl phthalate, 8 parts of mica, 4 parts of red clay, 8 parts of bentonite, talc 6 parts of powder, 6.5 parts of graphene, 5 parts of zinc powder, 4 parts of zinc oxide, 5 parts of aluminum oxide, 6 parts of glass fiber, 4.5 parts of nano-titanium dioxide, 5 parts of nano-silicon carbide, 3.5 parts of microcrystalline paraffin, butyl stearate 3.5 parts of ester, 13 parts of acetone, 3.2 parts of sodium dodecylsulfonate, 2.8 parts of silane coupling agent, 2.1 parts of defoamer, 3.4 parts of antioxidant, 3.8 parts of heat stabilizer and 2.8 parts of ultraviolet absorber.
[0054] The silane coupling agent is vinyltris(β-methoxyethoxy)silane.
[0055] The defoamer is polyoxypropylene oxide ethylene g...
PUM
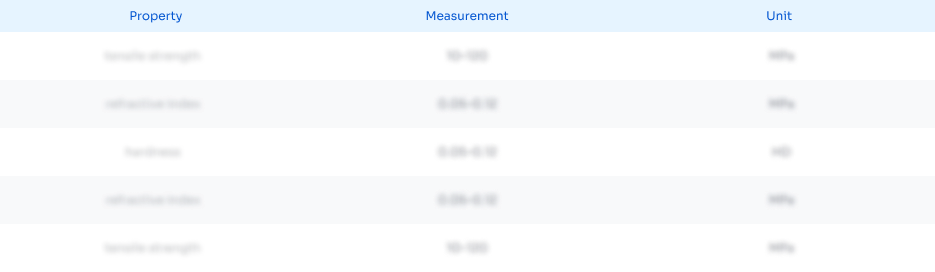
Abstract
Description
Claims
Application Information

- R&D
- Intellectual Property
- Life Sciences
- Materials
- Tech Scout
- Unparalleled Data Quality
- Higher Quality Content
- 60% Fewer Hallucinations
Browse by: Latest US Patents, China's latest patents, Technical Efficacy Thesaurus, Application Domain, Technology Topic, Popular Technical Reports.
© 2025 PatSnap. All rights reserved.Legal|Privacy policy|Modern Slavery Act Transparency Statement|Sitemap|About US| Contact US: help@patsnap.com