Abrasive block for high-speed multiple unit trains and preparation method
A high-speed motor car, composite material technology, applied in the field of grinding, can solve problems such as easy wear and tear, sparks, etc.
- Summary
- Abstract
- Description
- Claims
- Application Information
AI Technical Summary
Problems solved by technology
Method used
Examples
Embodiment 1
[0013] Weighing by weight percentage: phenolic resin 27%, steel fiber 10%, copper aluminum powder 14%, carbon fiber 10%, tungsten carbide 2%, aramid fiber 8.5%, iron oxide black 8.5%, nitrile rubber 8%, accelerator 12%, mix evenly, put into molding equipment.
[0014] Processing technology: pressure 20Mpa, temperature 120°C, first deflation after 10 seconds after pressurization, second deflation after pressure holding for 15 seconds, third deflation after pressure holding for 15 seconds, and pressure holding for 15 minutes to release the mold.
[0015] Curing, 80°C, constant temperature for 1 hour, 95°C, constant temperature for 2 hours, 110°C, constant temperature for 3 hours, temperature 120°C, constant temperature for 4 hours, 165°C for 6 hours.
Embodiment 2
[0017] Weighing by weight percentage: phenolic resin 26%, steel fiber 10%, copper aluminum powder 15%, carbon fiber 11%, tungsten carbide 1.5%, aramid fiber 8.5%, iron oxide black 8%, nitrile rubber 7%, accelerator 13%, mix well, put into molding equipment.
[0018] Processing technology: pressure 20Mpa, temperature 120°C, first deflation after 10 seconds after pressurization, second deflation after pressure holding for 15 seconds, third deflation after pressure holding for 15 seconds, and pressure holding for 15 minutes to release the mold.
[0019] Curing, 80°C, constant temperature for 1 hour, 95°C, constant temperature for 2 hours, 110°C, constant temperature for 3 hours, temperature 120°C, constant temperature for 4 hours, 165°C for 6 hours.
Embodiment 3
[0021] Weighing by weight percentage: phenolic resin 27.5%, steel fiber 9.5%, copper aluminum powder 15.5%, carbon fiber 12%, tungsten carbide 2%, aramid fiber 8.5%, iron oxide black 6%, nitrile rubber 7%, accelerator 12%, mix well, put into molding equipment.
[0022] Processing technology: pressure 20Mpa, temperature 120°C, first deflation after 10 seconds after pressurization, second deflation after pressure holding for 15 seconds, third deflation after pressure holding for 15 seconds, and pressure holding for 15 minutes to release the mold.
[0023] Curing, 80°C, constant temperature for 1 hour, 95°C, constant temperature for 2 hours, 110°C, constant temperature for 3 hours, temperature 120°C, constant temperature for 4 hours, 165°C for 6 hours.
[0024] Based on the above, the present invention has the advantage of avoiding high-temperature stress cracks, thermal cracks, and friction sparks during the use of the grinding wheel by optimizing the composition ratio and proce...
PUM
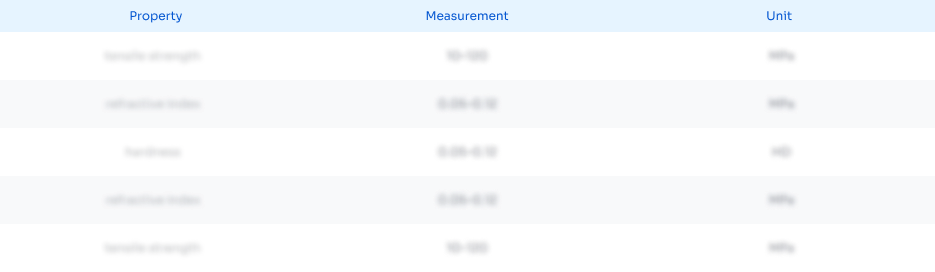
Abstract
Description
Claims
Application Information

- R&D
- Intellectual Property
- Life Sciences
- Materials
- Tech Scout
- Unparalleled Data Quality
- Higher Quality Content
- 60% Fewer Hallucinations
Browse by: Latest US Patents, China's latest patents, Technical Efficacy Thesaurus, Application Domain, Technology Topic, Popular Technical Reports.
© 2025 PatSnap. All rights reserved.Legal|Privacy policy|Modern Slavery Act Transparency Statement|Sitemap|About US| Contact US: help@patsnap.com