Purifying method of pulp electrolyte containing antimony concentrates
A technology of electrolyte and pulp, applied in the field of purification of pulp electrolyte, can solve the problems of slow stripping speed, increased treatment, insufficient phase separation time, etc., to reduce emulsification and aging, prolong the service period, and realize the effect of recycling.
- Summary
- Abstract
- Description
- Claims
- Application Information
AI Technical Summary
Problems solved by technology
Method used
Image
Examples
Embodiment 1
[0028] The ore slurry electrolyte composition of the antimony concentrate that the present invention adopts is following mass concentration (unit g / L): Fe 2+ 26.01, Fe 3+ 0.68, Sn 0.035, SiO 2 0.18, As 0.048, Sb 32.27, H + 28.53. Follow these steps:
[0029] Step A: Under the condition of oxidation temperature of 40°C and stirring time of 300 minutes, oxidant air is blown in, and activated carbon is added to absorb for 5 minutes at the end of the reaction, and Fe in the oxidation solution 3+ , Fe 2+ , Sb mass concentrations were 8g / L, 18.37g / L and 32.08g / L.
[0030] Step B: The extraction is a two-stage extraction. The organic phase of the extraction is a mixed organic phase composed of P204 with a volume fraction of 25%, 200# kerosene with a volume fraction of 74%, and TBP with a volume fraction of 1%. The volume ratio of the organic phase to the aqueous phase is 1 : 2, extraction time is 15 minutes, temperature is 15 ℃, clarification time 10 minutes; Gained raffina...
Embodiment 2
[0037] The ore slurry electrolyte composition of the antimony concentrate that the present invention adopts is following mass concentration (unit g / L): Fe 2+ 26.01, Fe 3+ 0.68, Sn 0.035, SiO 2 0.18, As 0.048, Sb 32.27, H + 28.53. Follow these steps:
[0038] Step A: Under the conditions of oxidation temperature 75°C and stirring time of 60 minutes, oxidant oxygen is blown in, and at the end of the reaction, activated carbon is added for adsorption for 10 minutes, and Fe in the oxidation solution 3+ , Fe 2+ , Sb mass concentrations were 13g / L, 14.08g / L and 32.31g / L.
[0039] Step B: the extraction is a two-stage extraction, and the extracted organic phase is a mixed organic phase composed of P204 with a volume fraction of 35%, sulfonated common kerosene with a volume fraction of 64% and TBP with a volume fraction of 1%, and the volume of the organic phase and the aqueous phase is The ratio is 1:4, the extraction time is 5 minutes, the temperature is 40°C, and the clar...
Embodiment 3
[0046] The ore slurry electrolyte composition of the antimony concentrate that the present invention adopts is following mass concentration (unit g / L): Fe 2+ 26.01, Fe 3+ 0.68, Sn 0.035, SiO 2 0.18, As 0.048, Sb 32.27, H + 28.53. Follow these steps:
[0047] Step A: Under the condition of oxidation temperature of 60°C and stirring time of 150 minutes, oxidant air is blown in, and activated carbon is added to absorb for 5 minutes at the end of the reaction, and Fe in the oxidation solution 3+ , Fe 2+ , Sb mass concentrations were 10g / L, 16.76g / L and 32.36g / L.
[0048] Step B: The extraction is a 3-stage extraction, and the extracted organic phase is a mixed organic phase composed of P204 with a volume fraction of 30%, 200# kerosene with a volume fraction of 68%, and TBP with a volume fraction of 2%, and the volume ratio of the organic phase to the aqueous phase is 1 : 3, the extraction time is 10 minutes, the temperature is 25 ℃, and the clarification time is 20 minut...
PUM
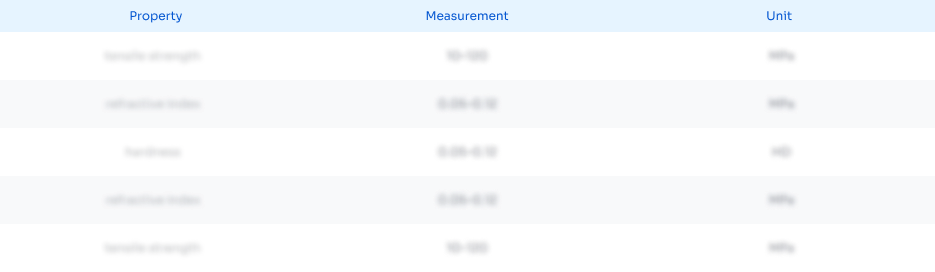
Abstract
Description
Claims
Application Information

- R&D
- Intellectual Property
- Life Sciences
- Materials
- Tech Scout
- Unparalleled Data Quality
- Higher Quality Content
- 60% Fewer Hallucinations
Browse by: Latest US Patents, China's latest patents, Technical Efficacy Thesaurus, Application Domain, Technology Topic, Popular Technical Reports.
© 2025 PatSnap. All rights reserved.Legal|Privacy policy|Modern Slavery Act Transparency Statement|Sitemap|About US| Contact US: help@patsnap.com