High-tensile-strength polyurethane and preparation method thereof
A polyurethane and strength technology, applied in the field of polyurethane with high tensile strength and its preparation, can solve the problems of insufficient tensile strength of polyurethane
- Summary
- Abstract
- Description
- Claims
- Application Information
AI Technical Summary
Problems solved by technology
Method used
Examples
preparation example Construction
[0020] The preparation method of the polyurethane of described high tensile strength, comprises the following steps:
[0021] S1. Mix polyurethane, polyester polyol and ethylene vinyl acetate evenly, stir at 850-1050r / min for 10-30min, heat up to 80-90°C, keep warm for 20-40min, then add polycarbonate diol, Polyester polyol, hydroxyl-terminated polybutadiene, polyphenylene sulfide, methacrylic acid, low-density polyethylene, chlorinated paraffin, pine tar, nano ceramic powder, nano boron nitride, zinc borate, aluminum tripolyphosphate, Mix nano-alumina, calcium sulfate whiskers, nano-attapulgite, silica powder, talc powder, heavy calcium, nano-calcium carbonate, and perlite evenly, and cool to room temperature after ball milling to obtain the base material;
[0022] S2. Mix microcrystalline stone, glass fiber, silane coupling agent KH-560, and tensile reinforcement modification additive evenly, heat up to 110-120°C, keep warm for 5-15min, and cool to room temperature to obtain...
Embodiment 1
[0026]A polyurethane with high tensile strength, in parts by weight, comprising the following raw materials: 85 parts of polyurethane, 30 parts of polyester polyol, 10 parts of ethylene vinyl acetate, 12 parts of polycarbonate diol, polyester polyol 6.5 parts, 4.5 parts of hydroxyl-terminated polybutadiene, 4 parts of polyphenylene sulfide, 3 parts of methacrylic acid, 6 parts of low-density polyethylene, 6 parts of chlorinated paraffin, 4.5 parts of pine tar, 4 parts of nano ceramic powder, nano 3 parts of boron nitride, 6 parts of zinc borate, 4 parts of aluminum tripolyphosphate, 3 parts of nano-alumina, 6 parts of calcium sulfate whiskers, 4.5 parts of nano-attapulgite, 3.5 parts of silicon micropowder, 3 parts of talcum powder, heavy calcium 6 parts, 4.5 parts of nano-calcium carbonate, 3.5 parts of perlite, 13 parts of microcrystalline stone, 7 parts of glass fiber, 2.5 parts of silane coupling agent KH-560, 12 parts of tensile reinforcement modification additive.
[002...
Embodiment 2
[0033] A polyurethane with high tensile strength, in parts by weight, comprising the following raw materials: 80 parts of polyurethane, 40 parts of polyester polyol, 5 parts of ethylene vinyl acetate, 16 parts of polycarbonate diol, polyester polyol 4 parts, 6 parts of hydroxyl-terminated polybutadiene, 2 parts of polyphenylene sulfide, 5 parts of methacrylic acid, 3 parts of low-density polyethylene, 8 parts of chlorinated paraffin, 3 parts of pine tar, 6 parts of nano ceramic powder, nano 1 part of boron nitride, 9 parts of zinc borate, 2 parts of aluminum tripolyphosphate, 5 parts of nano-alumina, 4 parts of calcium sulfate whiskers, 6 parts of nano-attapulgite, 2 parts of silicon micropowder, 5 parts of talc powder, heavy calcium 4 parts, 6 parts of nano-calcium carbonate, 2 parts of perlite, 14 parts of microcrystalline stone, 6 parts of glass fiber, 3 parts of silane coupling agent KH-560, 8 parts of tensile reinforcement modification additive.
[0034] The tensile stren...
PUM
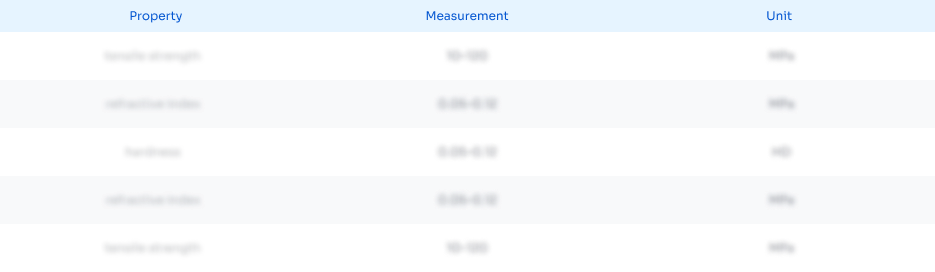
Abstract
Description
Claims
Application Information

- R&D
- Intellectual Property
- Life Sciences
- Materials
- Tech Scout
- Unparalleled Data Quality
- Higher Quality Content
- 60% Fewer Hallucinations
Browse by: Latest US Patents, China's latest patents, Technical Efficacy Thesaurus, Application Domain, Technology Topic, Popular Technical Reports.
© 2025 PatSnap. All rights reserved.Legal|Privacy policy|Modern Slavery Act Transparency Statement|Sitemap|About US| Contact US: help@patsnap.com